Measurement precision and uncertainty estimation are important factors for all residual stress measurement techniques. The values of these quantities can help to determine whether a particular measurement technique would be viable option. This paper determines the precision of hole-drilling residual stress measurement using repeatability studies and develops an updated uncertainty estimator. Two repeatability studies were performed on test specimens extracted from aluminum and titanium shot peened plates. Each repeatability study included 12 hole-drilling measurements performed using a bespoke automated milling machine. Repeatability standard deviations were determined for each population. The repeatability studies were replicated using a commercially available manual hole-drilling milling machine. An updated uncertainty estimator was developed and was assessed using an acceptance criterion. The acceptance criterion compared an expected percentage of points (68%) to the fraction of points in the stress versus depth profile where the measured stresses ± its total uncertainty contained the mean stress of the repeatability studies. Both repeatability studies showed larger repeatability standard deviations at the surface that decay quickly (over about 0.3 mm). The repeatability standard deviation was significantly smaller in the aluminum plate (max ≈ 15 MPa, RMS ≈ 6.4 MPa) than in the titanium plate (max ≈ 60 MPa, RMS ≈ 21.0 MPa). The repeatability standard deviations were significantly larger when using the manual milling machine in the aluminum plate (RMS ≈ 21.7 MPa), and for the titanium plate (RMS ≈ 18.9 MPa). The single measurement uncertainty estimate met a defined acceptance criterion based on the confidence interval of the uncertainty estimate.
Archives: Case Studies
DART – automated residual stress measurement
Near-surface residual stress data is critical when assessing material performance, optimizing design, validating models, evaluating field failures, and executing quality assurance programs. Hill Engineering’s DART™ is an industry-leading tool for efficient, precise, and reliable near-surface residual stress measurements. The DART™ overcomes limitations of existing residual stress measurement equipment and includes everything required to perform state-of-the-art measurements in accordance with industry specifications.
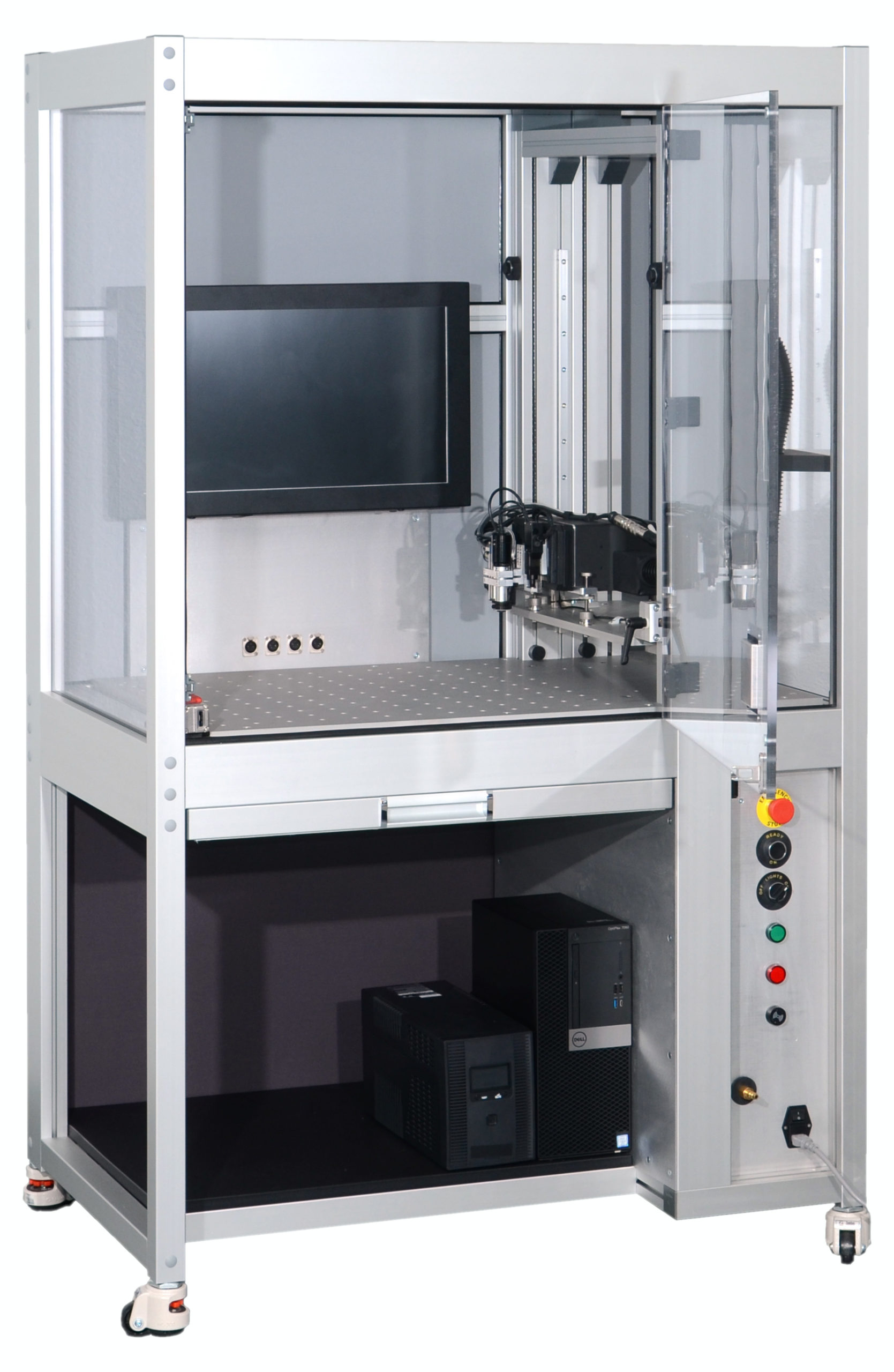
Hill Engineering’s DART™
A single DART™ can perform near-surface residual stress measurements using multiple techniques including hole drilling
and TRUEslot® methods. This flexibility is helpful when requirements change or new applications arise. The DART™ executes hole-drilling residual stress profile measurements in accordance with ASTM E837, providing a depth profile of the three in-plane residual stress components in a single measurement. TRUEslot® is a novel technique, like hole-drilling, but simpler and more precise. TRUEslot® provides a depth profile of one stress component per measurement.

Hole drilling measurement example
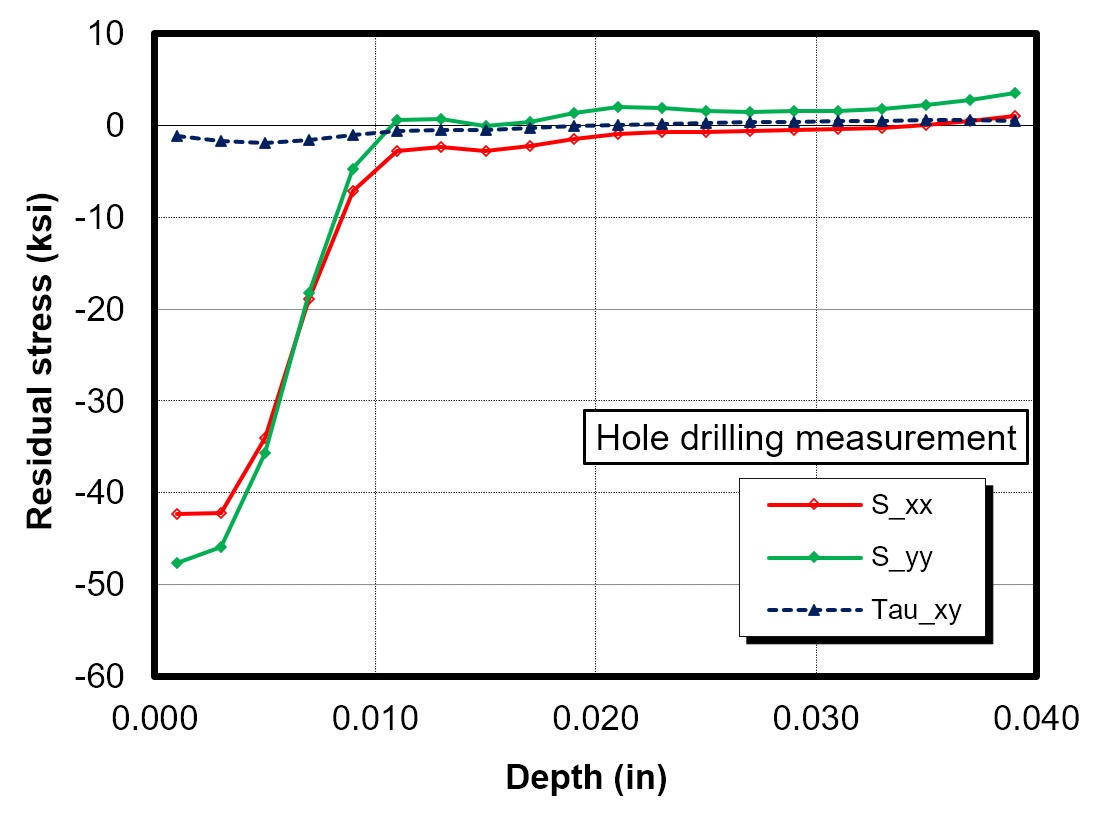
Hole drilling results example
Intuitive
Residual stress measurements with the DART™ are easy to complete. A user interface guides you through set-up, then takes over for automated measurement execution and residual stress calculation.
