Hill Engineering recently participated in the virtual 2020 United States Air Force Structural Integrity Program Conference (ASIP). The ASIP Conference is specifically designed to bring together the world leaders in the area of aircraft structural integrity and to disseminate information on state-of-the-art technologies for aircraft structures in both the military and civilian fleets. Hill Engineering’s presentation included a summary of recent work related to developing a digital quality assurance record for typical aircraft maintenance processes like hold hole expansion. The abstract text is presented below along with a copy of the presentation slides.
Continue reading ASIP conference 2020Category: Uncategorized
Search results for uncategorized Hill Engineering blog posts
HE Pet Spotlight: Rho
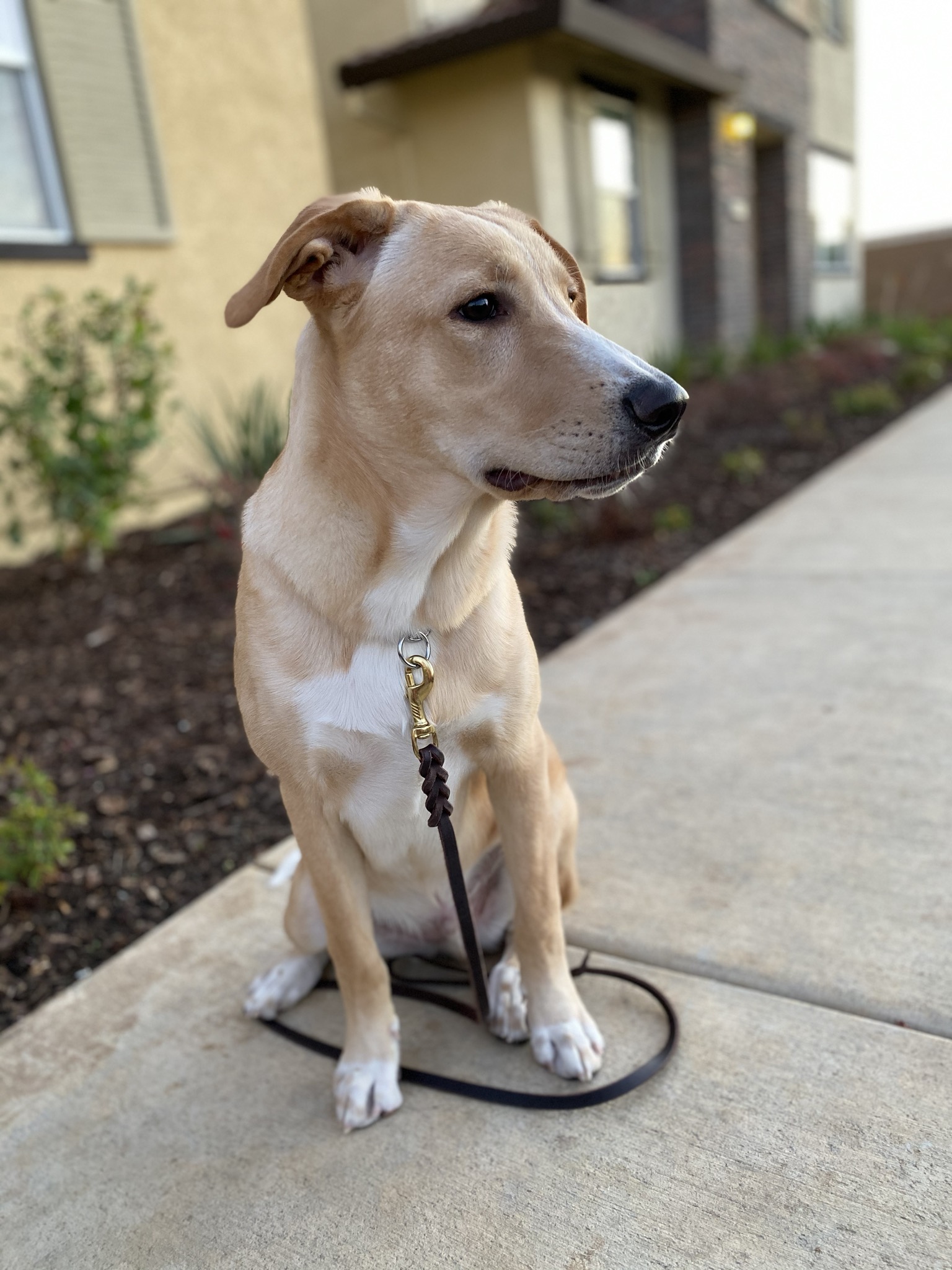
Rho, the dog
Who’s ready to meet our next pet? Last time, we introduced you to Delta, the spunky dog from Taiwan. Now let’s meet his “big” little brother – Rho. Continue reading HE Pet Spotlight: Rho
Racers of Hill Engineering
On your mark, get set, GO!
Hill Engineering isn’t just at the forefront of the residual stress measurement world, our employees are picking up the pace as well! The race pace that is. Today, we’re highlighting a few of our team members who cut through speed and strength like a wire EDM. Continue reading Racers of Hill Engineering
Vlog: How to Use the Nikon ModelMaker H120 3D Scanner
Hello Readers!
If you aren’t subscribed to our YouTube channel, we’d like to announce that our latest vlog is now live. Continue reading Vlog: How to Use the Nikon ModelMaker H120 3D Scanner
2016 Highlights at Hill Engineering
2016 was an exciting year at Hill Engineering. We accomplished so much and we wanted to take a moment to recognize some of the highlights. Continue reading 2016 Highlights at Hill Engineering
A Feast of Fall Festivities
The Hill Engineering employees took a quick break from all the residual stress analysis to partake in a few fall-themed festivities this season. We recognize that enjoying quality time together is an important way to strengthen our resolve as a team. What better way to do that than through everybody’s favorite activities: pumpkin carving and food! Continue reading A Feast of Fall Festivities
ASIP Conference
Hill Engineering is presenting about fatigue analysis methods for cold expanded aircraft fastener holes at the upcoming 2016 Aircraft Structural Integrity Program (ASIP) Conference in San Antonio, TX. Cold hole expansion is a method commonly used to induce compressive residual stress around the perimeter of fastener holes, which are common in aircraft structure. The compressive residual stress has significant benefits related to fracture and fatigue of the structure. Hill Engineering’s presentation will include a summary of current analysis methods and a plan for how these methods can evolve to allow for improvements in aircraft design and sustainment. The abstract text is presented below. Continue reading ASIP Conference
AFGROW User Workshop
Hill Engineering is presenting about fatigue analysis as part of the AFGROW User Workshop 2016 in Layton, UT. The objective of the workshop is to provide a forum for AFGROW users to exchange information and ideas related to fracture and fatigue. Hill Engineering’s presentation will include a summary of recent work on the formulation and solving of benchmarking problems in the field of fatigue crack growth analysis. The abstract text is presented below. Continue reading AFGROW User Workshop