Hill Engineering would like to congratulate Renan Ribeiro for winning the Henry O. Fuchs Student Award. Established in 1991, this award recognizes a graduate or recently graduated student that is working in the field of fatigue research and applications. The purpose of this award is to promote the education of engineering students in the area of fatigue technology.
This award honors the memory of Professor Henry O. Fuchs. Professor Fuchs participated in the SAE Fatigue Design & Evaluation Committee’s research projects, was a member of the faculty who founded the SAE Fatigue Concepts in Design short course, published extensively in SAE and elsewhere in the technical community, and actively participated in the Surface Enhancement Division of the Committee which is responsible for many standards relating to surface treatments of metals for withstanding fatigue damage.
Renan’s Ph.D. dissertation titled “Residual Stress and Fatigue Crack Growth Modeling in Complex Geometry Using Eigenstrain” was completed in 2019 at the University of California, Davis. The following is a brief excerpt from the abstract.
Residual stress from quenching is inherent in the production of key high-strength aluminum alloys (e.g., 7xxx series aluminum), as quenching is a step in the widely used precipitation hardening process. Some residual stress relief processes are available, but do not fully relieve the residual stress, especially in complex geometry (e.g., die forgings). It is well accepted that residual stress affects fatigue performance, and should be considered in structural design of critical components. Residual stress can be measured by a variety of experimental techniques, but it is desirable to have modeling tools to predict residual stress more rapidly and efficiently. While nonlinear process models have been used with some success for prediction of quench induced residual stress, they are very complex, time consuming, and typically require large amounts of experimental data specific to the problem being studied as input in the model. The eigenstrain method, on the other hand, uses linear elastic finite element (FE) models, and provides a useful alternative for modeling of quench-induced residual stress. Currently, no studies have been published in the literature using eigenstrain modeling in the context of quenching. As an extension to previous studies, this work seeks to evaluate eigenstrain models for prediction of quench-induced residual stress in finished parts given the residual stress in raw stock material, and subsequently the effects of residual stress in their fatigue performance.
Renan is currently working at Hill Engineering. Please join us in congratulating Renan on this well-deserved award.
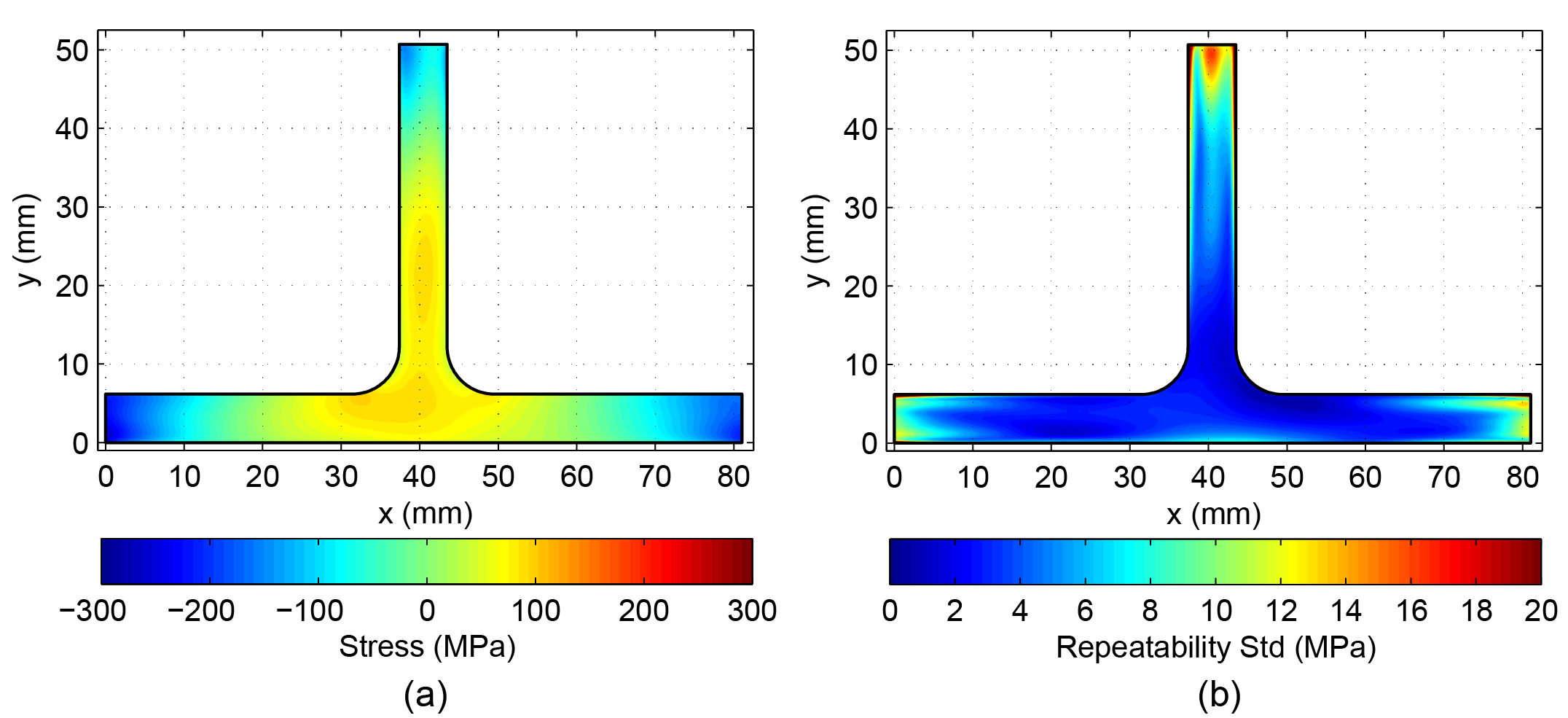
Illustration of measured residual stress in an aluminum T-section using the contour method