Aluminum alloy heat treatment is a three-step process designed to achieve the desired properties. The process involves: 1) solution heat treatment (SHT) at an elevated temperature below the melting point, 2) quenching in a tank of fluid (e.g., 140-180°F water), and 3) age hardening. While providing good properties, the heat treatment has the negative side effect of creating bulk residual stress and distortion.
Continue reading Case Study: Aluminum forging quench modelingCategory: Our Work
Search results for Hill Engineering blog posts under the subject category our work
Aluminum forging quench modeling
Aluminum alloy heat treatment is a three-step process designed to achieve desired properties. The process involves: 1) solution heat treatment (SHT) at an elevated temperature below the melting point, 2) quenching in a tank of fluid (e.g., 140-180°F water), and 3) age hardening. While providing good properties, the heat treatment has the negative side effect of creating bulk residual stress and distortion. These side-effects are a direct result of non-uniform cooling during the rapid, time-dependent quench. Since there is an unavoidable difference in cooling rates between near-surface and internal areas, thinner versus thicker sections, locations first submerged versus those submerged last, and vertical versus horizontal surfaces, the generation of bulk residual stress and distortion is unavoidable. Oftentimes there are so many variables in play it can appear as though there is a high degree of randomness in the process if things are not carefully controlled. Our analysis tools can help.
The focus of this case study is the quench distortion of an aluminum aerospace forging. Using our modeling tools, we were able to capture the significant post-quench distortion in the forging, which is shown in the figure below. A rapid immersion quench, evenly applied, results in a very distorted and bowed output.
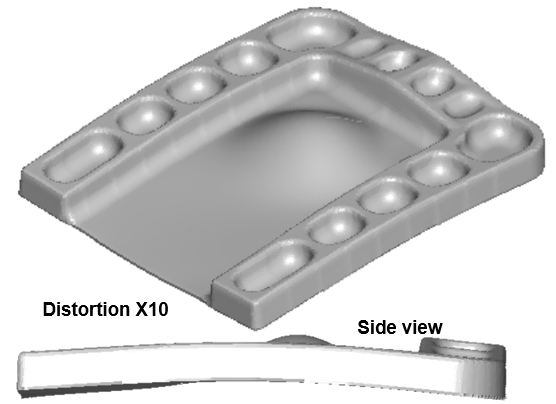
Illustration of predicted distortion of an aluminum forging during quench
Clearly, alternatives needed to be explored to mitigate the large amount of distortion. We considered several possibilities: slowing the cooling on one side (with a coating), removing the webbing before the quench (with machining), increasing the thickness of the webbing, or redesigning the forging with back-to-back symmetry by putting two parts into one forging. However, real-time physical experimentation of multiple options would be expensive and time consuming.
With modeling tools, we were able to quickly and effectively identify the most promising alternatives for improvement.
In this case, the biggest improvement came from removal of the webbing. The webbing is necessary for some of the initial forging operations, but does not need to be retained. It does not provide any coverage of the customer’s final post-machined part, and it is not necessary for heat treatment. Removing the webbing (i.e. cutting it off) prior to heat treatment requires an extra machining operation, but that is relatively inexpensive. As seen in the next figure, removing the webbing before quench resulted in a post-quench distortion that is remarkably reduced.
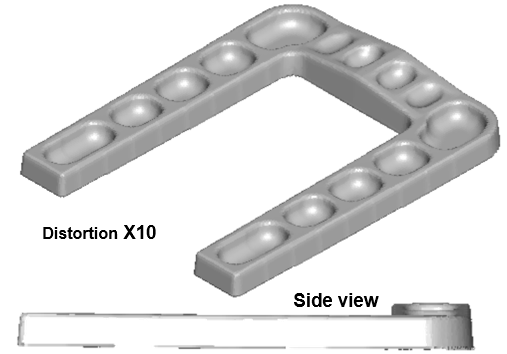
Illustration of predicted distortion for an alternate aluminum forging quench process that involves removing the webbing from the center prior to solution heat treatment and quench
The advantage of pre-production simulation is that problems can be found and solved beforehand, and the robustness of the proposed solutions can be tested and quantified.
Post-quench distortion is driven by bulk residual stress. That stress is created during the quench due to uneven cooling. Near surface cooling is much faster than the internal cooling of the part. This is unavoidable. However, using our modeling tools, the quench-induced residual stress can be predicted.
This predicted bulk residual stress is useful in follow-up simulations of post-machining distortion and part performance. The next figure shows the principal bulk residual stress as seen in section planes throughout the forging. Note that the residual stress reaches as high as 20.0 ksi in this aluminum 7075 simulation. This residual stress is post-quench and absent of any mechanical stress relief operations that are typically performed in subsequent steps.
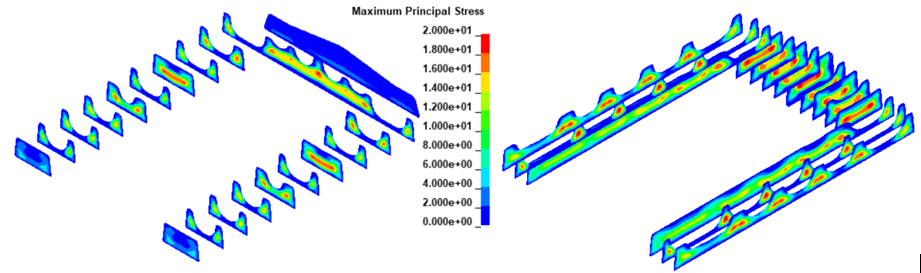
Illustration of predicted post-quench bulk residual stress in an aluminum forging
If this example relates to your production challenges, or if you have any questions about how these results might affect your projects, please do not hesitate to contact us. We would also be happy to answer any questions that you may have.
