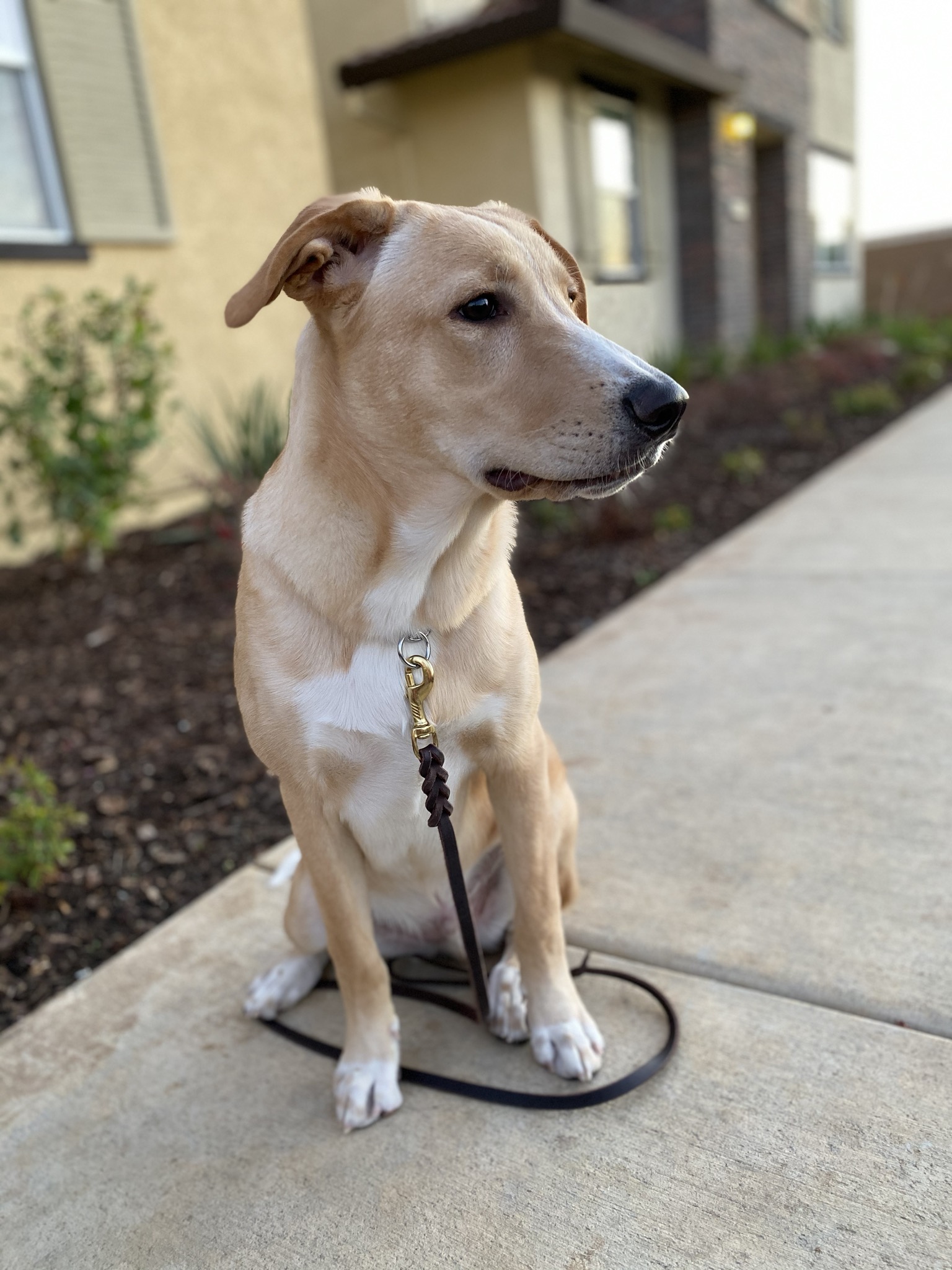
Rho, the dog
Who’s ready to meet our next pet? Last time, we introduced you to Delta, the spunky dog from Taiwan. Now let’s meet his “big” little brother – Rho. Continue reading HE Pet Spotlight: Rho
Rho, the dog
Who’s ready to meet our next pet? Last time, we introduced you to Delta, the spunky dog from Taiwan. Now let’s meet his “big” little brother – Rho. Continue reading HE Pet Spotlight: Rho
Summertime is just around the corner and we at Hill Engineering are always looking to engage our followers with fun and interesting information about engineering and residual stress. This summer we’re going to host the virtual Hill Engineering STEM challenge – a series of fun activities to demonstrate your engineering intuition and creativity. Participate on your own or with your family to compete for some cool Hill Engineering prizes! Continue reading #HillEngSTEM Summer Challenge
Staying safe and healthy during these times is something that’s on many people’s minds lately. Social distancing, washing our hands, and limiting outings are all things we can do to help “flatten the curve”. Wearing a face mask or covering when out in public is also something that can help protect others since some people with COVID-19 can show no symptoms. Face masks can be beneficial in areas with many people, since they can reduce the number of droplets we release when we speak, cough, or sneeze. Continue reading Face mask making with Hill Engineering
On your mark, get set, GO!