Efficient
With measurements completing in less than 60 minutes, the DART™ excels in the production quality management environment. Automated data capture, processing, and archiving provide you with residual stress results instantly.
Reliable
Featuring advanced cutting strategies and real-time quality checks, the DART™ gives you confidence in your residual stress data.
Features
• Hole drilling residual stress measurements according to ASTM E837
• TRUEslot® residual stress measurements
• Positional accuracy: ± 0.001 in.
• Works on most materials including: aluminum, titanium, steel, stainless steel, and nickel alloys
• Custom fixtures can be integrated to meet the needs of individual applications
• NFPA 79 compliant
Software
Each DART™ includes a complete software package that enables efficient and repeatable residual stress measurements for high-volume or single-use applications. DART™ software is designed for ease-of-use, while maintaining flexibility to meet your measurement needs and providing controls to maximize reliability. An operator defines the measurement location, the type of measurement (TRUEslot® or hole-drilling), and inputs the key measurement details. Following set-up, the software automatically controls the incremental material removal process, acquires the experimental data, computes residual stress, and outputs a test report. The entire process is significantly more efficient than other available tools.
DART™ produces the highest-quality residual stress data available
Precise engineering and extensive use of automation within the DART™ provides a demonstrated 50%+ improvement in measurement repeatability relative to other hole drilling test equipment. Hole drilling and TRUEslot® measurements performed using a DART™ have been shown to be 60%+ more repeatable than X-ray diffraction measurements.
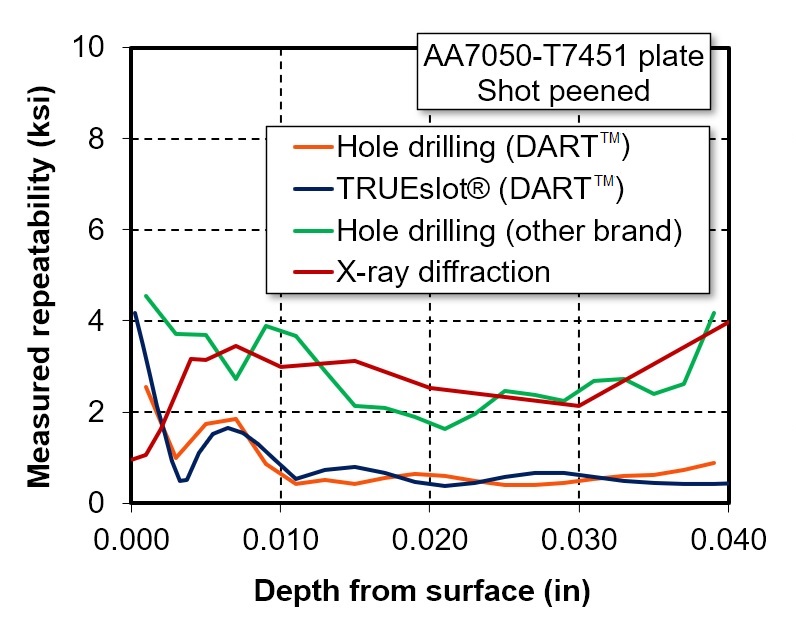
DART™ outperforms its competitors in RS measurement repeatability
The DART™ has proven to meet our high internal standards for data quality and is currently in use in multiple facilities throughout the world. It could be in your facility soon.
To place an order for DART™ related goods or services, please contact us.
Download a DART™ brochure here
The following are a list of patents pertaining to DART™ and TRUEslot®. Additional patents are pending for other international jurisdictions.
United States
- US10900768B2 – Systems and methods for analysis of material properties of components and structures using machining processes to enable stress relief in the material under test
Japan
- JP7258393B2 – Analysis that enables stress relaxation of the material under test
- JP2023025055A – Analysis that allows stress relaxation in material to be tested
Contour method uncertainty
The contour method is a residual stress measurement technique that provides a two-dimensional map of residual stress on a plane. Hill Engineering’s uncertainty estimate for contour method measurements is summarized here. For additional information, refer to the references below.
The contour method uncertainty estimate accounts for two main, random uncertainty sources present in contour method measurements. This includes the uncertainty associated with random noise in the surface height profiles called the displacement error, and the uncertainty associated with choosing a specific analytical model to fit the surface profiles called the model error.
The displacement error is estimated using a Monte Carlo approach that applies normally distributed noise to the each of the original measured surfaces. The normally distributed noise is prescribed to have approximately the same magnitude as the surface roughness that arises from EDM cutting. Stress results are found using five different sets of random noise added to the surface height profiles, and the standard deviation of those five residual stress results at each spatial location is taken as the displacement error.
The model error is estimated by taking the standard deviation of the residual stress results using displacement surface profiles that have been fit with different analytical models (centered around what was determined to be the best fit). Each case uses a different number of fitting coefficients.
The total contour method uncertainty is then taken as the root-sum-square of the displacement and model errors with a minimum value of uncertainty set as a floor. The floor used is the mean of the total uncertainty (prior to the application of the floor), which is evaluated over a regular grid. The uncertainty estimate is assumed to have a normal distribution, which implies that one standard deviation represents a 68% confidence interval.
An illustrative example of the contour method uncertainty calculation is provided below from a measurement on a dissimilar metal welded plate.
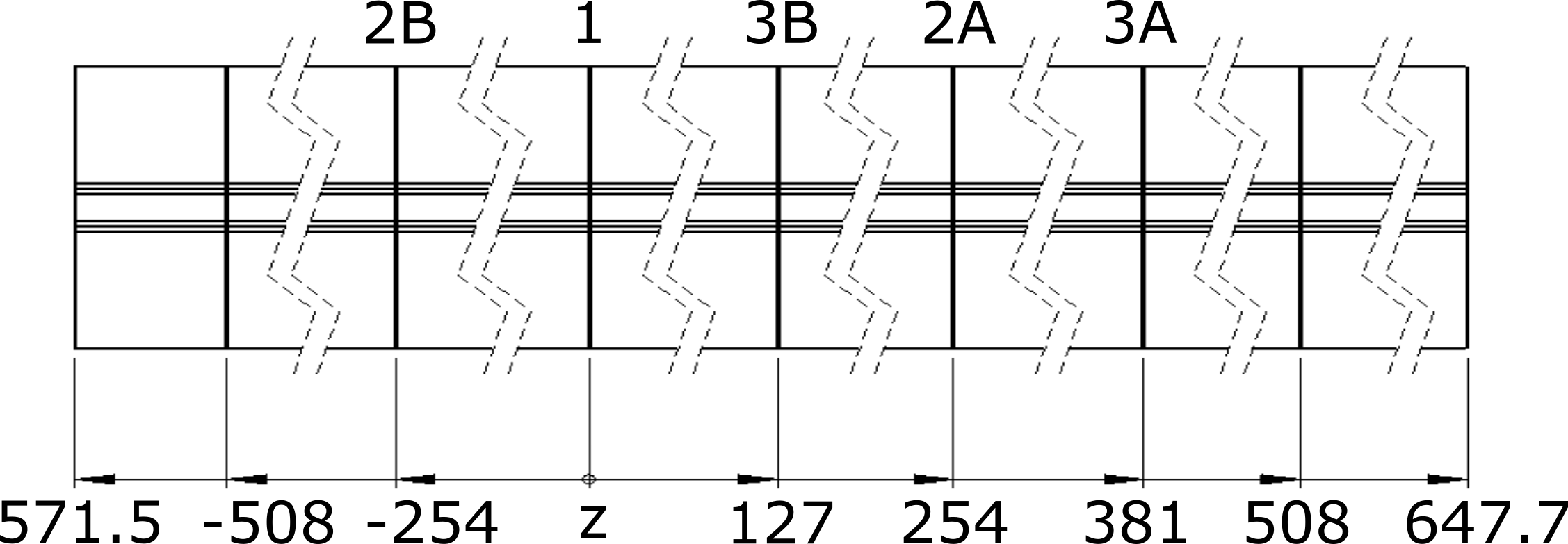
Stainless steel dissimilar metal dimensions and measurement locations (dimensions in mm)
The measured residual stress in the test specimen is shown below.