Analysis of distorted aerospace part
We recently uploaded a new case study on the topic of part distortion caused by residual stress during machining. We wanted to dive a little deeper into the topic with an analysis of a distorted aerospace part. Here is what we found. Continue reading Analysis of distorted aerospace part
Case Study: Multi-step machining distortion modeling
Distortion of parts during the machining process is a significant problem faced by many machining vendors. This phenomenon typically results from the release and redistribution of residual stress in the material once the part is unclamped from the machine table. When not accounted for, machining distortion can lead to out-of-tolerance parts that either require reworking, or have to be scrapped. Continue reading Case Study: Multi-step machining distortion modeling
Machining distortion modeling with multi-step models including residual stress
Distortion of finished parts during machining is a significant problem which typically results from release and redistribution of residual stress in the material once the part is unclamped from the machine table. If not accounted for,
This case study focuses on machining modeling of a representative aircraft specimen using multi-step finite element analysis. Machining modeling was used to identify a machining strategy that requires less machine time (e.g., fewer part set-ups) to arrive at the final geometry, while also reducing the distortion of the finished part. The results illustrate how multi-step machining models can be used to provide upfront estimates of distortion, as well as guidance to optimize machining processes and obtain improved machining outcomes.
The part geometry considered in this case study is shown in Figure 1, and was designed to be representative of an aircraft part. The overall dimensions are 25 x 10 x 2.5 inches. The pockets, stiffener walls, holes, and tapering along the 25 inch dimension and 2.5 inch dimension provide a complex and representative geometry. The part is assumed to be machined from a 27 x 12 x 3.5 inch plate of aluminum alloy 7050-T7451 (stress relieved by stretching). While this material state typically exhibits low levels of residual stress, distortion during machining can still occur depending on the part geometry, machining strategy, and required tolerances.
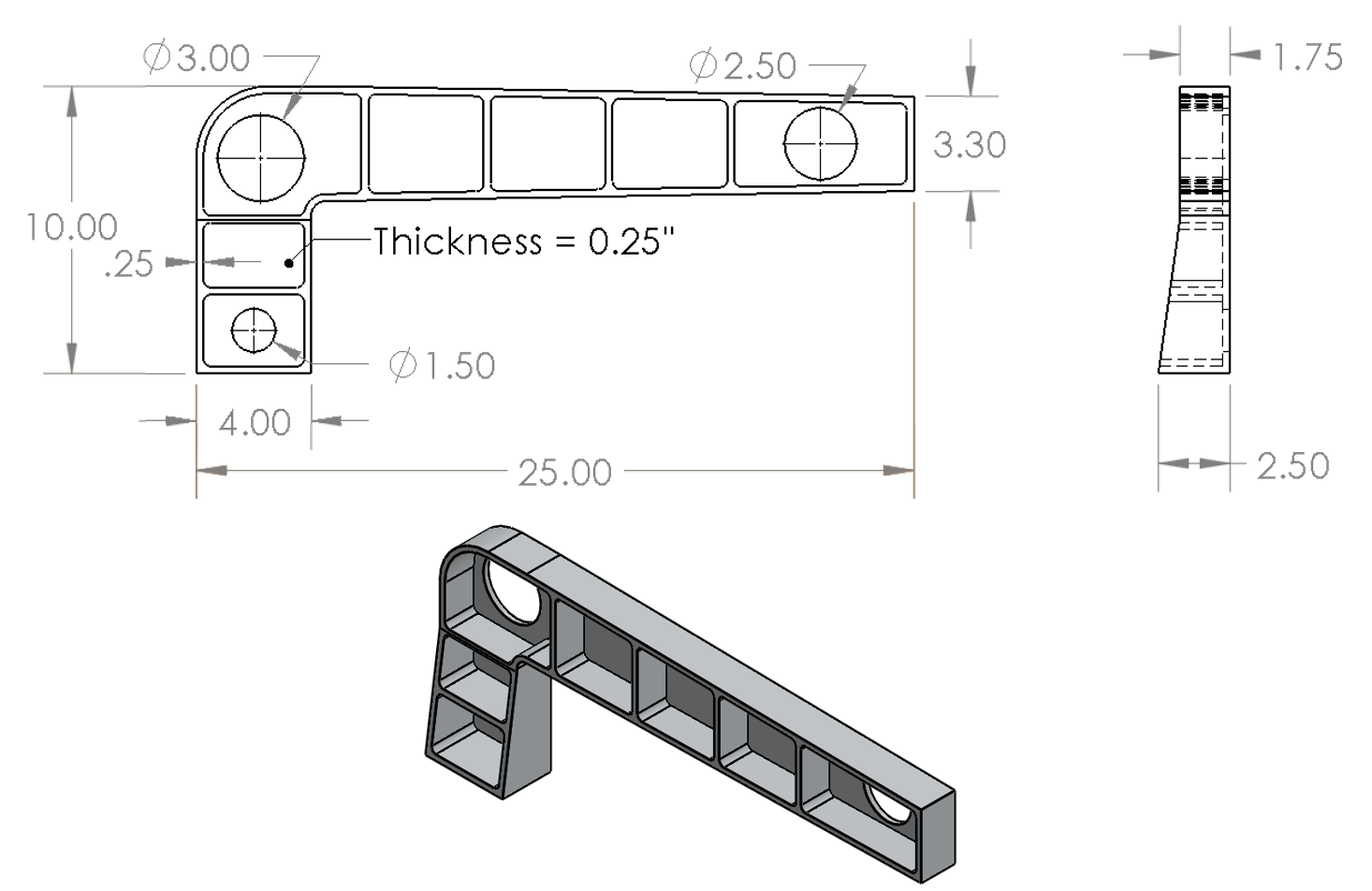
Part geometry (dimensions in inches)
The plate considered for machining this part provides extra material coverage on all sides. Figure 2 shows the amount of machining cover on each side, given the part is aligned with the mid-thickness of the stock plate with equal spacing relative to the sides of the stock. One inch of extra material is available on all sides when looking from a top view, while one-half inch of extra material is available along the thickness direction.
