BAMpF® (Broad Application for Multipoint Fatigue) enables fatigue crack growth analysis of parts with non-standard geometry, loading, and residual stress conditions through the implementation of multipoint fracture mechanics (MPFM). This user-friendly software environment provides structural analysts and engineers a tool to accurately and efficiently complete challenging fatigue crack growth problems.
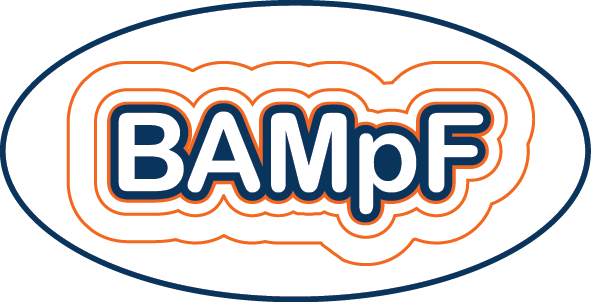
Starting from an assumed initial flaw, BAMpF® implements a multi-point fracture mechanics approach that allows crack shapes to evolve naturally as a function of the underlying, spatially varying stress fields and stress intensity factors. As illustrated in the figure below, the user specifies the number of points along the crack front to be used in the analysis. For each individual point, BAMpF® queries the stress intensity factor specific to the part geometry and loading through an interface with StressCheck® (a leading finite element software tool), provides the necessary inputs to AFGROW (a leading fatigue life assessment tool), and stores the expected fatigue crack growth for a given number of cycles. BAMpF® then combines the growth of each individual point into a new crack shape that serves as the starting point for the next increment of the analysis. This process is repeated until the fatigue crack reaches a critical size.
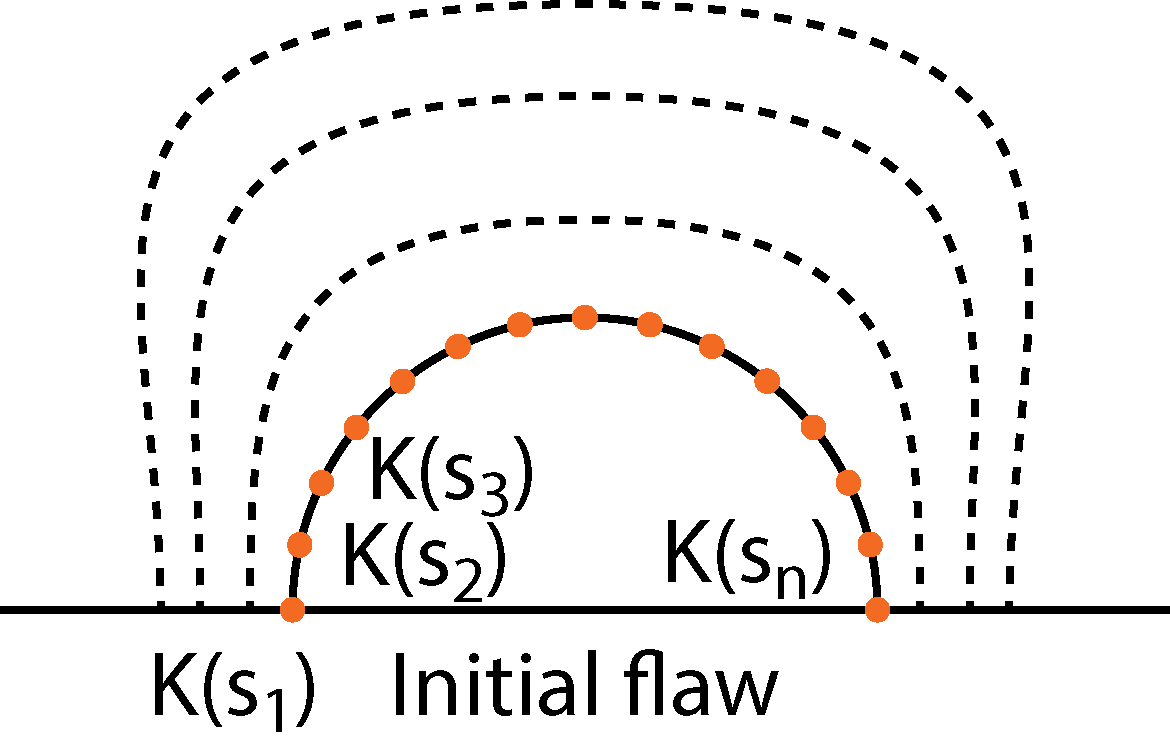
Illustration of multipoint fracture mechanics approach to defining individual control points around the crack front
Multipoint fracture mechanics improves the accuracy of fatigue crack growth calculations relative to traditional analysis methods by eliminating assumptions and constraints related to the shape of the crack (e.g. elliptical crack shapes are not required by MPFM). The use of MPFM is especially important when non-standard conditions like complex loading, complex geometry, and/or residual stresses are present as these factors tend to drive the evolution of the fatigue crack shape away from the circular/elliptical constraints imposed by the traditional analysis methods.