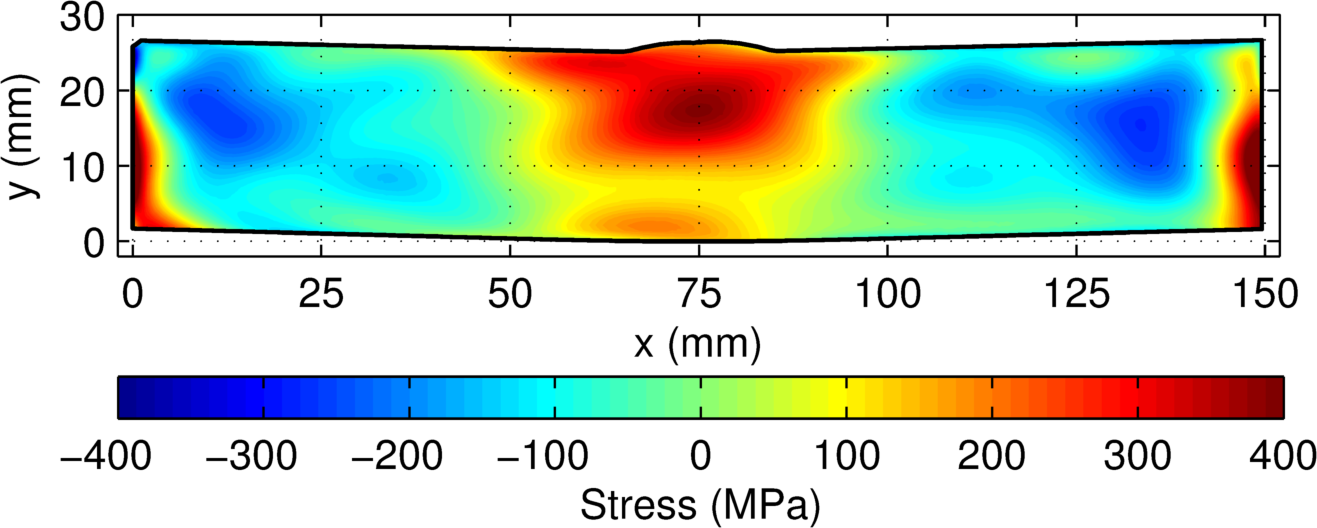
Measured residual stress (σzz)
The model error for the measurement (below) is largest along the part boundary (95th percentile is at 41.0 MPa). The displacement error (also shown below) is largest along the part boundary (95th percentile is at 11.8 MPa). The displacement error is much smaller than the model error. The total uncertainty has nearly the same distribution as the model error (95th percentile is at 42.5 MPa) with a 17.5 MPa floor covering most of the cross-section.
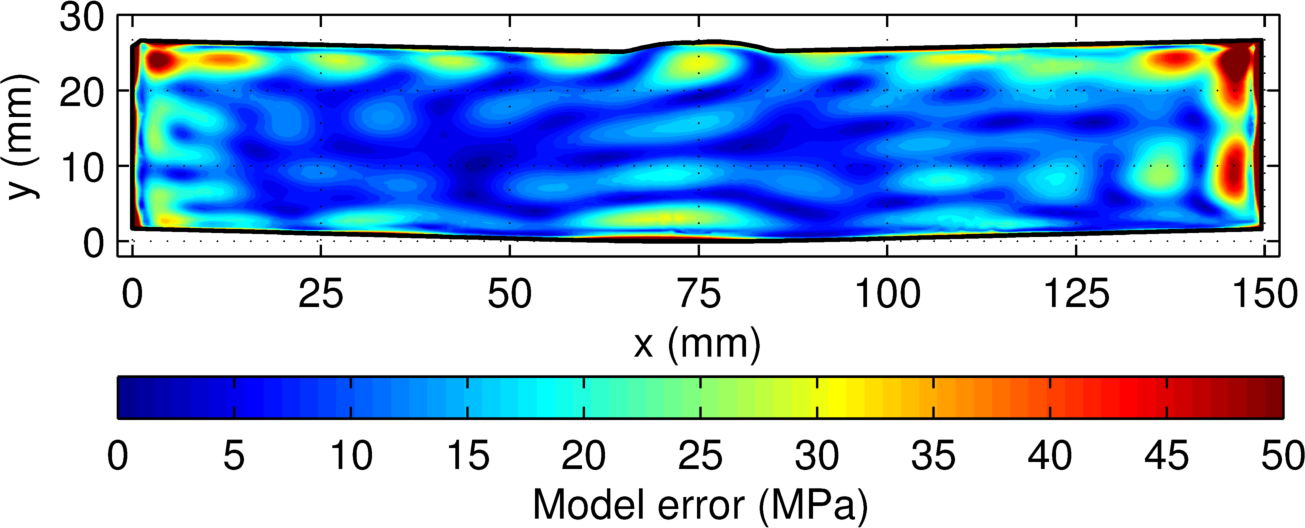
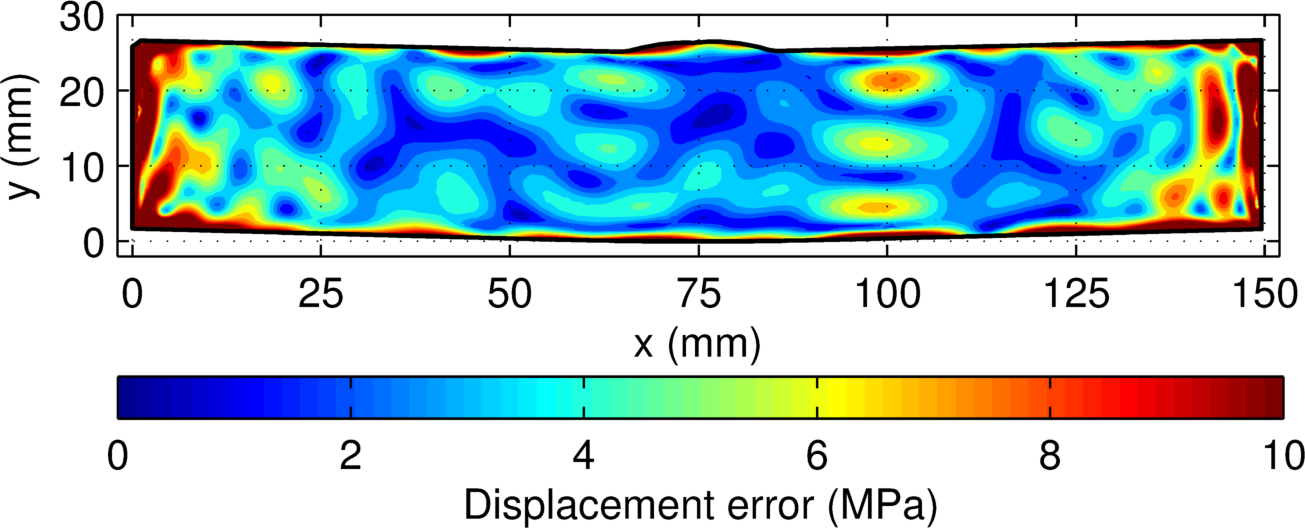
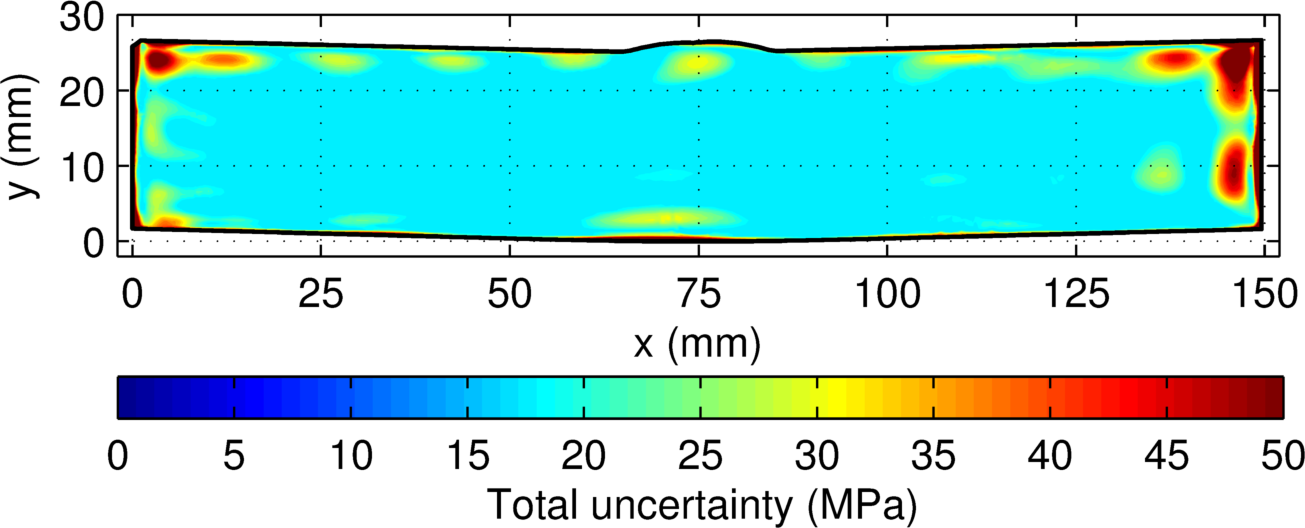
(top) Displacement error, (middle) model error, and (bottom) total uncertainty for the stainless steel DM welded samples
If you would like more information about using the contour method to determine a 2D map of residual stress in your parts please contact us.
Mechanical stress relief of aluminum alloys
As we discuss in a related case study, aluminum alloy heat treatment is a three-step process designed to achieve the desired properties. The process involves: 1) solution heat treatment (SHT) at an elevated temperature below the melting point, 2) quenching in a tank of fluid (e.g., 140-180°F water), and 3) age hardening. While providing good properties, the heat treatment has the negative side effect of creating bulk residual stress and distortion. These side-effects are a direct result of non-uniform cooling during the rapid quench. One approach to mitigate this problem is the application of a post-heat treatment mechanical stress relief process. In addition to modeling the heat treatment process, our analysis tools can support evaluation and optimization of mechanical stress relief processes.
