In an early blog post, we discussed Hill Engineering’s efforts to build and maintain a Quality System that is compliant with ISO 17025. More recently, we touched on our quality control program, which we use as an important check to make sure that our measurements are being carried out according to established procedures and meeting certain quality requirements. Now we’re back to give another glimpse into our Quality System and talk about another important aspect, our internal audit program.
Continue reading A closer look at Hill Engineering’s internal audit program
Tag: residual stress
Search results for Hill Engineering blog posts containing the tag residual stress
Hill Engineering acquires a new XRD system
Hill Engineering has recently acquired a new diffractometer and enclosure that will enable us to perform x-ray diffraction (XRD) residual stress measurements in our Rancho Cordova, California, laboratory.
Continue reading Hill Engineering acquires a new XRD system
New case study: Residual Stress Field Team
We invite you to read our latest case study which highlights the capabilities of our Residual Stress Field Team, who can perform many of our world-class residual stress measurements on-site at a customer’s facility. Continue reading New case study: Residual Stress Field Team
Residual Stress Field Team
Hill Engineering is committed to providing high-quality residual stress measurement data to its customers, both in our laboratory and on-site. Our Residual Stress Field Team is equipped with the same knowledge and expertise as our laboratory team to meet the challenge of performing residual stress measurements in the field.
Our Residual Stress Field Team has the experience necessary to tailor each measurement approach to meet the unique needs of the customer and bring our world-class residual stress measurement capabilities to the place it matters most – the operational environment. Challenging measurement access, complex geometry, and applications requiring rapid turn time are just a few situations where our team and equipment excel, allowing us to assess both near-surface and bulk residual stress in components that are delicate, large, or otherwise unable to be sent to our laboratory for in-house testing.
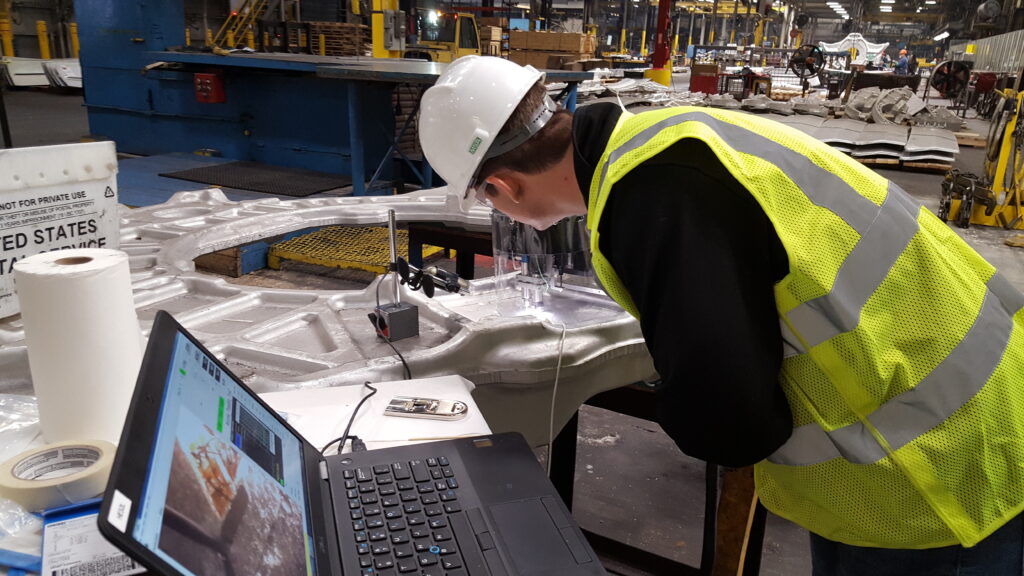
From a quality control perspective, measurements performed in the field allow customers to get a detailed glimpse of their manufacturing process, as measurements can be carried out shortly before or after a critical step, such as heat treatment, all without having the component leaving the manufacturing line, saving time for the customer.
On-site measurements and services that are available through our field team include:
The Hill Engineering Residual Stress Field Team, with its ability to perform on-site residual stress measurements, is just one of the ways we offer flexible, precise, and high-quality residual stress testing to our customers. Their mobility, coupled with advanced technology, ensures that the science of engineering is not confined to laboratories but can thrive in real-world environments where innovation truly takes flight.
If you have any questions about the capabilities of our Residual Stress Field Team and how it can help your project, please contact us.
2024 Turbine Engine Technology Symposium (TETS)
Hill Engineering will be presenting at the 2024 Turbine Engine Technology Symposium in Dayton, OH, from September 9th through September 12th. We invite you to come see us. The TETS symposium gathers approximately 1,000 engineers, scientists, managers, and operation personnel from throughout the turbine engine community every two years to review and discuss the latest turbine engine technology advances. Hill Engineering’s presentation will include a summary of recent work related to residual stress measurement on bearings using the TrueSlot® method. The abstract text is presented below.
Continue reading 2024 Turbine Engine Technology Symposium (TETS)
ERS-Toolbox® brochure
Hill Engineering’s ERS-Toolbox® software predicts the residual stress and distortion caused by surface treatment processes such as shot peening, laser shock peening (LSP), and cold hole expansion. This elegant computational design tool helps engineers and analysts design, analyze, and optimize the use of these processes, maximizing the performance of critical structural details.
Continue reading ERS-Toolbox® brochure
Two Decades of Excellence: Hill Engineering Celebrates 20 Years of Engineering Innovation
This year, Hill Engineering commemorates our 20th anniversary. This milestone is not just a reflection of time passed, but a testament to our unwavering commitment to engineering excellence. Since our inception, Hill Engineering has been on a mission to empower materials engineers, designers, and managers with the solid data needed to make sound decisions.
Discover Hill Engineering’s Latest Insights at SEM 2024
We are one month away from the 2024 SEM Annual Conference and Exposition on Experimental and Applied Mechanics, which means our presentation is fast approaching! Taking place in Vancouver, WA, from June 3rd through June 6th, this premier event offers an opportunity for professionals, researchers, and industry experts to come together, share insights, and explore the latest advancements in experimental mechanics.
Continue reading Discover Hill Engineering’s Latest Insights at SEM 2024
R&D Project: Strain gaging inside a tube
We are always trying to improve upon existing techniques and explore new methods so we can assure our customers that they are receiving the best services we have to offer.
After we spread out into our new laboratory space, we found some interesting things during the move that were hidden away. Something that caught our eye was a project a member of our lab team did, dealing with applying a strain gage to the inner diameter of a long tube with limited access.
Enhancing Efficiency: Hill Engineering’s scanning profilometer system
In the intricate world of residual stress analysis, the pursuit of precision is an ongoing endeavor. The Hill Engineering Scanning Profilometer (HESP) was a result of this perennial struggle, offering a satisfying, in-house solution that revolutionized our ability to perform contour method residual stress measurements.
Continue reading Enhancing Efficiency: Hill Engineering’s scanning profilometer system