We talk a lot about the residual stress measurement techniques we employ at Hill Engineering. One of the most commonly used is the Contour Method! Invented in the year 2000, and patented by Los Alamos National Laboratory, the contour method measures 2D residual stresses over a planar surface.
The Process
This residual stress measurement technique consists of cutting a metal part into two pieces along a given plane. This plane might be near a weld or an axis of rotation, depending on the data of interest.
Splitting the part releases internal stresses across the sectioning plane, causing the newly created surfaces to deform. The magnitude of the stresses released determines how much deformation occurs. Parts with larger residual stress will deform more than those with less.
We’re then able to measure these deformations using a scanning profilometer, which creates a highly precise digital 3D map of the deformed surface. Using this scanned map in conjunction with finite element analysis allows us to determine the initial residual stress field.
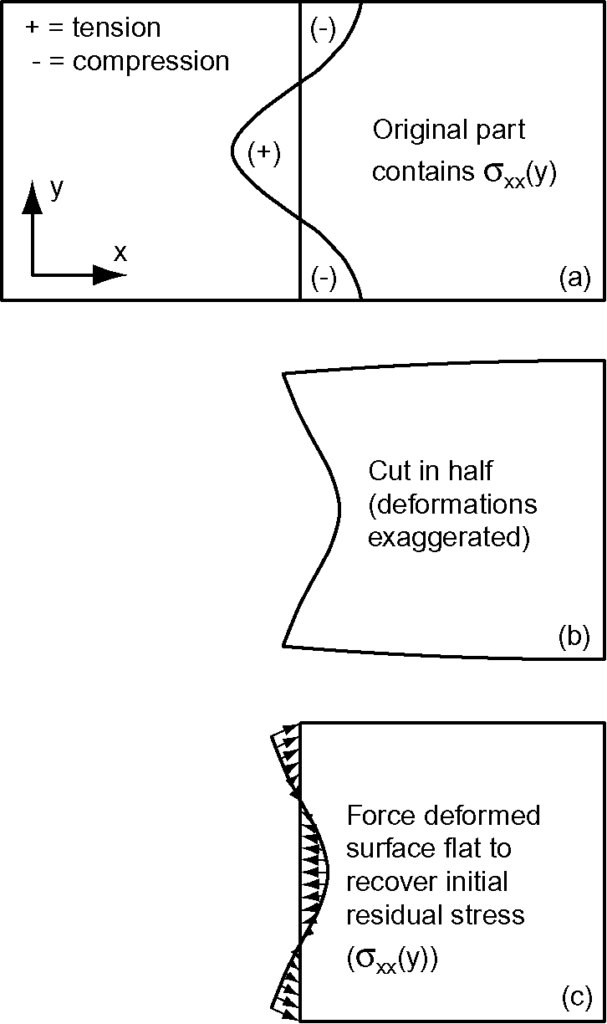
The Uses
Why choose the contour method?
This robust measurement technique has several benefits. It provides a stress map across an entire surface, rather than at a single location as with many other techniques. The contour method is also ideal for parts with large or complex geometry, and can handle materials with complex or variable texture, as well as those with large grains.
We’ve previously published studies about the repeatability of the contour method, which evaluated parts of varying materials, manufacturing processes, and surface treatments. Through the study, we found that the contour method produces highly repeatable results, with relatively narrow repeatability standard deviation, especially through the part interiors.
Hill Engineering personnel have been active in the development of the Contour Method and now, under license, use the method to meet the needs of customers worldwide. If you have any further questions about the Contour Method, or want to discuss employing the Contour Method for your residual stress needs, please contact us.