Mechanical stress relief is practical for many aluminum alloy products as a means of reducing bulk residual stress. For products with a uniform cross section, such as most extrusions, plate, and bar stock, the material can be stretched on the order of 1% to 5% using special equipment. The figure below shows an example extrusion section with bulk residual stress (top) along with the remaining residual stress after mechanical stress relief (bottom). Note, the use of different color scales because the residual stress magnitude changes so significantly. This figure illustrates our capability to model post-quench and post-stretch residual stress.
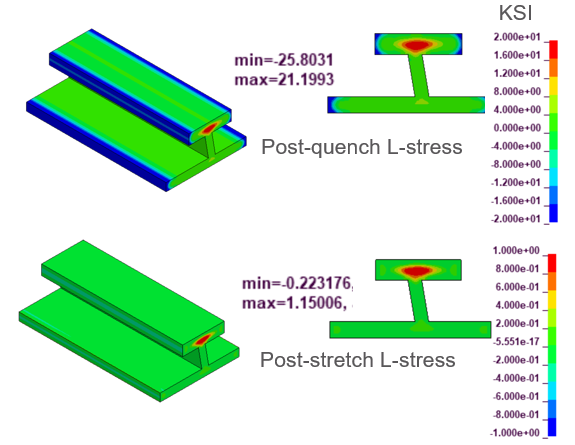
Illustration of predicted post-quench (top) and post-mechanical-stress-relief-stretch (bottom) in the long direction of an example aluminum extrusion
For other products such as forgings, an alternative stress-relief process using a compressive cold work stress relief can be employed. For a hand forging this is usually achieved using open-dies comprised of mostly flat surfaces. Post-quench, the hand forging is subjected to 1% to 5% compression often in an overlapping fashion.
On the other hand, an impression-die forging usually requires a more complex process that involves a cold-work die set. Such die sets are designed to impress 1% to 5% cold-work. Typically, the compression is on the order of 1% in thinner web sections and 3% in thicker rib sections. Since the forging will be at room temperature for the compression (therefore the term – cold-work) it does require higher press loads than one sees in the hot forging operation. The following figure illustrates the elements of a cold-work die set.
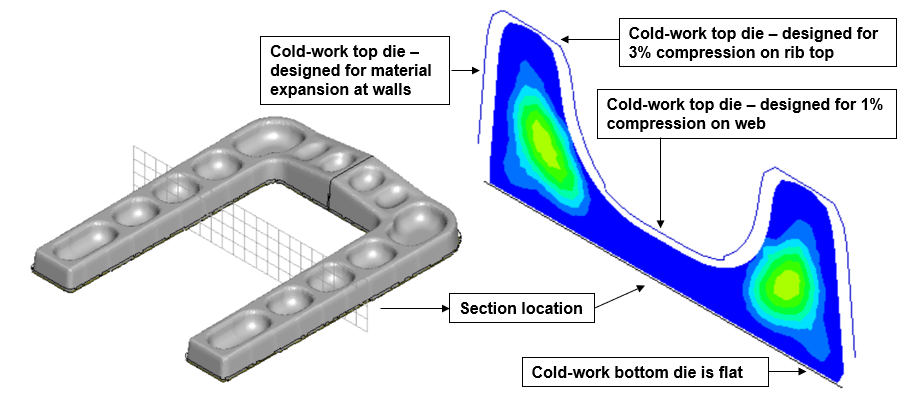
Illustration of a typical cold-work die set for mechanical stress relief of an aluminum forging
In a previous case study, we demonstrated our capability to predict post-quench residual stress and distortion for an example forging. The effect of mechanical stress relief using compression dies on that same example forging is shown below. The post-quench residual stress (left) reaches as high as 20.0 ksi in this aluminum 7075 simulation. The post-cold-work residual stress (right) is significantly reduced. The reduced residual stress level in the stress-relieved state has significant advantages in terms of ease of machining (reduced distortion) and improved part performance.
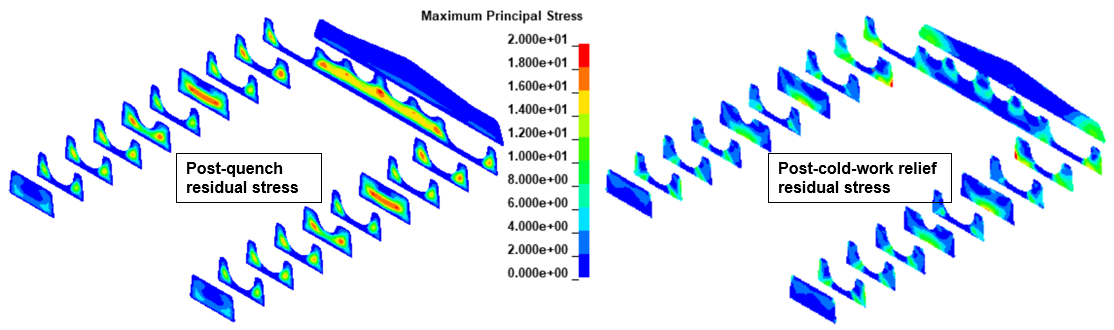
Predicted residual stress post-quench (left) and post-cold-work-stress-relief (right) for an example aluminum forging
If this example relates to your production challenges, or if you have any questions about how these results might affect your projects, please do not hesitate to contact us. We would also be happy to answer any questions that you may have.
Rapid Forge Design
Hill Engineering’s Rapid Forge Design™ software is an automated tool for fast and reliable design of 2-piece, closed-die impression forgings. Rapid Forge Design™ reads the final part geometry and automatically designs a forging according to accepted industry guidelines and user inputs. Rapid Forge Design™ is intended for use by forging suppliers and forging consumers/OEMs.
The Rapid Forge Design™ software comes with a user-friendly, graphical interface that allows for forging designs using a simple, 3-step, menu guided approach.
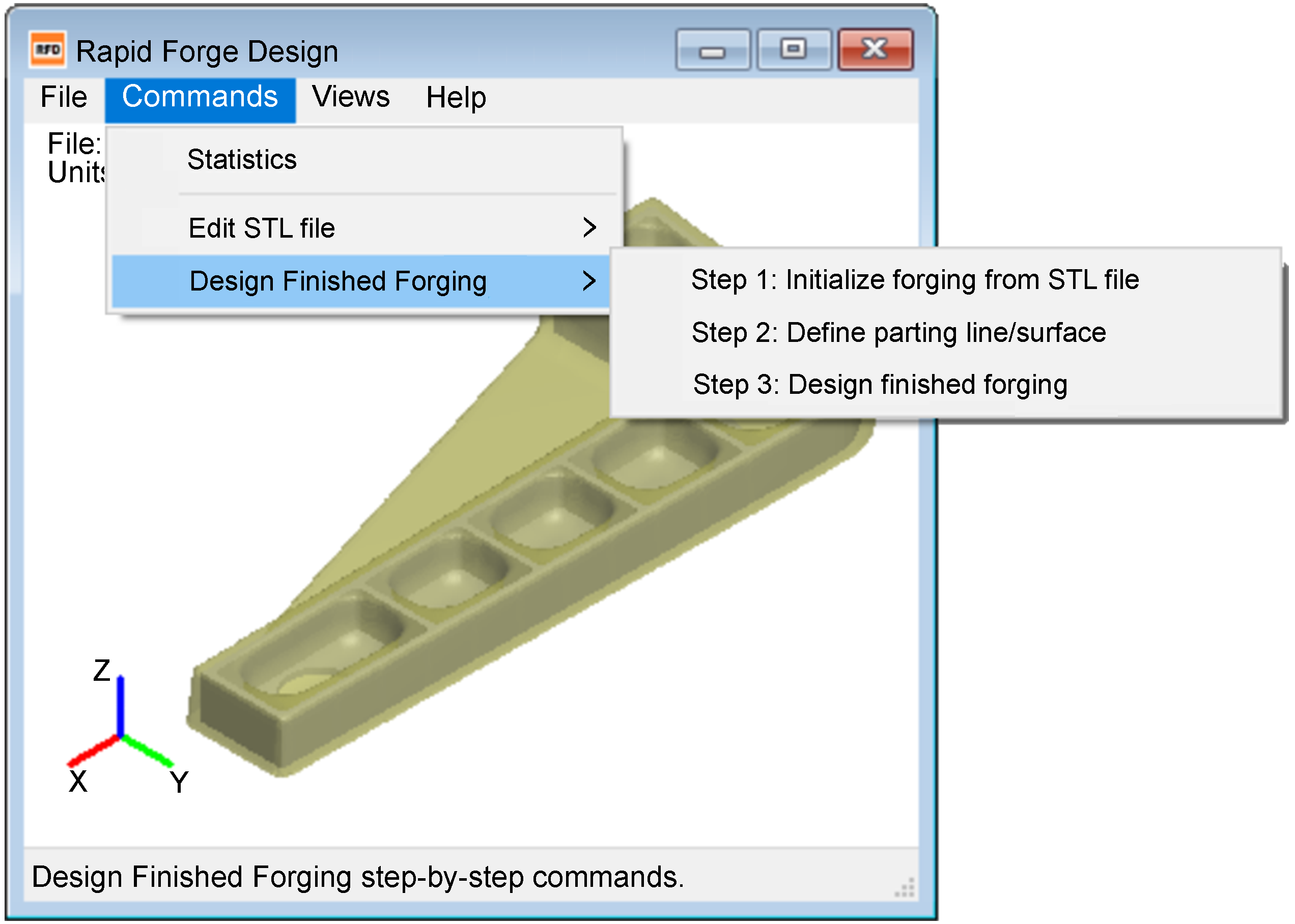
Illustration of Rapid Forge Design™ user interface
The inputs to Rapid Forge Design™ are the 3D geometry of the machined part (to be manufactured from the forging) and critical, user-defined parameters that allow for customization of the resulting forging design (e.g., minimum thickness and minimum radius values).
