We recently uploaded a new case study on the topic of part distortion caused by residual stress during machining. We wanted to dive a little deeper into the topic with an analysis of a distorted aerospace part. Here is what we found.
The focus of this blog post is the distortion of a machined aluminum bulkhead published by engineers at The Boeing Company in 2001. The publication includes an image of a significantly distorted machined aluminum bulkhead as an example of what can go wrong if residual stress induced distortion is not effectively managed during manufacturing of asymmetrically shaped parts.
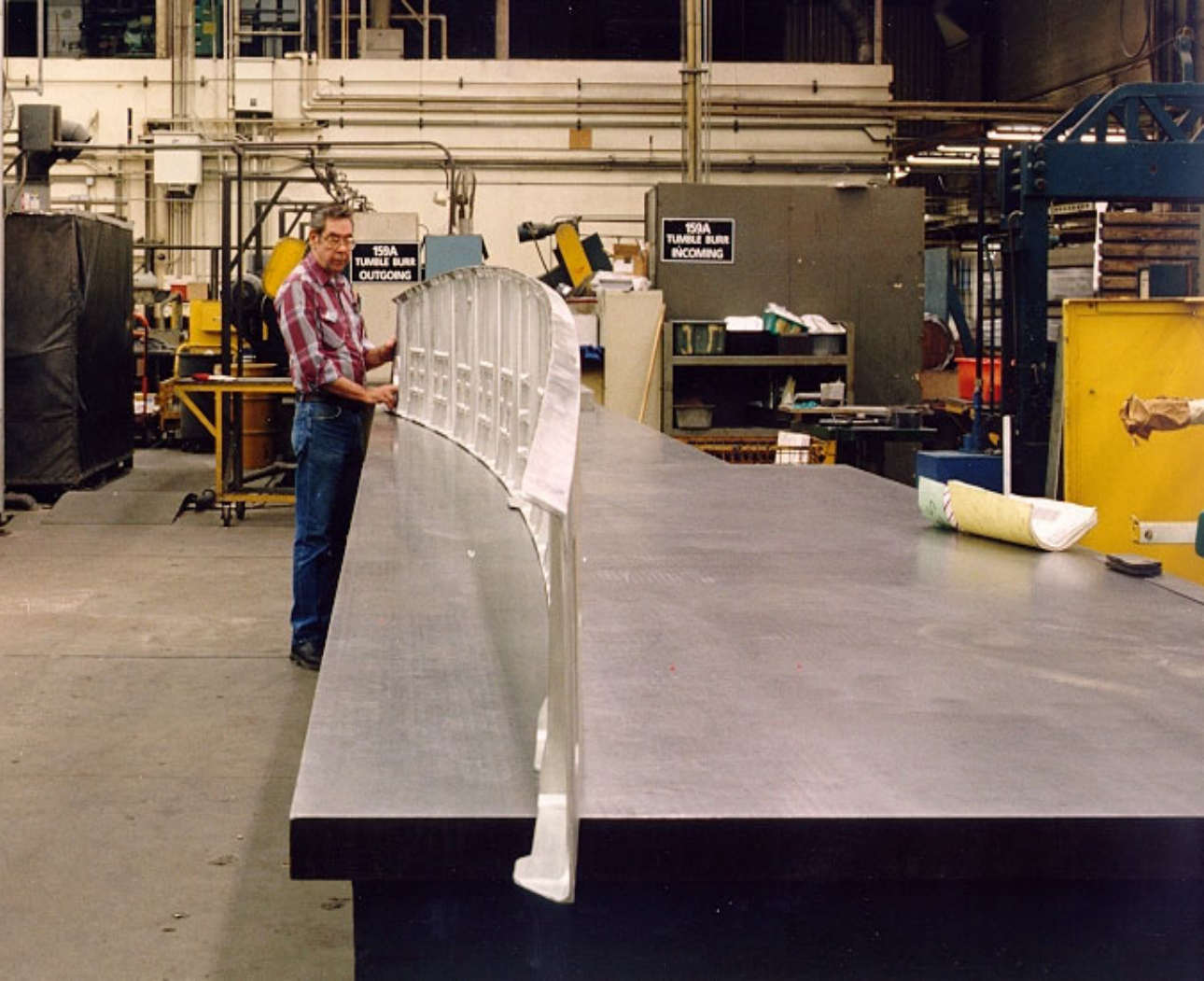
Photograph of distorted machined aluminum bulkhead
The focus of the paper is on the development of models to accurately predict the behavior of machined parts and it does not go into detail on this bulkhead. It does say that the material is “aluminum alloy 7050 die-forging” and that the observed bow in the bulkhead is “almost a foot.”
