We recently learned that some hole drilling method and contour method results were highlighted in the August 2022 issue of Railway Track and Structures. The article is titled Residual stress investigation of ultrasonic impact treated and untreated thermite welds.
In late 2020 and early 2021, Hill Engineering worked with MxV Rail (formerly TTCI) to measure the residual stress in thermite welds as part of an investigation on the effect of ultrasonic impact treatment (UIT) and how it assists in extending the life of these types of welds.
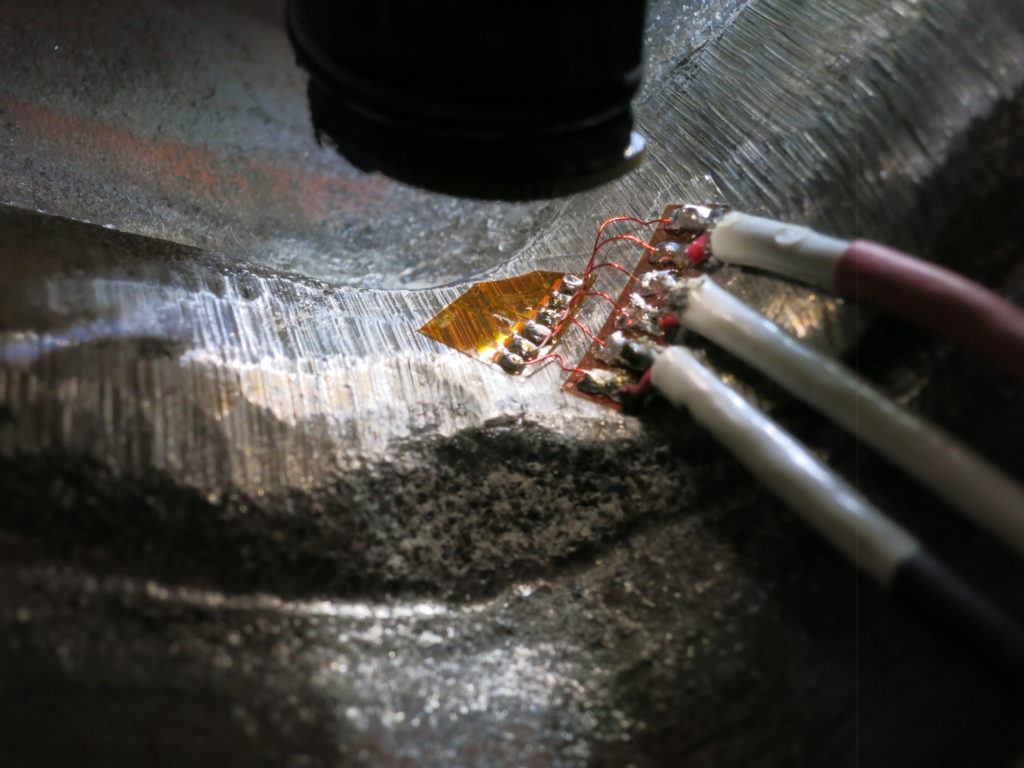
Thermite welding is a process that uses molten metal to permanently join conductors. Due to the geometry of the rail, impurities and pores that would normally be expelled through the slag material can get trapped in the web/base or head/web fillet locations, potentially creating nucleation sites for harmful fatigue cracks that can lead to weld failure. As a result, these welds generally have a shorter life span than the surrounding rail material.
Fatigue cracks grow more slowly when in the presence of compressive stress. To help mitigate the effects of the thermite welding process, ultrasonic impact treatment is performed along the web and fillet locations of the rail, plastically deforming the material, and introducing beneficial compressive stresses.
Hill Engineering measured three different thermite weld specimens using the hole drilling method and contour method. Two specimens were treated, and one specimen was untreated. The results from these measurements helped explain why treated thermite welds showed more longevity and better resistance to defect formation in the fillet locations when compared to untreated thermite welds.
If you are interested in reading more about our work related to this study by MxV, the publication can be found here.
For more information about our residual stress measurement capabilities and how it can help support your project, please contact us.