The forging design is generated by Rapid Forge Design™ according to a set of prescribed, industry-accepted design rules. After the user inputs are provided, the automated forging design process is completed by Rapid Forge Design™ in minutes without any further user intervention. With this approach, Rapid Forge Design™ enables the design of forgings with significantly less effort than existing manual processes.
Rapid Forge Design™ outputs the 3D geometry of the forging and a host of useful forging statistics and properties including volume, plan view area, periphery length, heat treatment section thickness, and other dimensional information. These metrics are essential to support the quoting process (material producers) and planning and costing activities (OEMs).
The preliminary forging designs produced by Rapid Forge Design™ can be used as the starting point for the finished forging’s more detailed design and tooling CAD files.
The Rapid Forge Design™ process is outlined in the flowchart below. The operator can input and customize important design parameters including: web thickness, draft wall cover, draft wall angle, plan view radius, fillet radius, and corner radius. Default values are provided based on alloy dependent industry standards. Help menus provide additional support and guidance, where necessary.
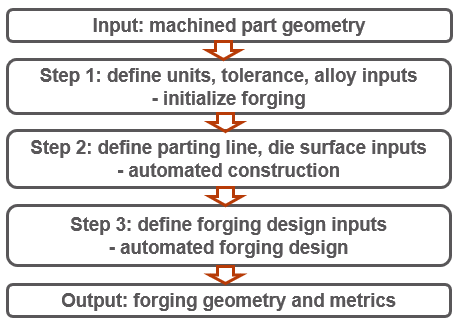
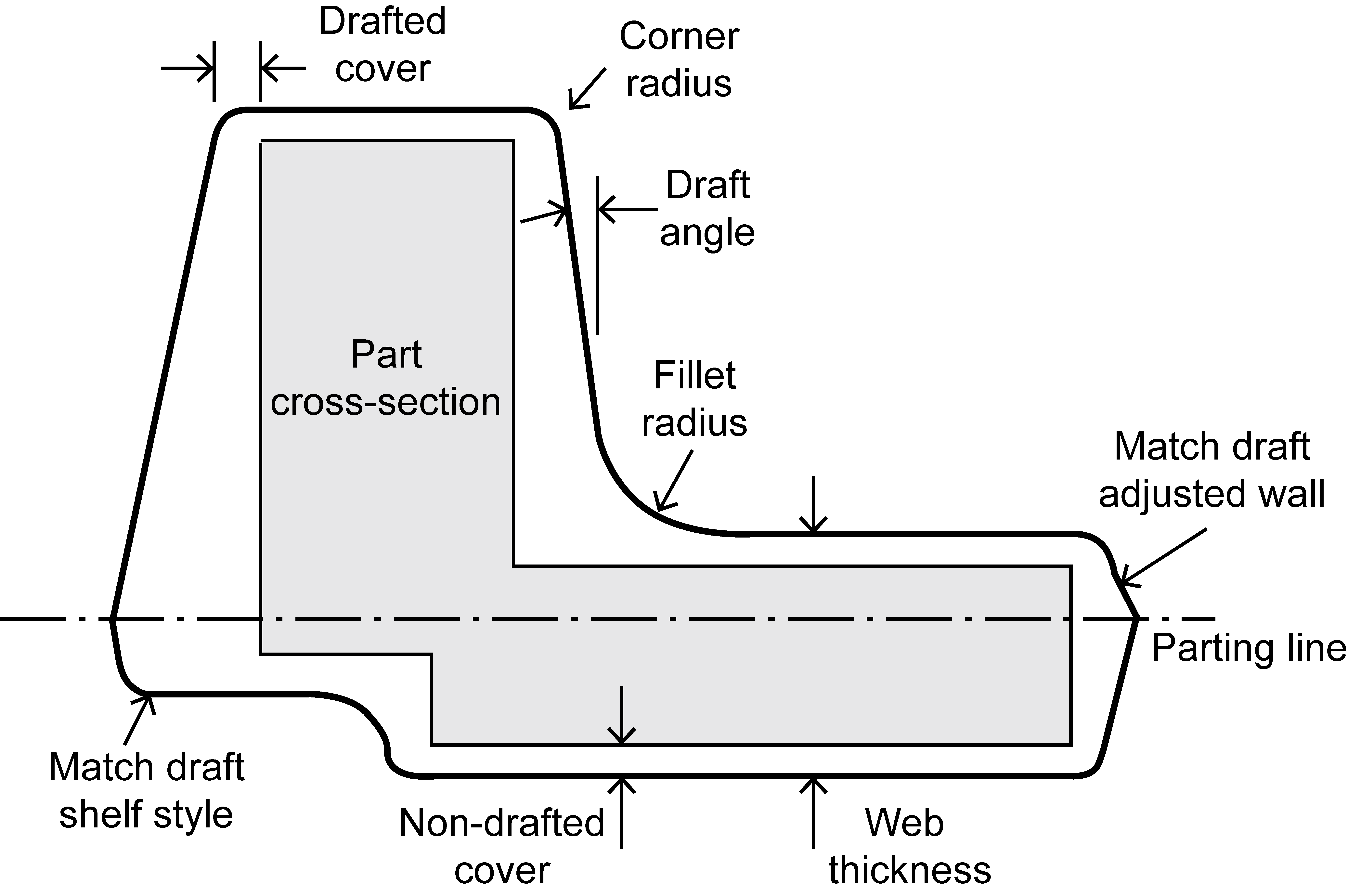
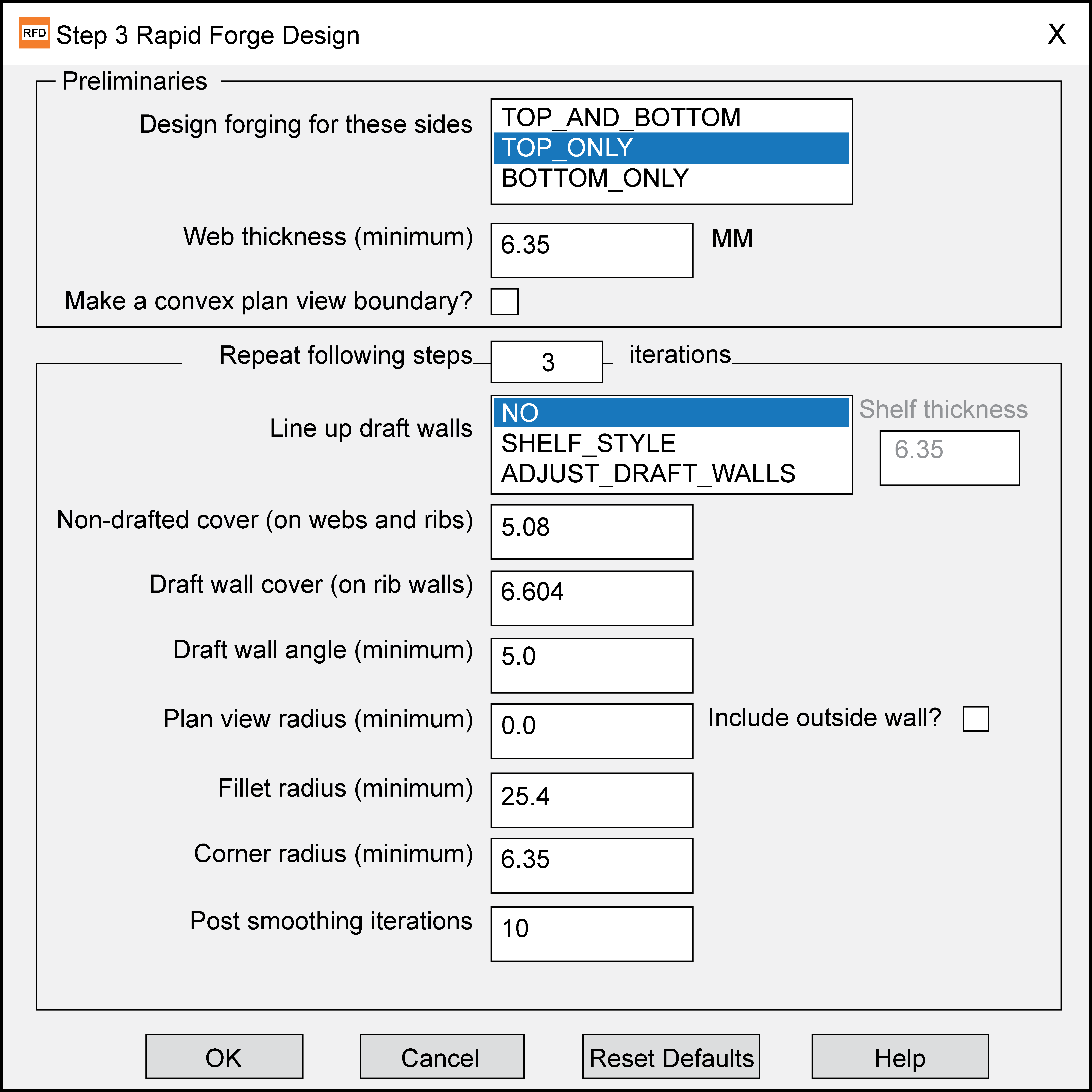
Summary of Rapid Forge Design™ workflow
Numerous examples taken from publicly available CAD files come with the software. The following are a few illustrations showing the ability of Rapid Forge Design™ to effectively produce forging designs for a wide variety of supplied final part geometry.