BAMpF® provides a straightforward approach for including residual stress in crack growth assessments. Residual stress input data for BAMpF® may come from measurement or process modeling (e.g., ERS-Toolbox®). The MPFM capabilities in BAMpF® enable accurate fatigue analysis of parts with laser shock peening (LSP), cold-expanded (CX) holes, of other bulk residual stress fields. For example, the figure below shows a comparison between the predicted (BAMpF®) and experimentally observed fatigue crack shape for a cold expanded hole test specimen.
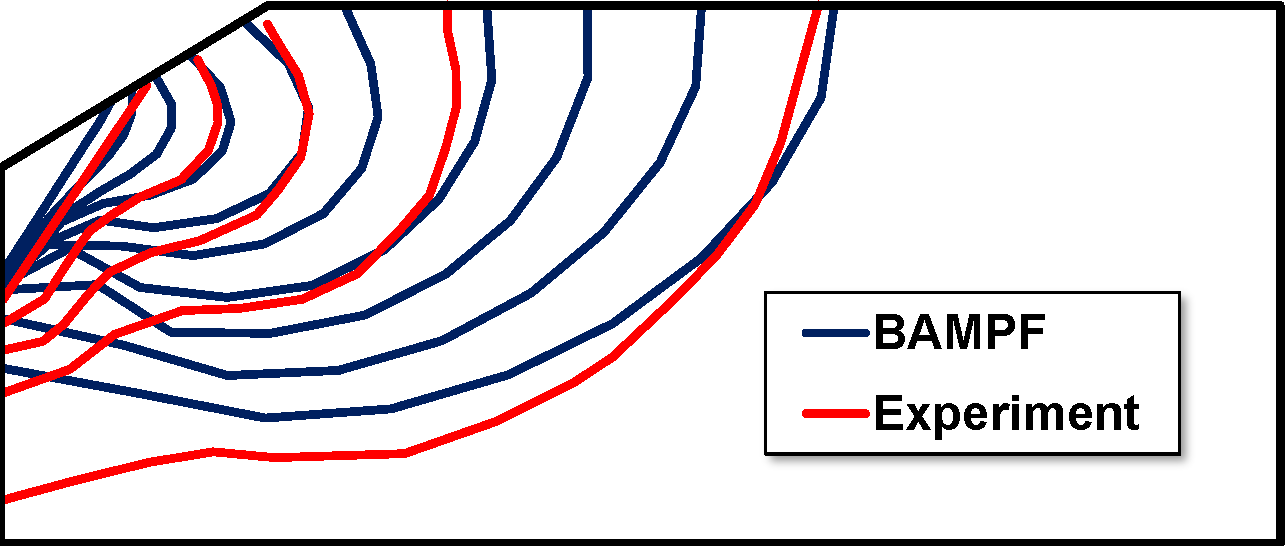
Fatigue crack growth analysis (BAMpF®) and experimental results for a cold expanded hole test specimen
Some of the key features and capabilities of BAMpF® include:
• Natural fatigue crack shape progression
• Fully 3D analysis
• Complex loading
• Multi-crack interactions and link-up
• Residual stress
BAMpF® has received software certification from the United States Airforce.