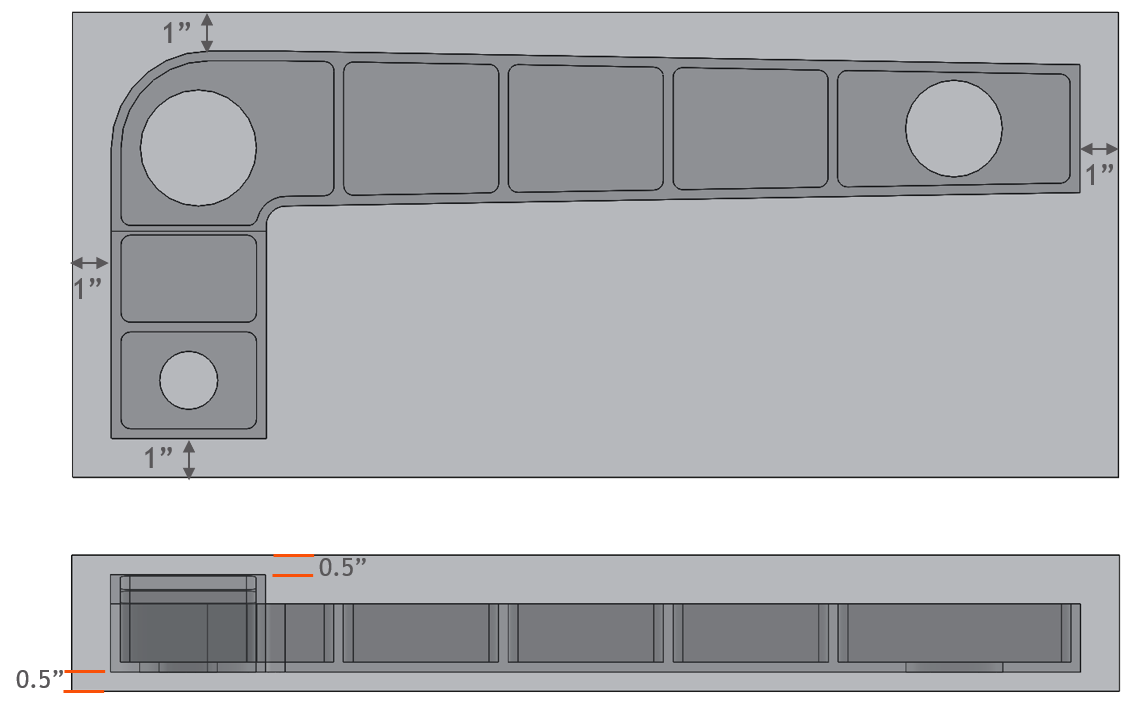
Part geometry within stock material when placed at the mid-thickness of the plate
The assumed residual stress in the stock plate material is shown in Figure 3. This is based on slitting method results published in [1] for 3-inch-thick plate of aluminum alloy 7050-T7451. The residual stress distributions are relatively symmetric and were normalized and scaled for the specific stock plate thickness used in the current study (3.5 inches). The rolling direction of the stock plate was assumed to be along the 27-inch dimension of the plate.