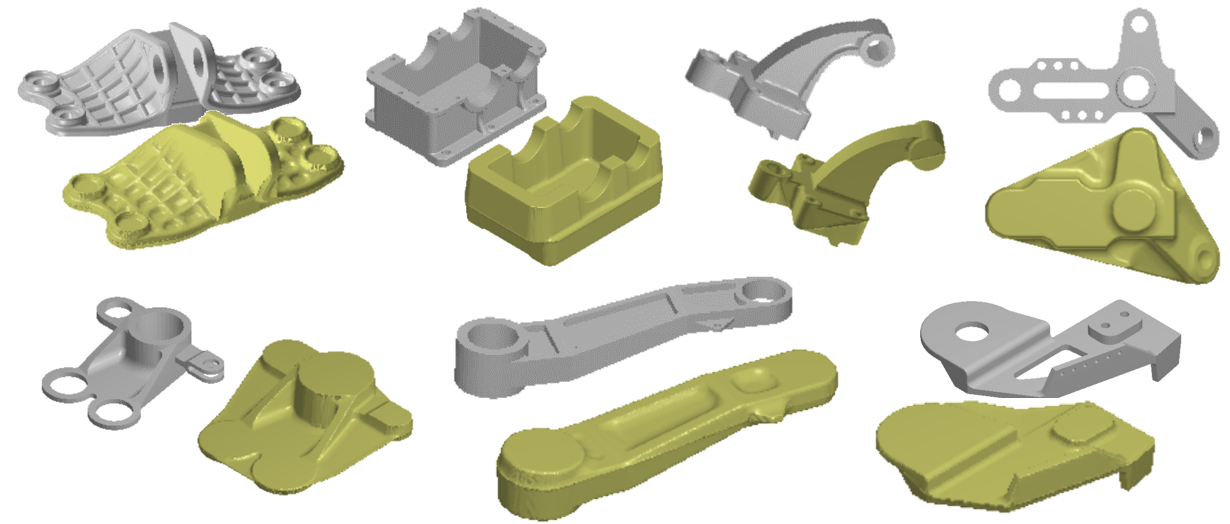
Illustration of forging designs produced by Rapid Forge Design™ (gold) along with the final machined part geometry that was used as the input for design (grey)
https://www.youtube.com/watch?v=wV3Vb4-DUV4
To place an order for Rapid Forge Design™ related goods and services, please contact us.
Aluminum forging quench modeling
Aluminum alloy heat treatment is a three-step process designed to achieve desired properties. The process involves: 1) solution heat treatment (SHT) at an elevated temperature below the melting point, 2) quenching in a tank of fluid (e.g., 140-180°F water), and 3) age hardening. While providing good properties, the heat treatment has the negative side effect of creating bulk residual stress and distortion. These side-effects are a direct result of non-uniform cooling during the rapid, time-dependent quench. Since there is an unavoidable difference in cooling rates between near-surface and internal areas, thinner versus thicker sections, locations first submerged versus those submerged last, and vertical versus horizontal surfaces, the generation of bulk residual stress and distortion is unavoidable. Oftentimes there are so many variables in play it can appear as though there is a high degree of randomness in the process if things are not carefully controlled. Our analysis tools can help.
The focus of this case study is the quench distortion of an aluminum aerospace forging. Using our modeling tools, we were able to capture the significant post-quench distortion in the forging, which is shown in the figure below. A rapid immersion quench, evenly applied, results in a very distorted and bowed output.
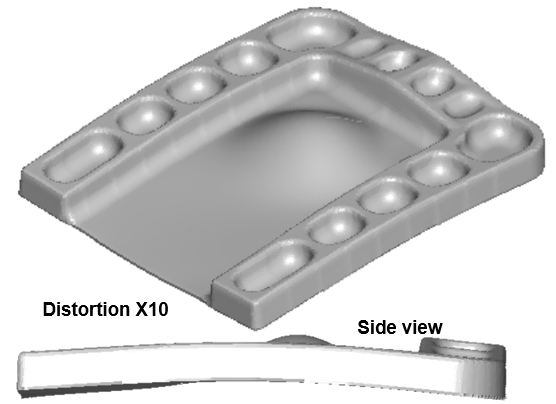
Illustration of predicted distortion of an aluminum forging during quench
Clearly, alternatives needed to be explored to mitigate the large amount of distortion. We considered several possibilities: slowing the cooling on one side (with a coating), removing the webbing before the quench (with machining), increasing the thickness of the webbing, or redesigning the forging with back-to-back symmetry by putting two parts into one forging. However, real-time physical experimentation of multiple options would be expensive and time consuming.
With modeling tools, we were able to quickly and effectively identify the most promising alternatives for improvement.
In this case, the biggest improvement came from removal of the webbing. The webbing is necessary for some of the initial forging operations, but does not need to be retained. It does not provide any coverage of the customer’s final post-machined part, and it is not necessary for heat treatment. Removing the webbing (i.e. cutting it off) prior to heat treatment requires an extra machining operation, but that is relatively inexpensive. As seen in the next figure, removing the webbing before quench resulted in a post-quench distortion that is remarkably reduced.
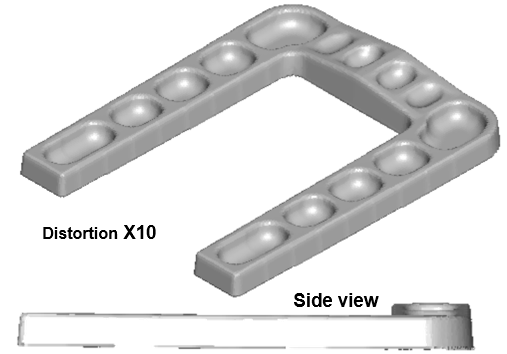
Illustration of predicted distortion for an alternate aluminum forging quench process that involves removing the webbing from the center prior to solution heat treatment and quench
The advantage of pre-production simulation is that problems can be found and solved beforehand, and the robustness of the proposed solutions can be tested and quantified.
Post-quench distortion is driven by bulk residual stress. That stress is created during the quench due to uneven cooling. Near surface cooling is much faster than the internal cooling of the part. This is unavoidable. However, using our modeling tools, the quench-induced residual stress can be predicted.
This predicted bulk residual stress is useful in follow-up simulations of post-machining distortion and part performance. The next figure shows the principal bulk residual stress as seen in section planes throughout the forging. Note that the residual stress reaches as high as 20.0 ksi in this aluminum 7075 simulation. This residual stress is post-quench and absent of any mechanical stress relief operations that are typically performed in subsequent steps.
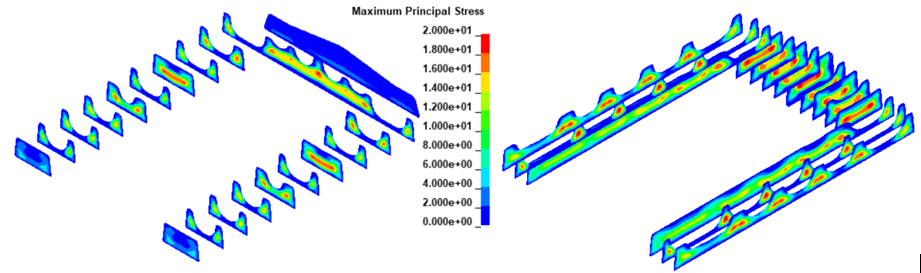
Illustration of predicted post-quench bulk residual stress in an aluminum forging
If this example relates to your production challenges, or if you have any questions about how these results might affect your projects, please do not hesitate to contact us. We would also be happy to answer any questions that you may have.
Machining distortion modeling with multi-step models including residual stress
Distortion of finished parts during machining is a significant problem which typically results from release and redistribution of residual stress in the material once the part is unclamped from the machine table. If not accounted for,
This case study focuses on machining modeling of a representative aircraft specimen using multi-step finite element analysis. Machining modeling was used to identify a machining strategy that requires less machine time (e.g., fewer part set-ups) to arrive at the final geometry, while also reducing the distortion of the finished part. The results illustrate how multi-step machining models can be used to provide upfront estimates of distortion, as well as guidance to optimize machining processes and obtain improved machining outcomes.