Hill Engineering isn’t just at the forefront of the residual stress measurement world, our employees are picking up the pace as well! The race pace that is. Today, we’re highlighting a few of our team members who cut through speed and strength like a wire EDM. Continue reading Racers of Hill Engineering
Our latest case study discusses our Broad Application for Modeling Failure (BAMF) software.
Broad Application for Modeling Failure (BAMF) enables fatigue crack growth analysis of parts with non-standard geometry, loading, and residual stress conditions through the implementation of multi-point fracture mechanics (MPFM). This user-friendly software environment provides structural analysts and engineers a tool to accurately and efficiently complete challenging fatigue crack growth problems.
Continue reading Case Study highlight: Broad Application for Modeling FailureHill Engineering and Engineering Software Research and Development, Inc. (ESRD) have executed a joint marketing agreement to collaboratively promote the combined use of our software tools: Broad Application for Modeling Failure (BAMF) and StressCheck® for fatigue analysis. Continue reading Announcing agreement with ESRD for joint BAMF/StressCheck marketing
Hill Engineering will be presenting at the upcoming Propulsion Safety & Sustainment Conference (PS&S) in Denver, CO on April 20th through April 23rd. We invite you to come see us. The mission of this conference is to proactively address or prevent problems with safety, readiness, reliability and sustainment within the tri-service turbine engine fleet, through the transition of existing and emerging technologies. Hill Engineering’s presentation will include a summary of recent work related to predicting residual stress and airfoil distortion from shot peening and laser shock peening. The abstract text is presented below. Continue reading Propulsion Safety & Sustainment Conference 2020
A representative composite overwrapped pressure vessel. Image courtesy of CompositesWorld: https://www.compositesworld.com/articles/thermoplastic-composite-pressure-vessels-for-fcvs
We’re putting something in a bottle, and no, it’s not an SOS to the world. It’s a strain gage!
Hill Engineering has recently developed technology to orient and apply strain gages inside a pressure vessel with restricted interior access. Continue reading Strain gage in a bottle
Delta, the dog.
In addition to residual stress, family pets are a special subject here at the office. This year at Hill Engineering, we’re starting a new blog series that highlights our four-legged friends. Don’t think that we forgot about animals with less than four legs, they’re coming up next! To kick things off, let’s meet Delta. Continue reading HE Pet Spotlight: Delta
Today, we’ve released the newest episode of our vlog: Residual Stress 101. The video is a return to basics, discussing the core of what it is we do here at Hill Engineering.
If you haven’t checked out our YouTube channel, it might be time. Our mission is to post content that helps highlight the capabilities of our organization, so that everyone can see how and why residual stress is important to their manufacturing processes.
Today’s post is a broad overview of what residual stress is, including the several techniques for measuring residual stress found in our lab. Look for future content that delves further into each technique, and contact us if you have any further questions or want to see a video related to something we haven’t discussed.