For more information about the study described above, our fatigue analysis and testing abilities, our residual stress engineering services, or to place an order for BAMpF® related goods and services, please contact us.
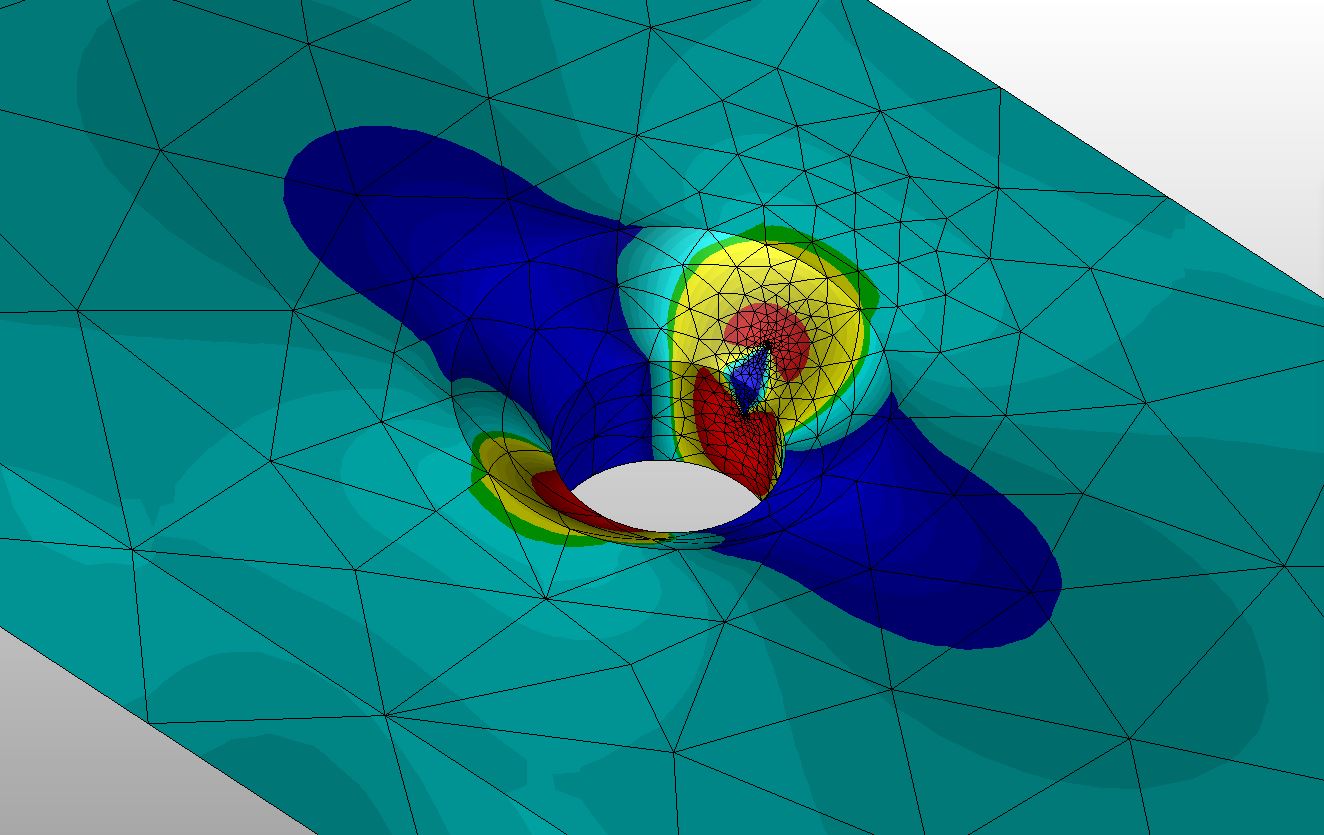
Image from a BAMpF® analysis showing the stress in a specimen with a small crack near a hole
Special thanks to our partners:
