In a recent blog post we discussed the question: what is residual stress. As a follow-up, today we are addressing the topic of residual stress calculation. Once you understand the concept of residual stress and are ready to account for its effect on material performance it’s important to quantify the residual stress that is present in your material. Residual stress calculation can include a variety of different topics.
One way to calculate the residual stress in a part is through testing. There are a variety of residual stress measurement techniques available. You can research the available residual stress measurement techniques on our website (and elsewhere on the internet) to determine which one is most appropriate for quantifying the residual stress information that is of interest to you. Or you can contact us and we can help you understand the available options. Residual stress measurement results from a sample of the population can form a solid basis for a residual stress calculation.
Another approach to residual stress calculation is through the use of an analytical model. For example, the residual stress in welded structures is often estimated through weld process simulations; or—for the case of compressive residual stress surface treatments like laser peening—Hill Engineering’s own ERS-toolbox® software can be used to provide a residual stress calculation.
It is often best to perform residual stress calculations based on both model and measurement results. For example, the figure below shows the residual stress calculations for an aluminum forging using a process model and contour method measurements.
If you have any questions about residual stress calculation please contact us for more information. We’d be happy to write a future blog post expanding on your questions about residual stress calculation or other topics of interest.
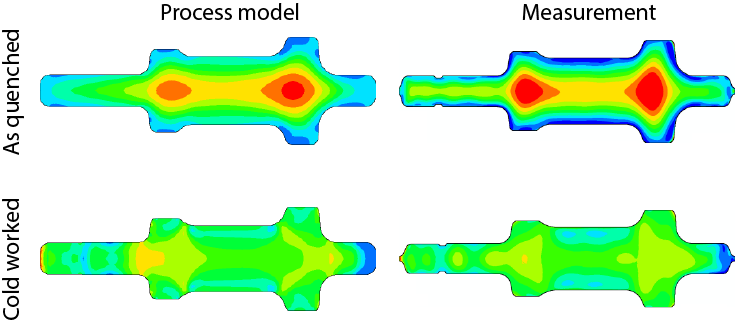
Residual stress calculation in a quenched forging (top) and a cold-compressed forging (bottom) – model forecast (left) and measurement data (right) with tension in red and compression in blue