We’ve recently uploaded a new case study on the topic of part distortion caused by machining. Distortion is a significant problem faced by many industries, especially where rigorous dimensional tolerances are required. When not appropriately accounted for, distortion can lead to significant economic loss and should be managed for effective design and production.
After establishing a representative problem in the case study, we used modeling to estimate part distortion due to both machining-induced residual stress and the bulk residual stress contained in the raw material. We also explore the effects of part placement within the raw material on the resulting part distortion.
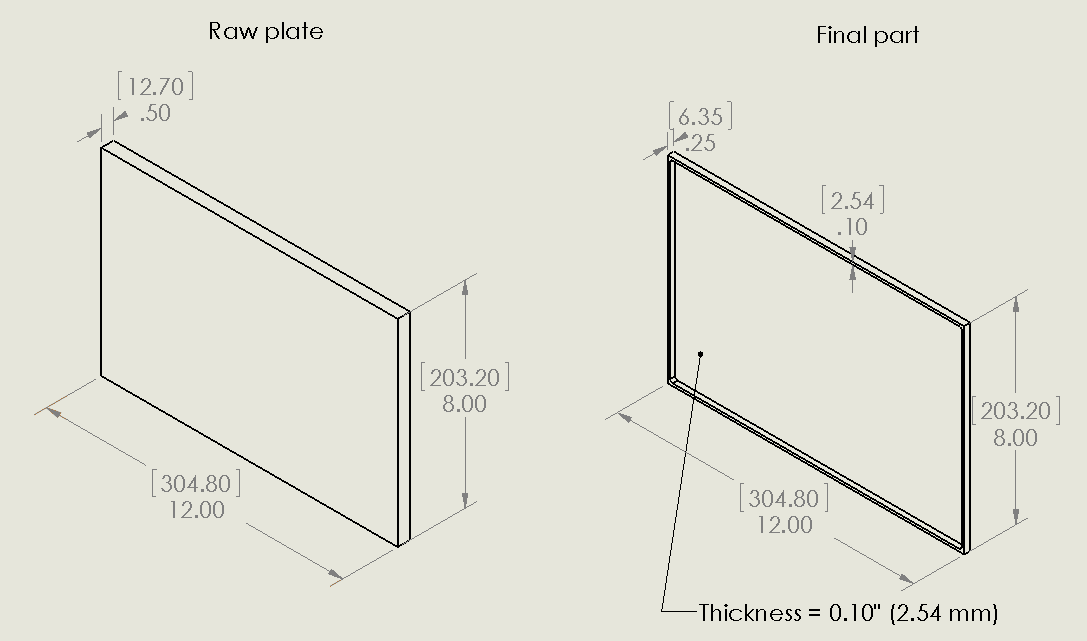
Raw plate and final part geometry for the case study representative problem. Non-bracketed dimensions are in inches and bracketed dimensions are in mm.
Read the full case study here to see our findings. If this study relates to your production or design, or if you have any questions about how these results might affect your projects, please do not hesitate to contact us. We would also be happy to answer any questions about the residual stress measurement techniques employed at Hill Engineering.