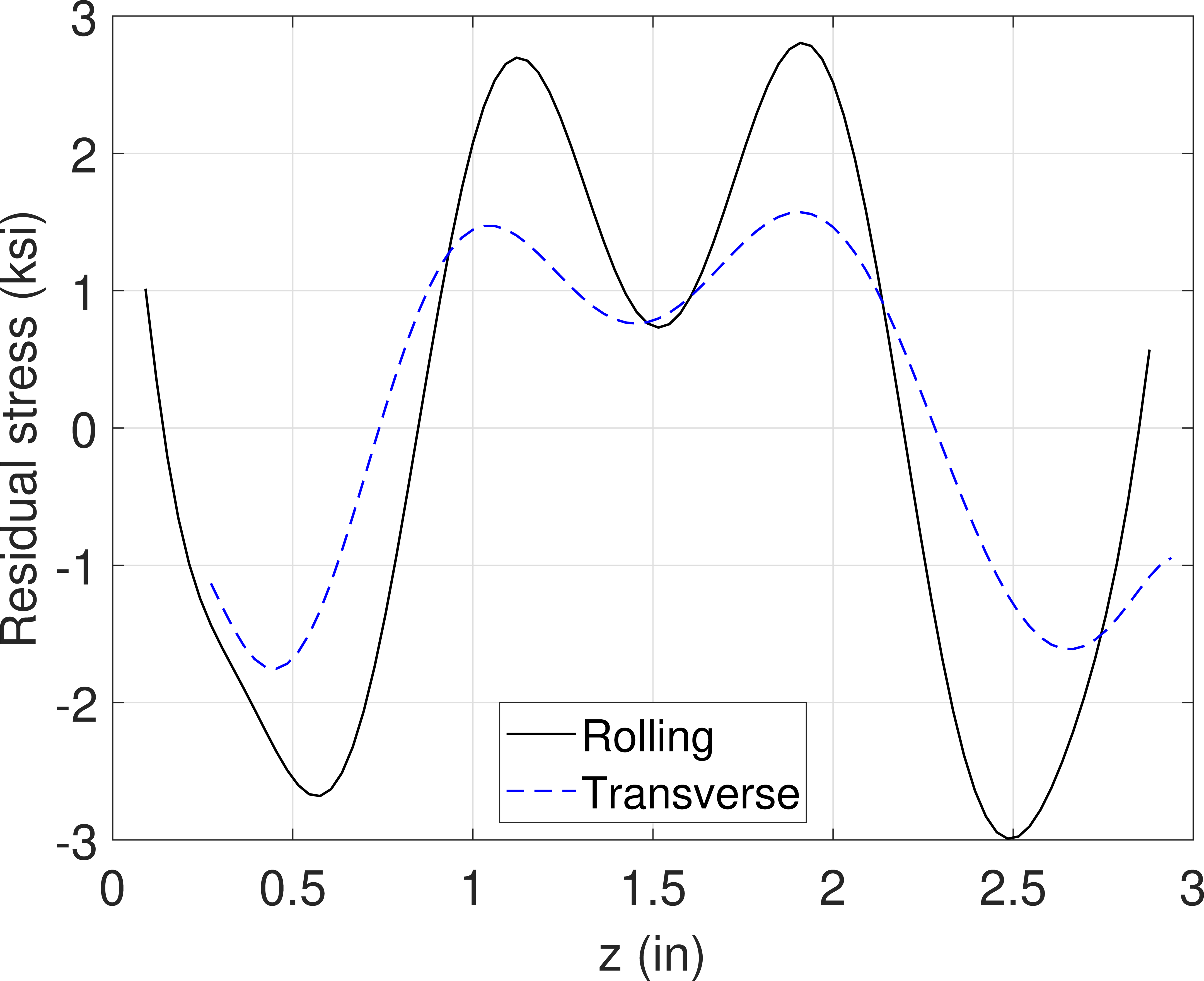
Residual stress measured in aluminum alloy 7050-T7451 plate (adapted from [1])
The baseline machining strategy considered is illustrated in Figure 4, in which the part is placed near the top surface of plate. Step 1 includes a rough machining pass on the bottom surface of the plate to obtain a flat surface for subsequent machining. Then, the part is flipped on the machine table. Step 2 involves an initial rough machining of the pockets and stiffener walls. Step 3 flips the part once again and finalizes machining of the bottom flat surface of the part. Finally, the part is flipped for the last time, and machining of the pockets, holes, and stiffener walls is finalized to arrive at the final geometry. This machining strategy includes a total of 3 flips on the machine table.

Part placement and baseline machining strategy
Multi-step finite element models were employed to obtain estimates of the distortion and residual stress at the end of each machining step. For brevity, the displacement of the finished part only (step 4) is shown here. Figure 5 shows a contour plot of the displacement along the z-axis (U3, perpendicular to the bottom flat surface of the part) on a scale that varies from -0.025 to 0.025 inches. The displacement U3 range (maximum minus minimum value) is about 0.030 inches. Maximum displacement is observed near the corner region of the part that contains the 3-inch diameter hole (shown in Figure 1).
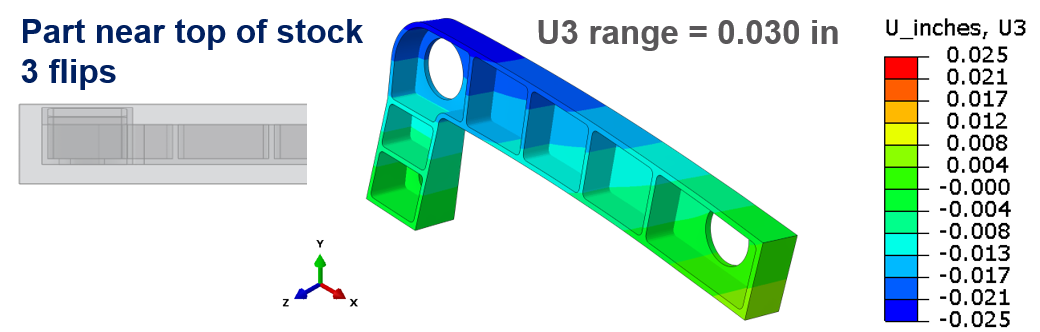
Contour plot of displacement along the z-axis (U3) for the finished part from the baseline strategy
Modeling was performed to simulate many different machining approaches. The optimal machining strategy places the part at the bottom surface of the stock plate as illustrated in Figure 6. The first step involves rough machining of the pockets and stiffener walls. The part is then flipped, and final-machined on the bottom flat surface. The second and final flip on the machine table provides the setup to final-machine the pockets, holes, and stiffener walls. This machining strategy uses a total of 2 flips (one less than the previous strategy).
