When it comes to measuring residual stress in small test specimens, precision is paramount. The slitting method is well suited to this application due to the high accuracy of wire EDM machining. However, this method is not without its challenges, especially when applied to very small test specimens, such as the 0.022-inch diameter wire we recently measured.
Continue reading Overcoming Challenges in Residual Stress Measurements on Small Test Specimens Using the Slitting MethodTag: Residual Stress Measurement
Search results for Hill Engineering blog posts containing the tag residual stress measurement
New publication: Effects of high‑energy laser peening followed by pre‑hot corrosion on stress relaxation, microhardness, and fatigue life and strength of single‑crystal nickel CMSX‑4® superalloy
Hill Engineering recently published new collaborative research in the International Journal of Advanced Manufacturing Technology titled Effects of high‑energy laser peening followed by pre‑hot corrosion on stress relaxation, microhardness, and fatigue life and strength of single‑crystal nickel CMSX‑4® superalloy and appears in International Journal of Advanced Manufacturing Technology. The abstract text is available here along with a link to the publication.
Continue reading New publication: Effects of high‑energy laser peening followed by pre‑hot corrosion on stress relaxation, microhardness, and fatigue life and strength of single‑crystal nickel CMSX‑4® superalloyNew Vlog: How To Apply A Strain Gage
Strain gages feature in a large portion of the residual stress measurements we perform at Hill Engineering, which is why we pride ourselves on our ability to correctly choose and apply strain gages to fit any measurement needs.
Continue reading New Vlog: How To Apply A Strain GagePublication alert – Multiscale framework for prediction of residual stress in additively manufactured functionally graded material
Hill Engineering recently published new research with collaborators from around the world including South Korea, Australia, China, and the United Kingdom. The work is titled Multiscale framework for prediction of residual stress in additively manufactured functionally graded material. The abstract text is available here along with a link to the publication.
Continue reading Publication alert – Multiscale framework for prediction of residual stress in additively manufactured functionally graded materialHill Engineering’s DART issued second US patent!
Hill Engineering has been recently issued its second US patent for the DART™ measurement system. This updated device offers improved residual stress measurements within small-diameter pipe applications, allowing for more accurate analysis in both in-laboratory and non-laboratory settings.
Continue reading Hill Engineering’s DART issued second US patent!New Case Study – TrueSlot®
Our latest case study is up and it’s all about TrueSlot®, our innovative technique for measuring near-surface residual stress!
Continue reading New Case Study – TrueSlot®Hill Engineering issued first Japanese patent for the DART!
Hill Engineering is officially going global!
We are proud to announce we’ve been issued our first Japanese patent for the DART™, our Device for Automated Residual stress Testing.
Continue reading Hill Engineering issued first Japanese patent for the DART!TrueSlot® – near surface residual stress measurement
TrueSlot® is an innovative technique for measuring near-surface residual stress that is more reliable than conventional techniques.
TrueSlot® is a residual stress measurement technique for generating a profile of residual stress versus depth from the material surface. The stress computation is similar to slitting but offers more sensitivity near the surface due to the proximity of the strain gage.
Additionally, TrueSlot® is globally less invasive than slitting because the volume of removed material is localized to the surface and does not typically extend through most of the specimen thickness.
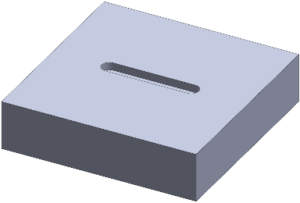
The physical application of TrueSlot® is like hole drilling, however instead of a shallow hole being milled into the body of a specimen containing residual stress, the material removed is a shallow slot. The strain released with each incremental slot depth is measured near the slot using a strain gage.
TrueSlot® is useful for
- Production quality control applications
- Applications requiring in-field measurements with portable equipment
- Near-surface residual stress determination
- Parts with large or complex geometry
- Applications with challenging measurement access
- Applications requiring rapid turn time
TrueSlot® was found to have better repeatability when compared with conventional x-ray diffraction.
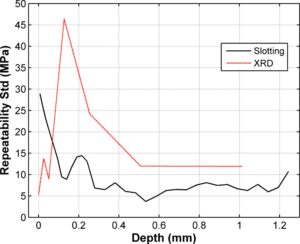
You can read about our repeatability study here.
TrueSlot® measurements are performed using our DARTTM system for automated residual stress measurement.
The Big 200! – Celebrating a milestone blog post
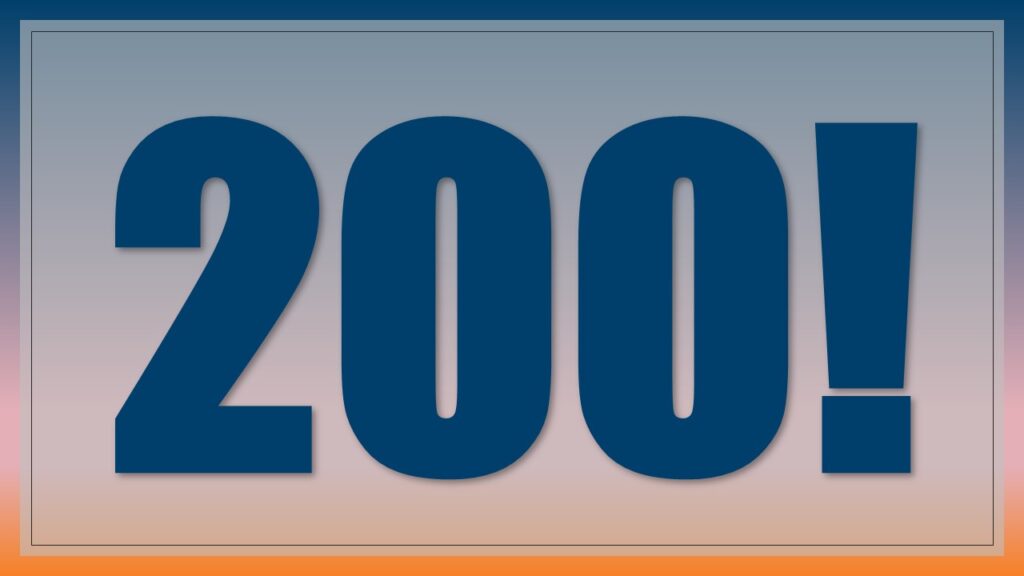
Gather round readers!
We are very excited today because in this blog we cross an incredible milestone: our 200th post! That’s right. Since the inception of the Hill Engineering blog back in March 2016, we have published 200 times.
Let’s take a look back over the past 7 years of blogging bliss!
Continue reading The Big 200! – Celebrating a milestone blog postNew Case Study: Express RS
Our latest case study highlights ExpressRS®, our dedicated service to high-priority, accelerated schedule projects.
Continue reading New Case Study: Express RS