Interestingly, the paper does provide some context on the cost of the problem stating that the “planned costs” for manufacturing are on the order of $42,000; however due to distortion problems (resulting in a high scrap rate) the “actual costs” exceeded $100,000 per part.
Since the publication does not include information about the temper of the material (e.g., -T74 or -T7452), we wanted to see if we could reverse engineer the level of residual stress that would have been required to produce this level of distortion in a 30 foot long bulkhead.
For our analysis we assumed that the machined aluminum bulkhead was manufactured from 3.0 inch thick aluminum alloy 7050 stock material. We input different initial residual stress states into the machining model based on published results. For example, the figure below from Prime and Hill shows representative residual stress values for 7050-T74 plate and 7050-T7451 plate. These represent two extreme residual stress conditions. The stress relieved condition (-T7451) is a typical condition for aerospace manufacturing. The non-stress relieved condition (-T74) is atypical.
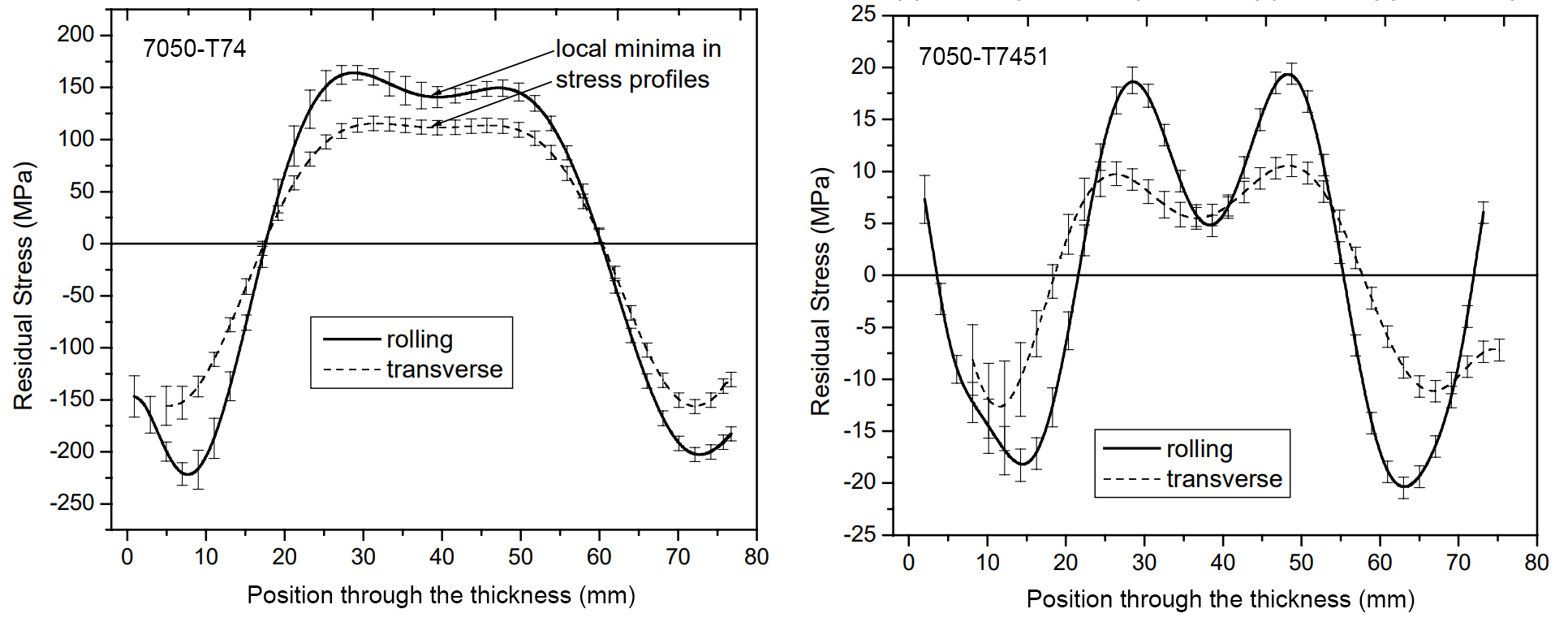
Representative residual stress distributions for (left) non-stress-relieved and (right) stress-relieved aluminum alloy 7050 plate
Our analysis predicted that there would be approximately 1.5 inch of distortion for a stress-relieved material condition (e.g., -T7451) and on the order of 18.0 inches of distortion for the non-stress-relieved condition (e.g., -T74). Based on the results of this analysis it seems like the distorted machined aluminum bulkhead used in the above example was likely machined from non-residual-stress-relieved stock material. The reported distortions are likely much larger than would occur if a similar part were machined from typical residual stress-relieved material.
If this example relates to your production challenges, or if you have any questions about how these results might affect your projects, please do not hesitate to Contact us. We would also be happy to answer any questions that you may have.