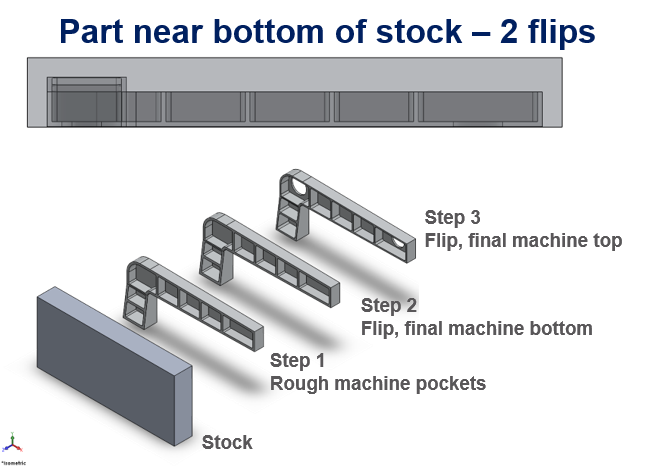
Part placement and optimized machining strategy
The part distortion for the optimized machining strategy is shown in Figure 7 (using the same color scale as in Figure 5). Compared to the baseline strategy (Figure 5), a different displacement pattern is observed, although the maximum values are near the same region (i.e., near the corner of the part with the 3-inch diameter hole). The displacement range is 0.013 inches for the optimized machining strategy, which is significantly lower than observed from the baseline approach (0.030 inches). It is important to note that the optimized strategy (which places the part near the bottom of the stock) not only provided a finished part with lower amount of distortion, it also required less machine time (fewer flips), which represents an improvement in efficiency of the machining process.
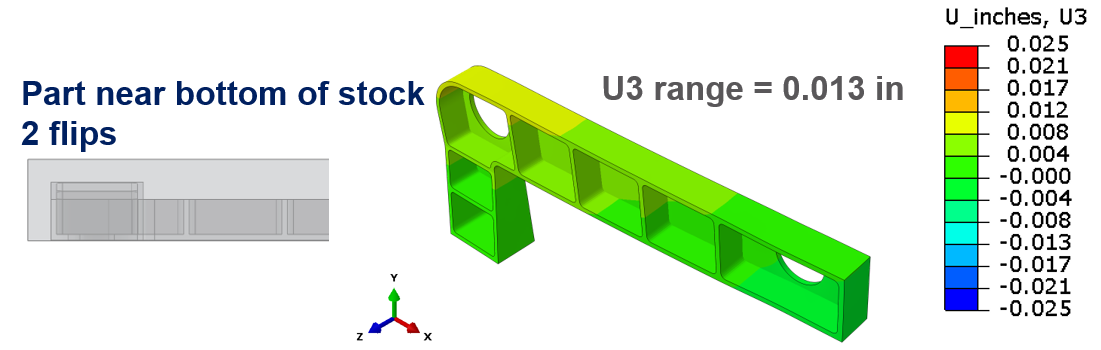
Contour plot of displacement along the z-axis for the finished part from the optimized strategy
This case study considered multi-step machining models of a representative aircraft specimen, including the residual stress in the incoming stock material, to assess the distortion of the finished part. Two different machining strategies were presented, which included differences in part placement within the stock material, and sequence of machining steps. The results identify an optimized machining strategy that uses fewer flips on the machine table (setups) to arrive at the final geometry, while also reducing the distortion of the finished part. The results illustrate how multi-step machining models can be used to provide upfront estimates of distortion and guidance to optimize machining processes in order to obtain improved outcomes. Please contact us for additional information.
Case Study highlight: Broad Application for Modeling Failure
Our latest case study discusses our Broad Application for Modeling Failure (BAMF) software.
Broad Application for Modeling Failure (BAMF) enables fatigue crack growth analysis of parts with non-standard geometry, loading, and residual stress conditions through the implementation of multi-point fracture mechanics (MPFM). This user-friendly software environment provides structural analysts and engineers a tool to accurately and efficiently complete challenging fatigue crack growth problems.
Continue reading Case Study highlight: Broad Application for Modeling FailureBAMpF®
BAMpF® (Broad Application for Multipoint Fatigue) enables fatigue crack growth analysis of parts with non-standard geometry, loading, and residual stress conditions through the implementation of multipoint fracture mechanics (MPFM). This user-friendly software environment provides structural analysts and engineers a tool to accurately and efficiently complete challenging fatigue crack growth problems.
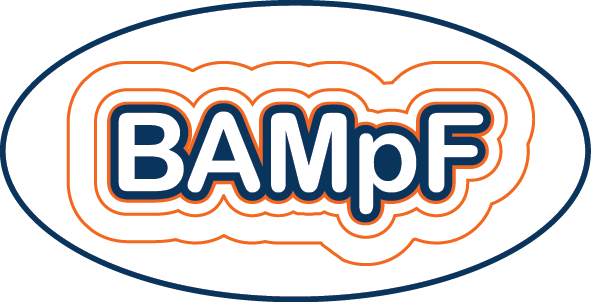
Starting from an assumed initial flaw, BAMpF® implements a multi-point fracture mechanics approach that allows crack shapes to evolve naturally as a function of the underlying, spatially varying stress fields and stress intensity factors. As illustrated in the figure below, the user specifies the number of points along the crack front to be used in the analysis. For each individual point, BAMpF® queries the stress intensity factor specific to the part geometry and loading through an interface with StressCheck® (a leading finite element software tool), provides the necessary inputs to AFGROW (a leading fatigue life assessment tool), and stores the expected fatigue crack growth for a given number of cycles. BAMpF® then combines the growth of each individual point into a new crack shape that serves as the starting point for the next increment of the analysis. This process is repeated until the fatigue crack reaches a critical size.
