Hill Engineering was recently awarded US Patent 10,900,768 for residual stress measurement technology. Granted on January 26, 2021, the title of the patent is “Systems and Methods for Analysis of Material Properties of Components and Structures Using Machining Processes to Enable Stress Relief in the Material Under Test..” The patent abstract is available below. There is a link at the end to download and read it in full.
Analysis of residual stress in materials is often done in static conditions in a laboratory. Accurate systems and methods for performing these analyses in a dynamic, non-laboratory environment are notoriously difficult and can be very inaccurate. A method using a portable, field deployable apparatus having greater accuracy than currently available is disclosed whereby accurate and repeatable residual stress analysis may be implemented in non-laboratory environments leading to greatly improved diagnostics, maintenance and life limit prediction.
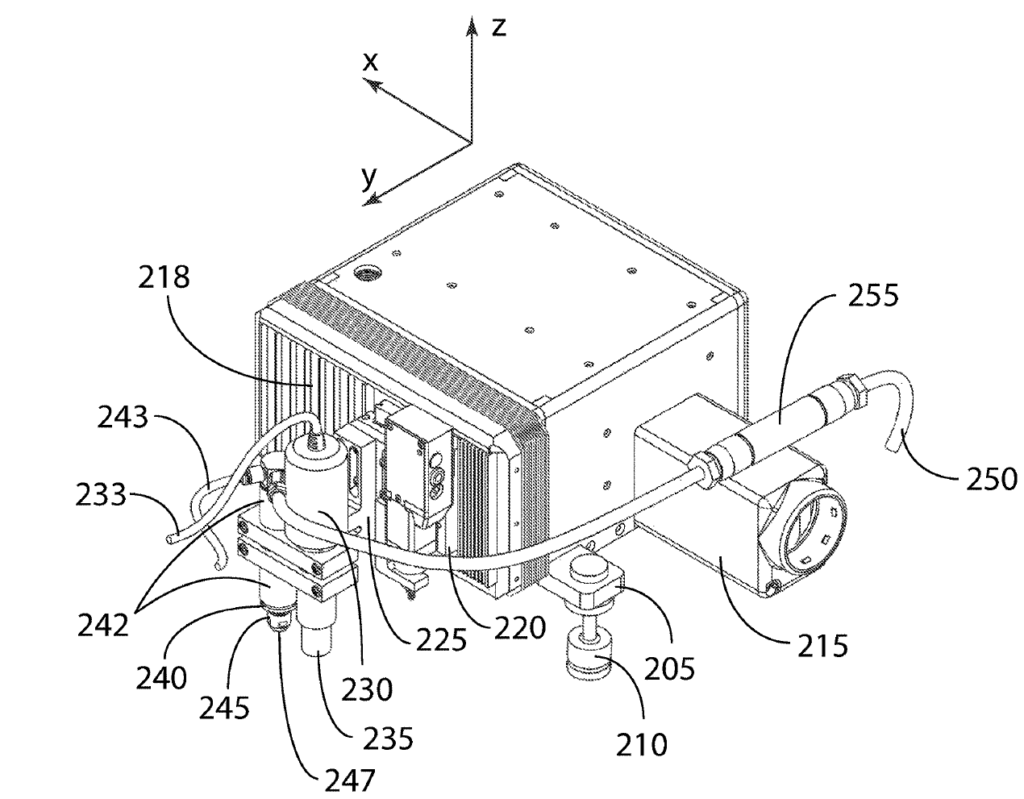
A consequence of manufacturing is that when metals are formed, through any method or technique, residual stresses are created in the material that may affect its performance and may be difficult to quantify. It is common to find methods, such as heat treatment, that are used to reduce the magnitude of residual stresses but in general there are almost always some residual stresses after a process or treatment is completed. In some manufacturing processes, residual stresses may be deliberately created. As an example, mechanical surface treatments used to improve fatigue performance, such as shot peening using steel shot or laser peening, build residual stresses into the surface of a material. Chemical treatments such as nitriding, or case-hardening, heating in a nitrogen rich atmosphere so as to build a surface into which nitrogen has been diffused, are common processes. Surface treatment affects only a very thin layer of the metal but this is relied on to reduce or prevent the formation of cracks which become points of origination of failure; typically a crack is an area of extreme stress, or stress riser, which may propagate over time leading eventually to the destructive failure of the component.
Because the practical characterization of material residual stress is difficult, a routine engineering solution is to develop a process which ensures that failure modes or lifetimes are achieved on a statistically significant basis. One consequence of this is that the processes are often stochastic in nature and determined experimentally. It should be evident that building in safety factors supported by low-quality data is costly and fraught with uncertainty; using what are only believed to be representative samples in a laboratory is one example of an uncertainty leading to questionable data. It is clear, then, that an urgent need exists for systems and methods that improve such processes so that accurate residual stress measurements may be made on component parts that have been or will be in use. There is also a need for greatly improved accuracy of machining equipment normally used in analysis work at an economical price point. There is an advantage to being able to do the analysis work in the field, thus avoiding the costs and delays when parts must be shipped to a remote facility. This is especially true where critical components for high value systems are being considered. For example, the consequences of failure of a turbine blade can be catastrophic but detection of failure onset is difficult with current processes.
Download the full patent for a more in-depth description. If you have any further questions about the technology, please feel free to contact us.