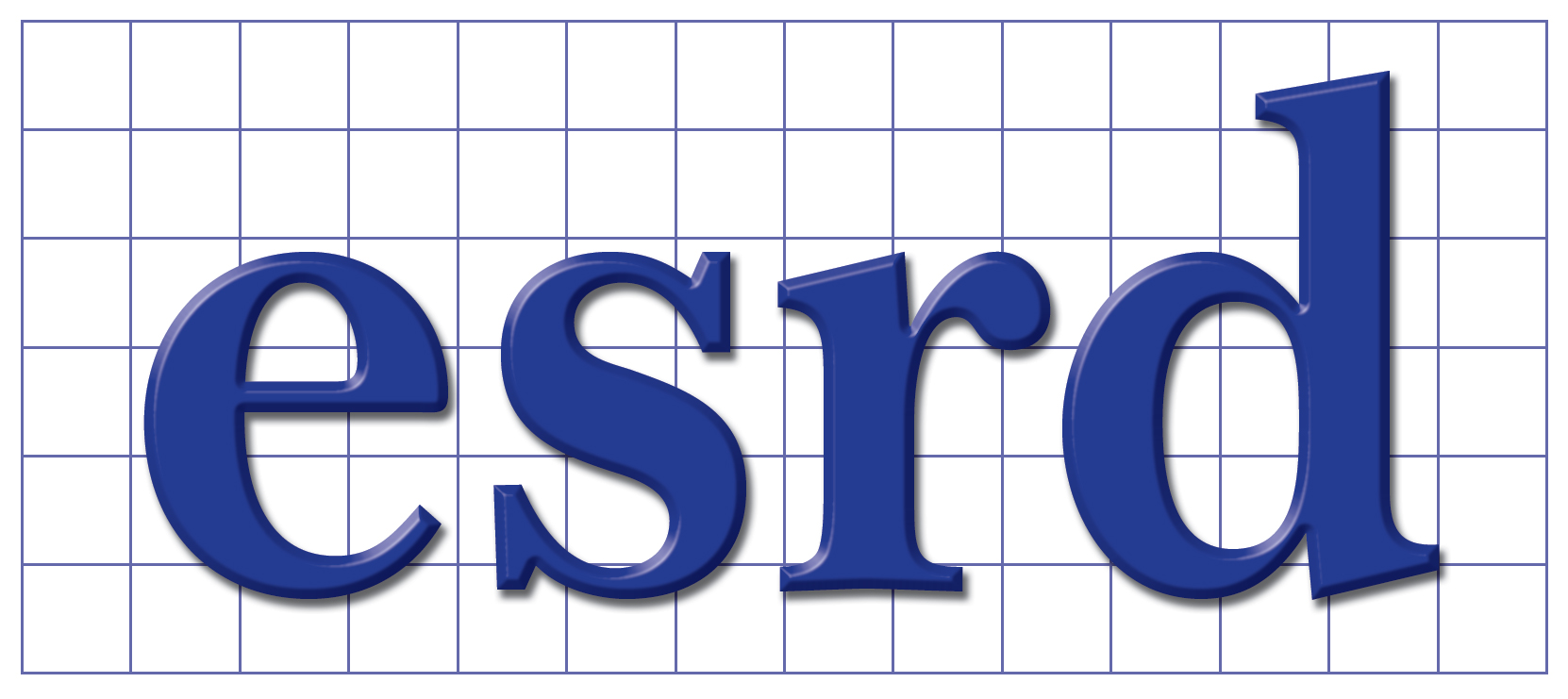
ESRD’s flagship software product, StressCheck® Professional, is an advanced FEA tool having numerous unique technical capabilities
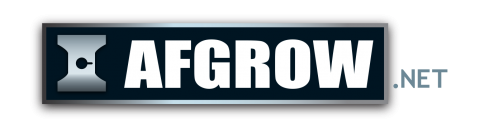
AFGROW is a Damage Tolerance Analysis (DTA) framework that allows users to analyze crack initiation, fatigue crack growth, and fracture to predict the life of metallic structures