The part geometry considered in this case study is shown in Figure 1, and was designed to be representative of an aircraft part. The overall dimensions are 25 x 10 x 2.5 inches. The pockets, stiffener walls, holes, and tapering along the 25 inch dimension and 2.5 inch dimension provide a complex and representative geometry. The part is assumed to be machined from a 27 x 12 x 3.5 inch plate of aluminum alloy 7050-T7451 (stress relieved by stretching). While this material state typically exhibits low levels of residual stress, distortion during machining can still occur depending on the part geometry, machining strategy, and required tolerances.
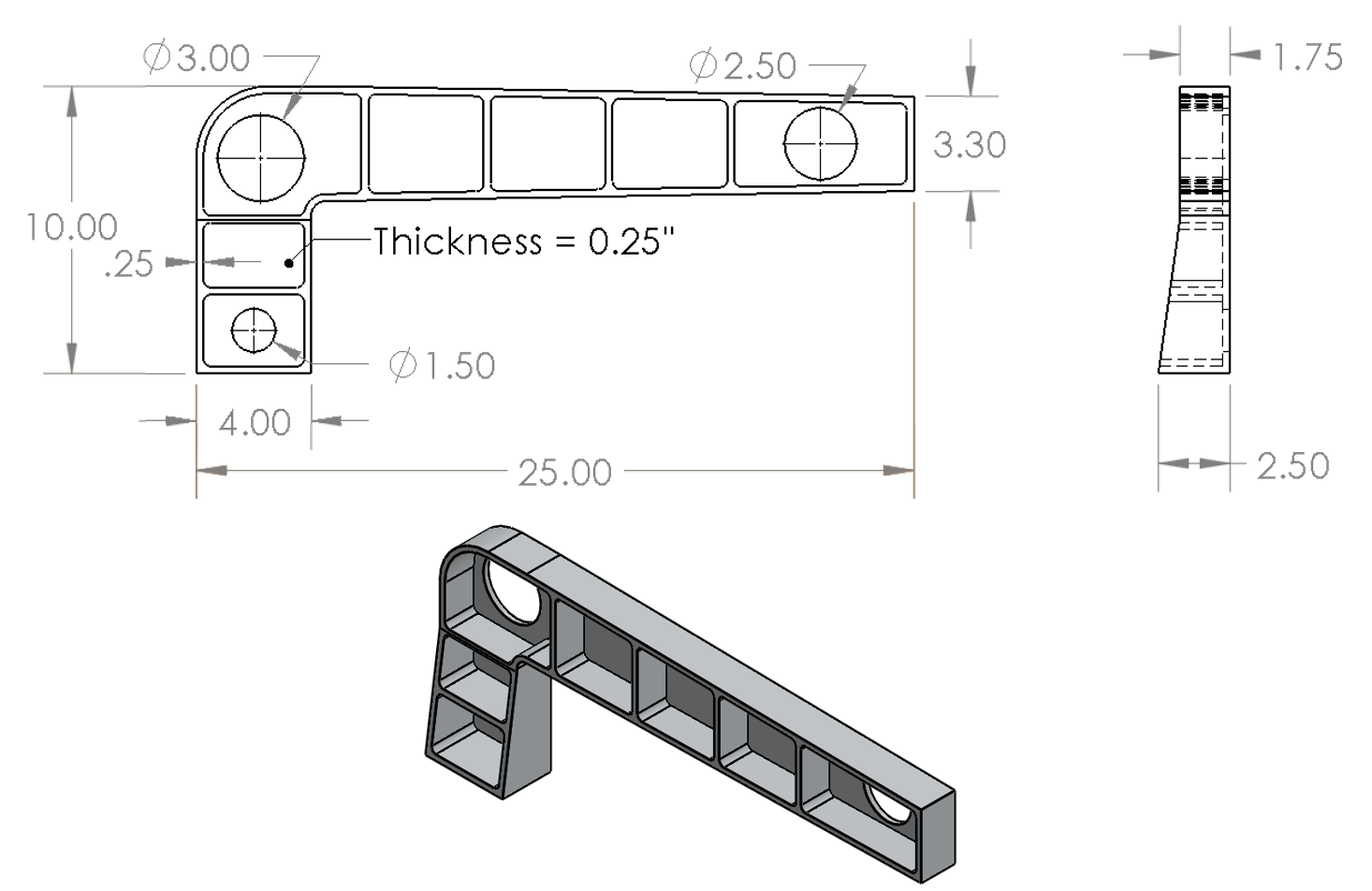
Part geometry (dimensions in inches)
The plate considered for machining this part provides extra material coverage on all sides. Figure 2 shows the amount of machining cover on each side, given the part is aligned with the mid-thickness of the stock plate with equal spacing relative to the sides of the stock. One inch of extra material is available on all sides when looking from a top view, while one-half inch of extra material is available along the thickness direction.
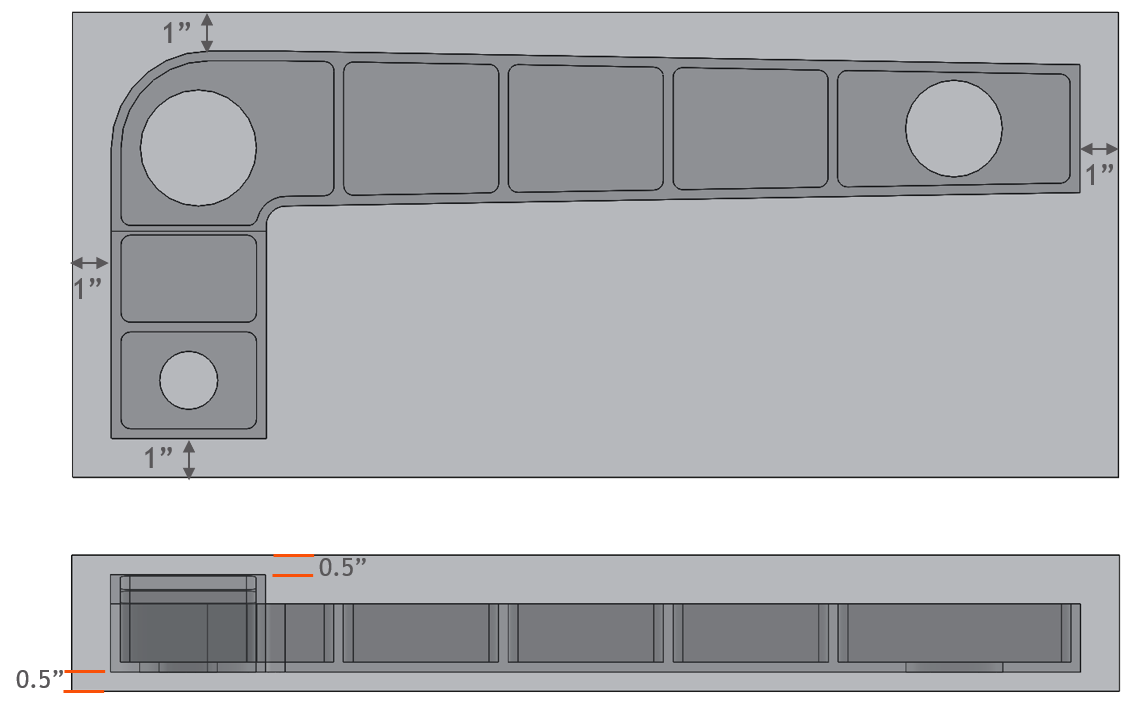
Part geometry within stock material when placed at the mid-thickness of the plate
The assumed residual stress in the stock plate material is shown in Figure 3. This is based on slitting method results published in [1] for 3-inch-thick plate of aluminum alloy 7050-T7451. The residual stress distributions are relatively symmetric and were normalized and scaled for the specific stock plate thickness used in the current study (3.5 inches). The rolling direction of the stock plate was assumed to be along the 27-inch dimension of the plate.
