A special Issue of Experimental Mechanics on Advances in Residual Stress Technology in Honor of Drew Nelson was recently published. The Special Issue recognizes Dr. Nelson, Mike’s PhD advisor at Stanford University and a leader in the residual stress community, on becoming emeritus after 40 years of research contributions and teaching on the experimental determination of residual stresses and their effects on fatigue.
Dr. Nelson received a PhD in Mechanical Engineering at Stanford University, worked six years in industry, mainly for General Electric, then returned to the university, where he is a Professor of ME. His research with students on residual stresses has included extension of the hole drilling method by use of optical methods, development of an eigenstrain method, use of fiber optic strain sensors embedded in composites, as well as modelling effects of residual stresses on crack growth using a crack closure approach, development of a surface acoustic wave method for monitoring the crack closure of microcracks, and studies of residual stress effects from shot peening and carburizing on fatigue. He received the Hetényi award from SEM in 1996.
Topics covered in the special issue include:
- New approaches for (a) computational modelling of the hole drilling method, (b) incorporating residual stress data from complementary measurement techniques such X-ray diffraction (XRD) into the method and (c) correcting for plasticity effects when stresses uniform with hole depth approach yield stress levels
- Application of the hole drilling method to fiber-metal laminates
- A new computational framework for evaluating residual stresses and uncertainties in use of the contour method plus a comprehensive reproducibility study of the method
- Application of the contour method to smaller size parts using scanning white-light interferometry
- Mapping heterogeneous residual stresses from XRD averaged measurements plus residual strain mapping with high energy dispersive XRD in thick specimens
- Use of a slitting method to measure residual stresses in a radioactive component plus a measurement repeatability study using a slotting method and XRD applied to shot peened specimens
- Studies of (a) residual stresses and warpage in a thin-walled aluminum structure processed by uphill quenching, (b) residual stresses/strains and fatigue behavior of a laser clad repaired titanium alloy and (c) the effect of bulk residual stresses on residual stresses and distortion induced by milling of thin-walled aluminum specimens
- A computational approach for predicting machining-induced residual stresses using calibration from digital image correlation (DIC) analysis of in-situ sub-surface displacement fields
- Use of neutron diffraction to investigate the internal stress distribution from confinement forces in a bridge cable strand model and accompanying analysis
- Measurement of residual stresses in bi-layer thin films by a ring‑core method using focused ion beam milling and digital image correlation
- A system-level thermo-mechanical finite element study of nuclear reactor cooling components to investigate residual strains and their effects on cyclic hardening and associated environmentally assisted fatigue
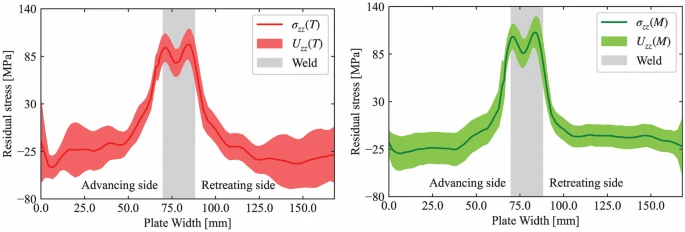
If you have any questions about the special issue or any of the services we offer, feel free to contact us.