Hill Engineering will be presenting at the upcoming Propulsion Safety & Sustainment Conference (PS&S) in Denver, CO on April 20th through April 23rd. We invite you to come see us. The mission of this conference is to proactively address or prevent problems with safety, readiness, reliability and sustainment within the tri-service turbine engine fleet, through the transition of existing and emerging technologies. Hill Engineering’s presentation will include a summary of recent work related to predicting residual stress and airfoil distortion from shot peening and laser shock peening. The abstract text is presented below.
In modern military and commercial aircraft turbine engines, high cycle fatigue and foreign object damage are significant factors of sustainment costs. Foreign object damage (FOD) is most acute on the thin leading edges of titanium airfoils. Objects inadvertently ingested in the engine include small stones, aircraft fasteners, and birds. When these objects impact the rotating titanium airfoils, damage such as dents, nicks or tears result. Left undetected or uncorrected, this damage provides an ideal initiation site for high cycle fatigue cracks to form then propagate within the airfoil. Once these cracks reach a critical length, the airfoil will fracture resulting in significant secondary damage and a possible in-flight shutdown of the engine or catastrophic failure. Engineered residual stress processes like shot peening and laser shock peening (LSP) are often used to mitigate cracking risk in airfoils.
This presentation will discuss an analytical tool (ERS-Toolbox®) used for the design of engineered residual stress processes for integrally bladed disk airfoils. In addition, the presentation will incorporate comparisons between ERS-Toolbox® predictions and experimental testing performed to quantify the deformation, residual stress, and fatigue performance of airfoils treated with shot peening or laser shock processing.
If you are planning to attend the conference please stop by to discuss Hill Engineering’s capabilities in fatigue analysis and deisgn and residual stress measurement. Please contact us for more information.
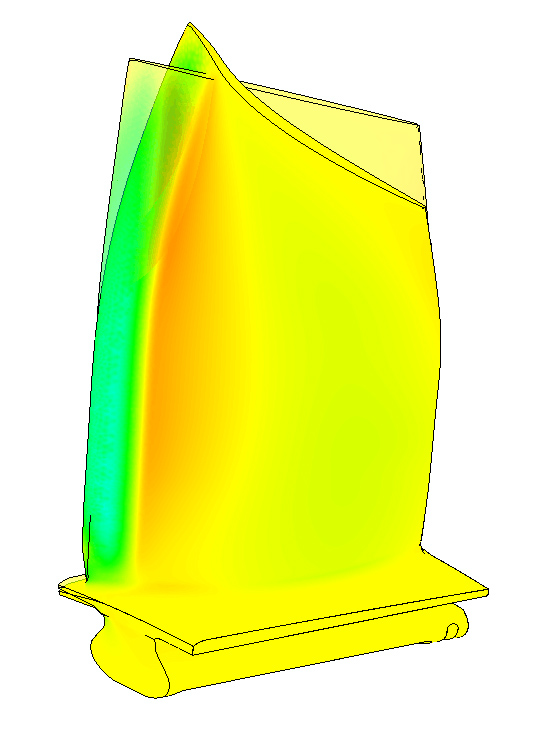
Illustration of predicted residual stress and deformation from application of laser shock processing to a compressor airfoil