Hill Engineering recently published new research with collaborators from around the world including South Korea, Australia, China, and the United Kingdom. The work is titled Multiscale framework for prediction of residual stress in additively manufactured functionally graded material. The abstract text is available here along with a link to the publication.
Continue reading Publication alert – Multiscale framework for prediction of residual stress in additively manufactured functionally graded materialTag: residual stress
Search results for Hill Engineering blog posts containing the tag residual stress
New Case Study – TrueSlot®
Our latest case study is up and it’s all about TrueSlot®, our innovative technique for measuring near-surface residual stress!
Continue reading New Case Study – TrueSlot®The Big 200! – Celebrating a milestone blog post
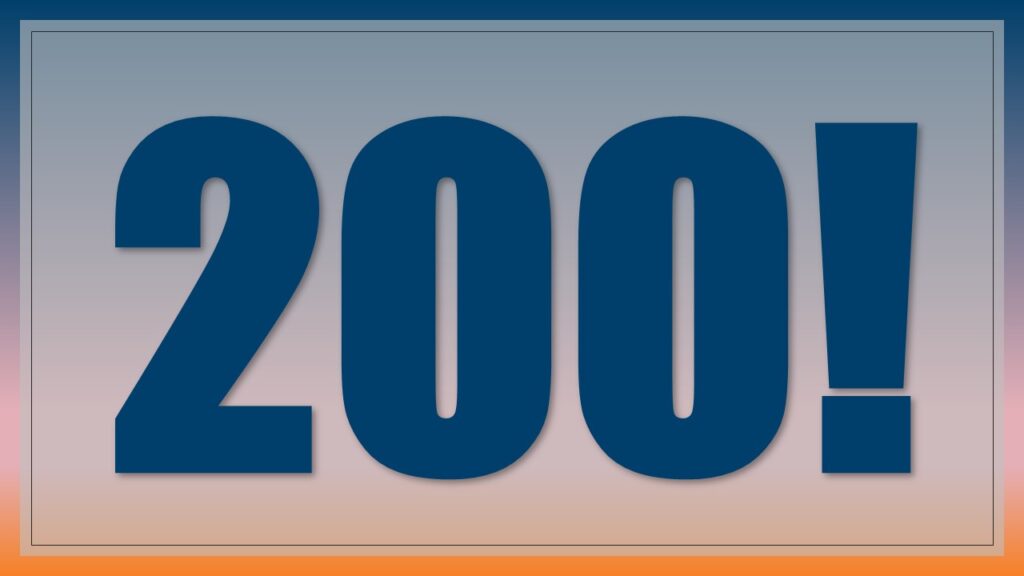
Gather round readers!
We are very excited today because in this blog we cross an incredible milestone: our 200th post! That’s right. Since the inception of the Hill Engineering blog back in March 2016, we have published 200 times.
Let’s take a look back over the past 7 years of blogging bliss!
Continue reading The Big 200! – Celebrating a milestone blog postNew Case Study: Express RS
Our latest case study highlights ExpressRS®, our dedicated service to high-priority, accelerated schedule projects.
Continue reading New Case Study: Express RSRenovations finished at Hill Engineering’s Utah office
Hill Engineering is happy to announce the completion of our Utah office renovations. Working with Gladwell Construction, a licensed general contractor based in Ogden, Utah, we created a thoughtfully designed and functional workspace with our employees, current projects, and future opportunities in mind. Thank you to Gladwell Construction for a job well done.
Continue reading Renovations finished at Hill Engineering’s Utah officeStrain Gaging Services
Strain gages are devices used to measure strain on the surface of an object. These strain measurements can be used to infer the amount of stress induced on the object, as is done with many types of residual stress measurements.
Additionally, strain gages can be used to measure things such as aircraft wing deflection, bridge cable creep, and tensile testing for material properties, making them an ideal tool for in-field measurements.
Strain gages come in many shapes and sizes and can measure strain in a single direction or in multiple directions, depending on the goal of the experiment. Strain gages can be used on a wide variety of materials under many conditions, such as in extreme temperatures or underwater.
Hill Engineering has extensive experience with strain gage application and can help design the experiment needed to reach your project’s goals. Strain gage application can be performed in our laboratory or at your site, to your specifications.
