We invite you to read our latest case study which highlights the capabilities of our Residual Stress Field Team, who can perform many of our world-class residual stress measurements on-site at a customer’s facility.
Residual stress measurements that are executed in the field can be useful to customers who have components that are too large, delicate, or otherwise unable to be sent to our laboratory for in-house testing. Additionally, on-site measurements can allow customers to evaluate critical steps in a manufacturing process, such as heat treatment, as soon as it is completed, making in-field testing ideal during quality control inspections.
Our Residual Stress Field Team is comprised of the same personnel responsible for carrying out our in-house testing, so customers can expect to receive the same level of high-quality residual stress measurement results that Hill Engineering is known for. We are equipped to provide both near-surface and bulk residual stress measurements, as well as strain gaging services, to your specifications.
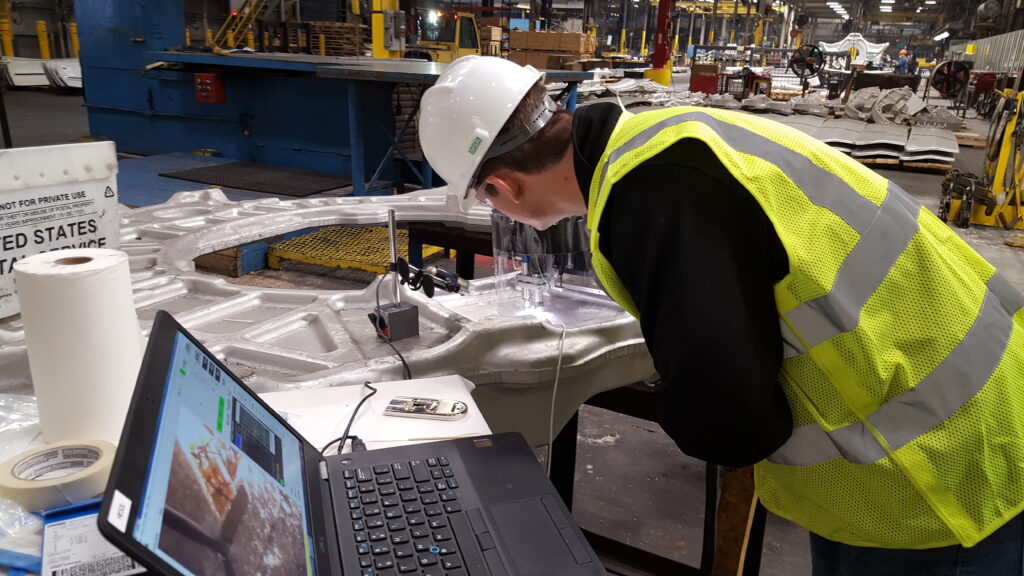
For more details about the residual stress measurement services our Residual Stress Field Team can provide, visit the case study.
If you have any questions about our on-site services or how residual stress measurements can help you meet the goals of your project, please contact us.