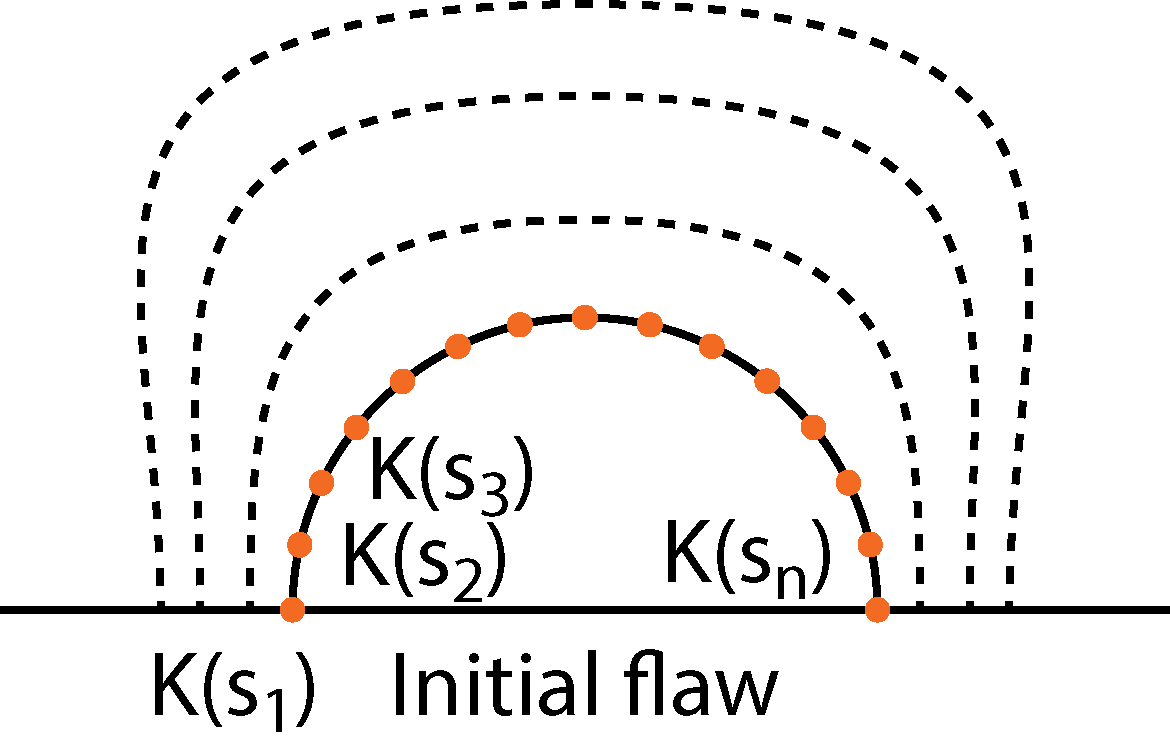
Illustration of multipoint fracture mechanics approach to defining individual control points around the crack front
Multipoint fracture mechanics improves the accuracy of fatigue crack growth calculations relative to traditional analysis methods by eliminating assumptions and constraints related to the shape of the crack (e.g. elliptical crack shapes are not required by MPFM). The use of MPFM is especially important when non-standard conditions like complex loading, complex geometry, and/or residual stresses are present as these factors tend to drive the evolution of the fatigue crack shape away from the circular/elliptical constraints imposed by the traditional analysis methods.
BAMpF® provides a straightforward approach for including residual stress in crack growth assessments. Residual stress input data for BAMpF® may come from measurement or process modeling (e.g., ERS-Toolbox®). The MPFM capabilities in BAMpF® enable accurate fatigue analysis of parts with laser shock peening (LSP), cold-expanded (CX) holes, of other bulk residual stress fields. For example, the figure below shows a comparison between the predicted (BAMpF®) and experimentally observed fatigue crack shape for a cold expanded hole test specimen.
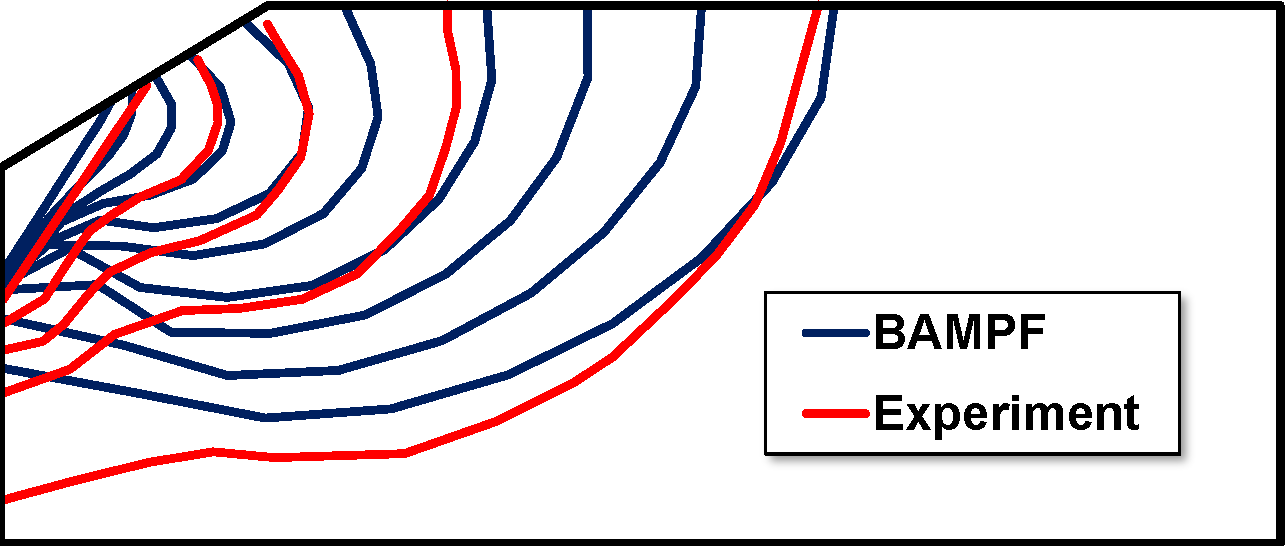
Fatigue crack growth analysis (BAMpF®) and experimental results for a cold expanded hole test specimen
Some of the key features and capabilities of BAMpF® include:
• Natural fatigue crack shape progression
• Fully 3D analysis
• Complex loading
• Multi-crack interactions and link-up
• Residual stress
BAMpF® has received software certification from the United States Airforce.
