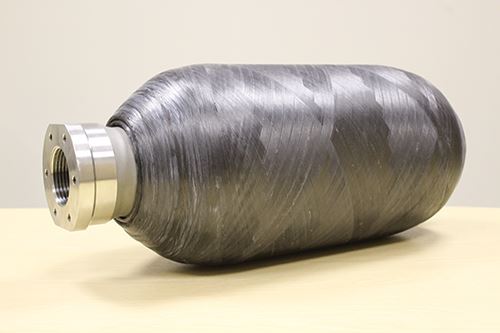
A representative composite overwrapped pressure vessel. Image courtesy of CompositesWorld: https://www.compositesworld.com/articles/thermoplastic-composite-pressure-vessels-for-fcvs
We’re putting something in a bottle, and no, it’s not an SOS to the world. It’s a strain gage!
Hill Engineering has recently developed technology to orient and apply strain gages inside a pressure vessel with restricted interior access.
We were first approached with the challenge by NASA, who sought to perform testing on composite overwrapped pressure vessels. COPVs, as they’re known for short, are vessels constructed of a thin metallic liner wrapped in a fiber composite, designed to hold fluids under high-pressure. These are often used to store fuel during spaceflight, due to their high strength and low weight.
During manufacturing and use, COPVs undergo intense environmental conditions, which makes studying their performance challenging. To further complicate things the metallic liner, which is the inner layer, is only accessible through a small diameter hole at one or both ends.
Presented with this issue, our development team had their work cut out for them: how to position a correctly oriented strain gage inside the COPV and apply the pressure needed to adhere it to the vessel wall, all while retaining access to the gage wires in order to collect readings during measurements.
NASA provided a full-scale test COPV, which we sectioned in order to track the effectiveness of our process. The goal was to apply a strain gage five feet from the access point through an approximately 1-inch diameter inlet port. After months of design and procedure iterations, our team developed the custom tooling necessary to achieve the desired results. The procedure allows us to correctly apply a gage in only a couple hours and the portability of our tooling allows us to perform the method in nearly any environment.

A simplified diagram of the tooling developed for the strain gaging procedure.
Since its initial installation, we’ve utilized this technique for numerous “strain gage in a bottle” applications, further diversifying our capabilities. The results have been near-perfect, much to the satisfaction of our customers!
If you have more questions about this particular technique, how it can help your project, or about any of our residual stress measurement techniques, feel free to contact us.
For additional information on this particular application and how it benefitted NASA’s program, read their article on COPV Test and Measurement Techniques.