Strain gage application is useful for:
- Applications requiring in-field measurements with portable equipment
- Measuring strain in multiple directions
- Parts in every shape and size – nothing is too big or too small
- Measuring residual stress
If you’re interested in how we apply a strain gage to a simple specimen, watch our video:
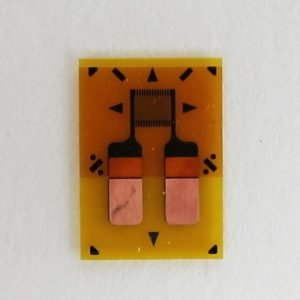
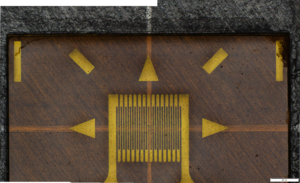
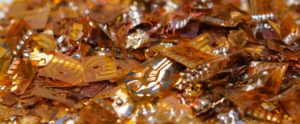
New case study: Residual Stress
The heart of work at Hill Engineering has everything to do with residual stress. That’s why we thought it was about time we published a case study giving a general overview of what residual stress is, and why it is so important for designers and manufacturers to consider.
Continue reading New case study: Residual StressResidual Stress
Residual stress is the stress present in a material in the absence of externally applied loading. These stresses can often form during manufacturing, and are typically an unintentional byproduct of a manufacturing process. Residual stresses can be caused by a number of factors, including plastic deformations, temperature cycles, or phase transformations.
Residual stresses can positively or negatively affect a product’s performance, which makes them a vital consideration for any critical design component. Often, structures are designed with considerable safety factors, in which case the effects of residual stress can be ignored, but as we push for higher performing structures that operate closer to the cutting-edge of technology, factors like residual stress can be the difference between successful performance and structural failure.
Positive values of residual stress are referred to as tensile, meaning the material is being pulled or stretched. Unintended tensile residual stresses can cause undesirable results, including cracking and failure. If tensile stresses induced by manufacturing processes are not taken into account, these can lead to premature failure.
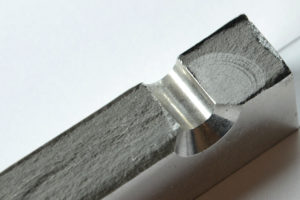
Negative values of residual stress are referred to as compressive, meaning the material is being pushed together. These kinds of residual stresses can improve the performance of fatigue-critical components. Surface treatment processes like shot peening and laser shock peening intentionally introduce compressive stress in select locations at the material surface to make products perform better. For instance, introducing compressive residual stress can toughen brittle materials such as glass in smartphone screens or pre-stressed concrete used in city infrastructure.
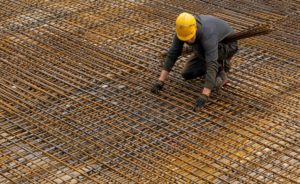
Overall, the residual stress on any given plane in a material must be in equilibrium, but there can be local regions with tensile or compressive stress. Below is our Residual Stress 101 vlog, which highlights the information above.
Residual stress engineering involves the practice of manipulating residual stresses in order to maximize the usability and lifespan of manufactured components.
Through residual stress measurement techniques, Hill Engineering is capable of quantifying the internal stresses in a material, to better inform design decisions. We are the industry leader in Contour Method measurements and provide the same level of precision and accountability in a broad range of other residual stress measurement methods.
The methods we employ are as follows:
- Contour Method
- Slitting Method
- Hole Drilling
- Ring Core
- X-ray Diffraction
- Neutron Diffraction
- Deep Hole Drilling
- Barkhausen Noise Analysis
- Biaxial Mapping
- TrueSlot
Hill Engineering is a trusted source for a wide range of measurement capabilities. For more information about residual stresses or any of the residual stress measurement techniques we employ at Hill Engineering, feel free to contact us.
BAMpF achieves USAF software certification
We are happy to announce that our BAMpF® software version 8.x has achieved software certification from the United States Airforce (USAF) to operate on the USAF network.
Continue reading BAMpF achieves USAF software certificationAdvances in Residual Stress Technology in honor of Drew Nelson
A special Issue of Experimental Mechanics on Advances in Residual Stress Technology in Honor of Drew Nelson was recently published. The Special Issue recognizes Dr. Nelson, Mike’s PhD advisor at Stanford University and a leader in the residual stress community, on becoming emeritus after 40 years of research contributions and teaching on the experimental determination of residual stresses and their effects on fatigue.
Continue reading Advances in Residual Stress Technology in honor of Drew Nelson