We are thrilled to announce that Hill Engineering’s Integrated Maintenance System (IMx+) has been nominated for the prestigious “Outstanding Scientist Team” Award at the Air Force Life Cycle Management Center (AFLCMC) Annual Engineering Awards. This nomination is a testament to the dedication, innovation, and technical excellence demonstrated by the IMx+ development team in addressing the quality assurance needs of the aerospace industry.
Category: Our Work
Search results for Hill Engineering blog posts under the subject category our work
The Ring Core Method: New Brochure
Hill Engineering’s latest brochure shines a spotlight on the ring core residual stress measurement method, a powerful technique for assessing near-surface to bulk residual stress in materials. With its compact footprint and versatility, the ring core method is a robust technique that can be applied under a variety of circumstances. Continue reading The Ring Core Method: New Brochure
Introducing Hill Engineering’s New Brochure on Deep-Hole Drilling Residual Stress Measurement
Our latest brochure highlights the Deep-Hole Drilling (DHD) residual stress measurement method, a specialized technique with applications across multiple industries, including aerospace, automotive, and heavy manufacturing.
Download Hill Engineering’s X-Ray Diffraction Residual Stress Measurement Brochure
We are excited to introduce our new downloadable brochure, providing comprehensive details on the x-ray diffraction (XRD) residual stress measurement method. Available on the X-ray Diffraction Method page, this essential technique is ideal for accurately determining near-surface residual stresses, offering precise results that are crucial for industries ranging from aerospace to manufacturing.
Continue reading Download Hill Engineering’s X-Ray Diffraction Residual Stress Measurement Brochure
IMx+ system deployment for A-10 Hogback
In a recent production deployment, the Integrated Maintenance System (IMx+) system was utilized during the A-10 Fuselage Modification, affectionately nicknamed Hogback. During this structural modification, over 500 holes are inspected along the upper longeron, a critical component of the aircraft. Continue reading IMx+ system deployment for A-10 Hogback
A closer look at Hill Engineering’s internal audit program
In an early blog post, we discussed Hill Engineering’s efforts to build and maintain a Quality System that is compliant with ISO 17025. More recently, we touched on our quality control program, which we use as an important check to make sure that our measurements are being carried out according to established procedures and meeting certain quality requirements. Now we’re back to give another glimpse into our Quality System and talk about another important aspect, our internal audit program.
Continue reading A closer look at Hill Engineering’s internal audit program
Hill Engineering acquires a new XRD system
Hill Engineering has recently acquired a new diffractometer and enclosure that will enable us to perform x-ray diffraction (XRD) residual stress measurements in our Rancho Cordova, California, laboratory.
Continue reading Hill Engineering acquires a new XRD system
New case study: Residual Stress Field Team
We invite you to read our latest case study which highlights the capabilities of our Residual Stress Field Team, who can perform many of our world-class residual stress measurements on-site at a customer’s facility. Continue reading New case study: Residual Stress Field Team
Residual Stress Field Team
Hill Engineering is committed to providing high-quality residual stress measurement data to its customers, both in our laboratory and on-site. Our Residual Stress Field Team is equipped with the same knowledge and expertise as our laboratory team to meet the challenge of performing residual stress measurements in the field.
Our Residual Stress Field Team has the experience necessary to tailor each measurement approach to meet the unique needs of the customer and bring our world-class residual stress measurement capabilities to the place it matters most – the operational environment. Challenging measurement access, complex geometry, and applications requiring rapid turn time are just a few situations where our team and equipment excel, allowing us to assess both near-surface and bulk residual stress in components that are delicate, large, or otherwise unable to be sent to our laboratory for in-house testing.
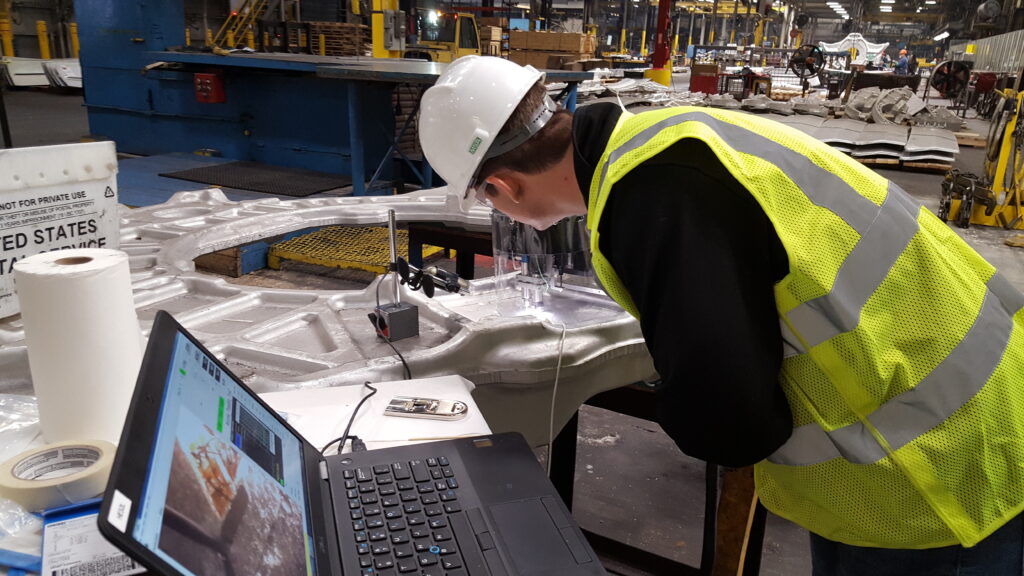
From a quality control perspective, measurements performed in the field allow customers to get a detailed glimpse of their manufacturing process, as measurements can be carried out shortly before or after a critical step, such as heat treatment, all without having the component leaving the manufacturing line, saving time for the customer.
On-site measurements and services that are available through our field team include:
The Hill Engineering Residual Stress Field Team, with its ability to perform on-site residual stress measurements, is just one of the ways we offer flexible, precise, and high-quality residual stress testing to our customers. Their mobility, coupled with advanced technology, ensures that the science of engineering is not confined to laboratories but can thrive in real-world environments where innovation truly takes flight.
If you have any questions about the capabilities of our Residual Stress Field Team and how it can help your project, please contact us.
ERS-Toolbox® brochure
Hill Engineering’s ERS-Toolbox® software predicts the residual stress and distortion caused by surface treatment processes such as shot peening, laser shock peening (LSP), and cold hole expansion. This elegant computational design tool helps engineers and analysts design, analyze, and optimize the use of these processes, maximizing the performance of critical structural details.
Continue reading ERS-Toolbox® brochure