For more information about the study described above, our fatigue analysis and testing abilities, our residual stress engineering services, or to place an order for BAMpF® related goods and services, please contact us.
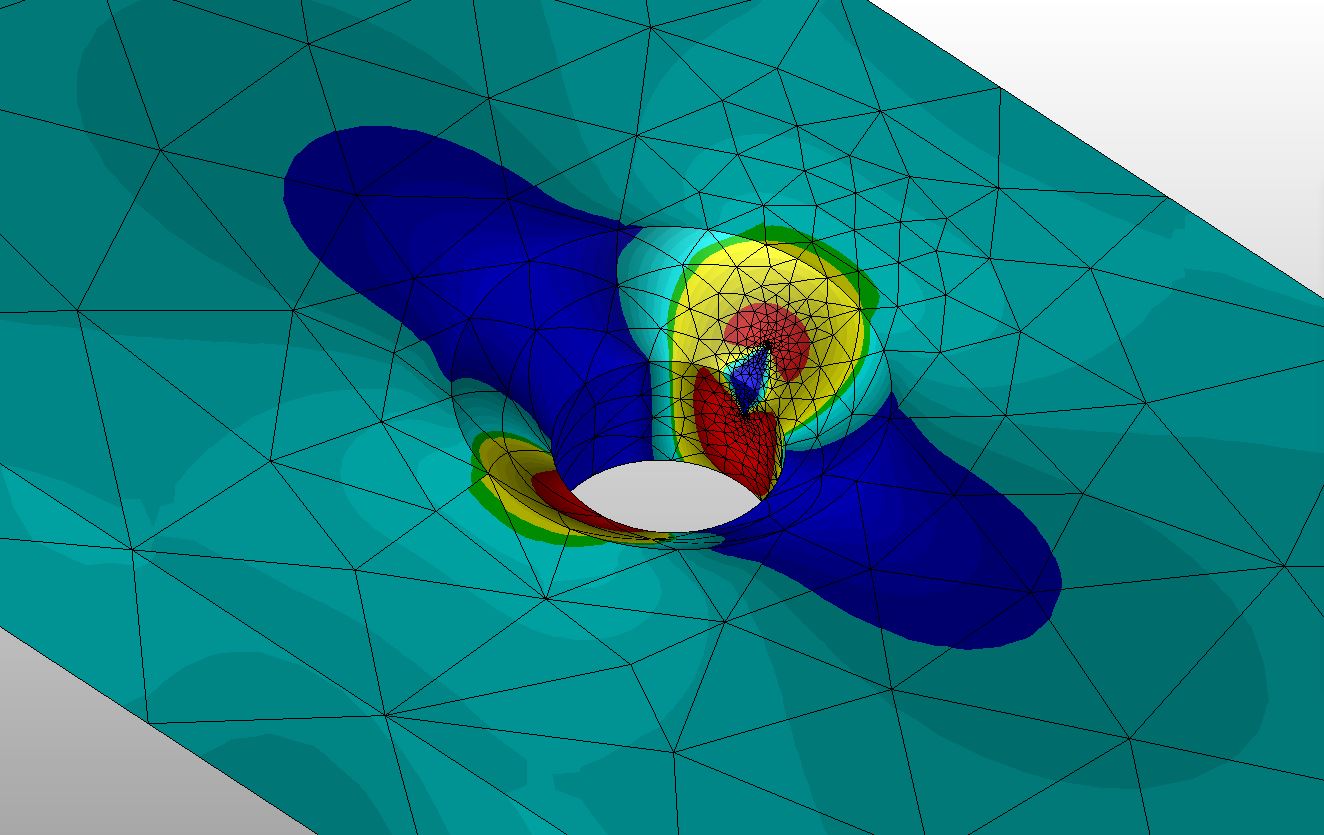
Image from a BAMpF® analysis showing the stress in a specimen with a small crack near a hole
Special thanks to our partners:
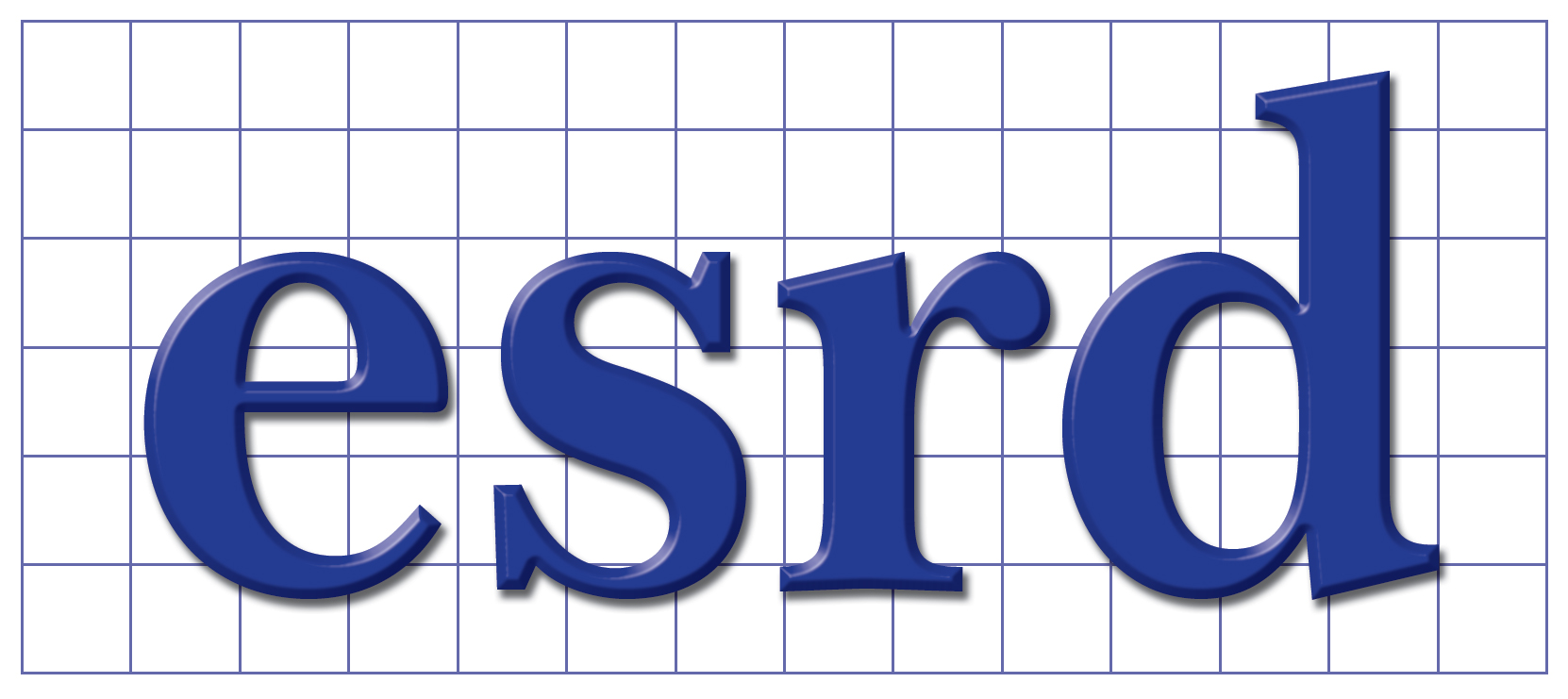
ESRD’s flagship software product, StressCheck® Professional, is an advanced FEA tool having numerous unique technical capabilities
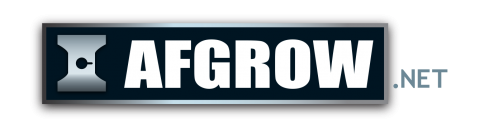
AFGROW is a Damage Tolerance Analysis (DTA) framework that allows users to analyze crack initiation, fatigue crack growth, and fracture to predict the life of metallic structures
Announcing agreement with ESRD for joint BAMF/StressCheck marketing
Hill Engineering and Engineering Software Research and Development, Inc. (ESRD) have executed a joint marketing agreement to collaboratively promote the combined use of our software tools: Broad Application for Modeling Failure (BAMF) and StressCheck® for fatigue analysis. Continue reading Announcing agreement with ESRD for joint BAMF/StressCheck marketing
Strain gage in a bottle
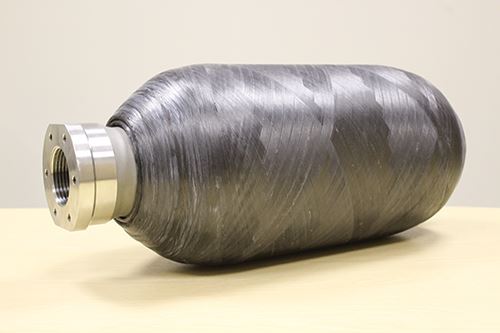
A representative composite overwrapped pressure vessel. Image courtesy of CompositesWorld: https://www.compositesworld.com/articles/thermoplastic-composite-pressure-vessels-for-fcvs
We’re putting something in a bottle, and no, it’s not an SOS to the world. It’s a strain gage!
Hill Engineering has recently developed technology to orient and apply strain gages inside a pressure vessel with restricted interior access. Continue reading Strain gage in a bottle
Residual Stress 101 vlog
Today, we’ve released the newest episode of our vlog: Residual Stress 101. The video is a return to basics, discussing the core of what it is we do here at Hill Engineering.
If you haven’t checked out our YouTube channel, it might be time. Our mission is to post content that helps highlight the capabilities of our organization, so that everyone can see how and why residual stress is important to their manufacturing processes.
Today’s post is a broad overview of what residual stress is, including the several techniques for measuring residual stress found in our lab. Look for future content that delves further into each technique, and contact us if you have any further questions or want to see a video related to something we haven’t discussed.