Distortion of parts during the machining process is a significant problem faced by many machining vendors. This phenomenon typically results from the release and redistribution of residual stress in the material once the part is unclamped from the machine table. When not accounted for, machining distortion can lead to out-of-tolerance parts that either require reworking, or have to be scrapped.
Our latest Case study highlights Hill Engineering’s machining process simulation capabilities and how they can be utilized to reduce uncertainty in machining planning and improve processes through validated models. The study focuses on machining modeling of a representative aircraft specimen using multi-step finite element analysis.
Click the link above to read the full write-up, or visit our Case study page to read through any of our previous work highlights. If you have further questions, don’t hesitate to Contact us for more information.
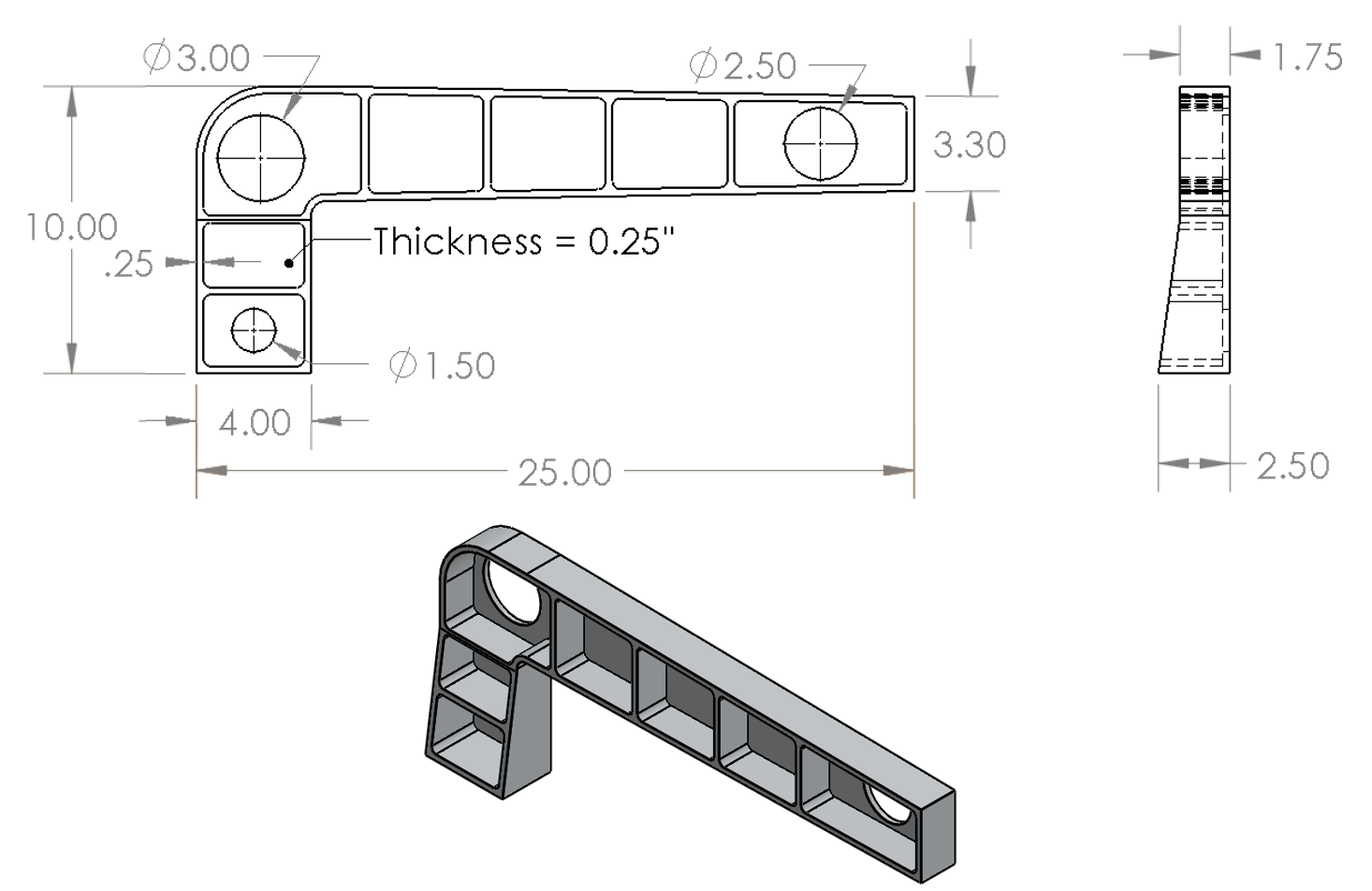
The representative aircraft specimen part geometry (dimension in inches)