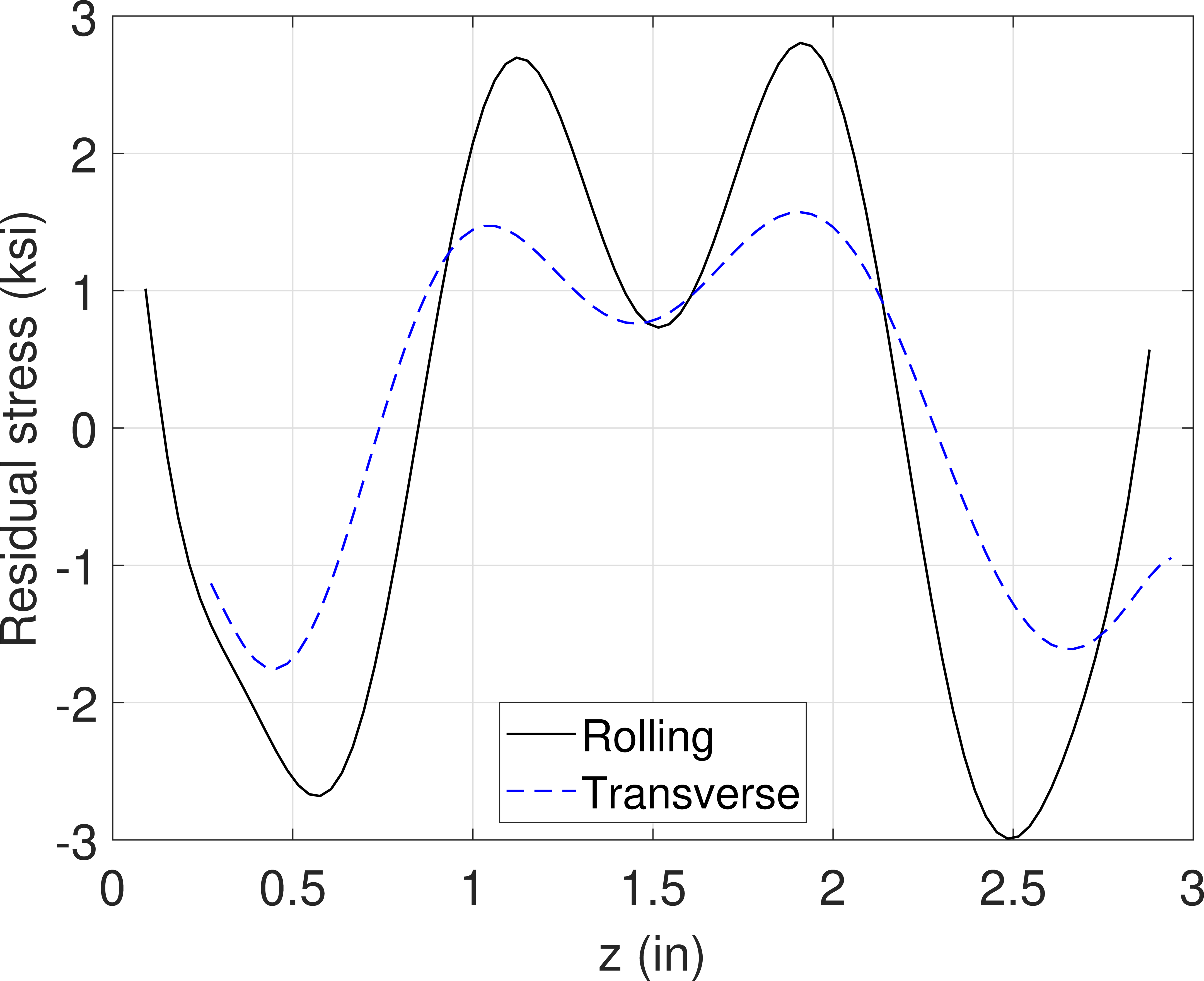
Residual stress measured in aluminum alloy 7050-T7451 plate (adapted from [1])
The baseline machining strategy considered is illustrated in Figure 4, in which the part is placed near the top surface of plate. Step 1 includes a rough machining pass on the bottom surface of the plate to obtain a flat surface for subsequent machining. Then, the part is flipped on the machine table. Step 2 involves an initial rough machining of the pockets and stiffener walls. Step 3 flips the part once again and finalizes machining of the bottom flat surface of the part. Finally, the part is flipped for the last time, and machining of the pockets, holes, and stiffener walls is finalized to arrive at the final geometry. This machining strategy includes a total of 3 flips on the machine table.

Part placement and baseline machining strategy
Multi-step finite element models were employed to obtain estimates of the distortion and residual stress at the end of each machining step. For brevity, the displacement of the finished part only (step 4) is shown here. Figure 5 shows a contour plot of the displacement along the z-axis (U3, perpendicular to the bottom flat surface of the part) on a scale that varies from -0.025 to 0.025 inches. The displacement U3 range (maximum minus minimum value) is about 0.030 inches. Maximum displacement is observed near the corner region of the part that contains the 3-inch diameter hole (shown in Figure 1).
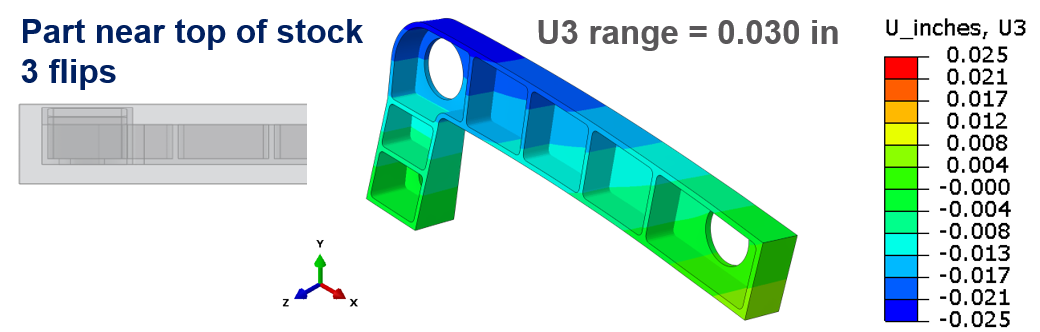
Contour plot of displacement along the z-axis (U3) for the finished part from the baseline strategy
Modeling was performed to simulate many different machining approaches. The optimal machining strategy places the part at the bottom surface of the stock plate as illustrated in Figure 6. The first step involves rough machining of the pockets and stiffener walls. The part is then flipped, and final-machined on the bottom flat surface. The second and final flip on the machine table provides the setup to final-machine the pockets, holes, and stiffener walls. This machining strategy uses a total of 2 flips (one less than the previous strategy).
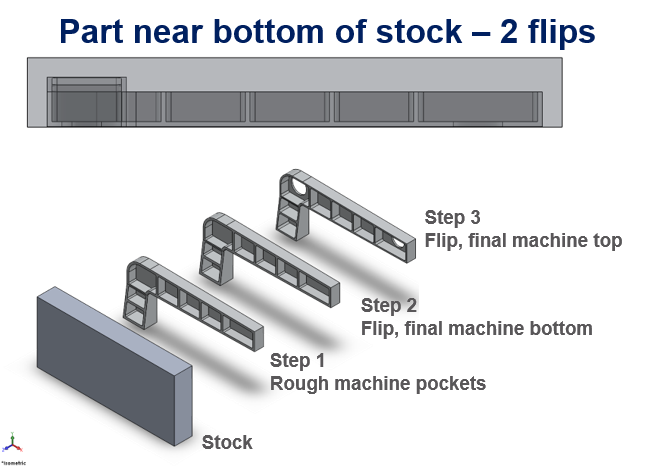
Part placement and optimized machining strategy
The part distortion for the optimized machining strategy is shown in Figure 7 (using the same color scale as in Figure 5). Compared to the baseline strategy (Figure 5), a different displacement pattern is observed, although the maximum values are near the same region (i.e., near the corner of the part with the 3-inch diameter hole). The displacement range is 0.013 inches for the optimized machining strategy, which is significantly lower than observed from the baseline approach (0.030 inches). It is important to note that the optimized strategy (which places the part near the bottom of the stock) not only provided a finished part with lower amount of distortion, it also required less machine time (fewer flips), which represents an improvement in efficiency of the machining process.
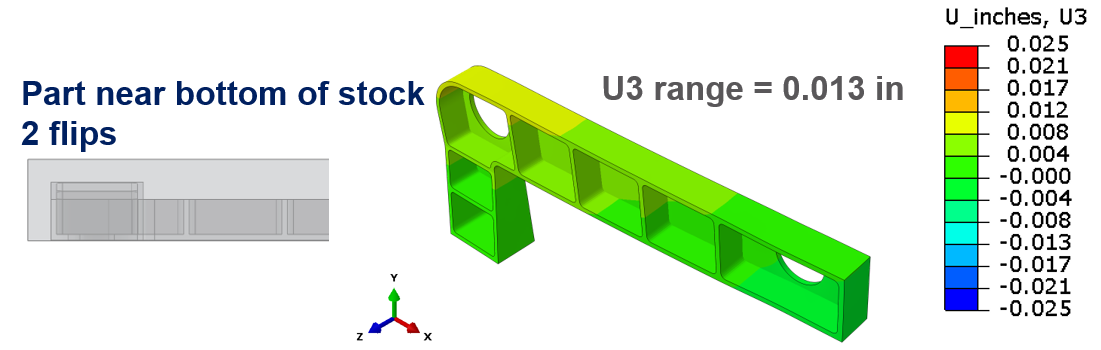
Contour plot of displacement along the z-axis for the finished part from the optimized strategy
This case study considered multi-step machining models of a representative aircraft specimen, including the residual stress in the incoming stock material, to assess the distortion of the finished part. Two different machining strategies were presented, which included differences in part placement within the stock material, and sequence of machining steps. The results identify an optimized machining strategy that uses fewer flips on the machine table (setups) to arrive at the final geometry, while also reducing the distortion of the finished part. The results illustrate how multi-step machining models can be used to provide upfront estimates of distortion and guidance to optimize machining processes in order to obtain improved outcomes. Please contact us for additional information.
BAMpF®
BAMpF® (Broad Application for Multipoint Fatigue) enables fatigue crack growth analysis of parts with non-standard geometry, loading, and residual stress conditions through the implementation of multipoint fracture mechanics (MPFM). This user-friendly software environment provides structural analysts and engineers a tool to accurately and efficiently complete challenging fatigue crack growth problems.
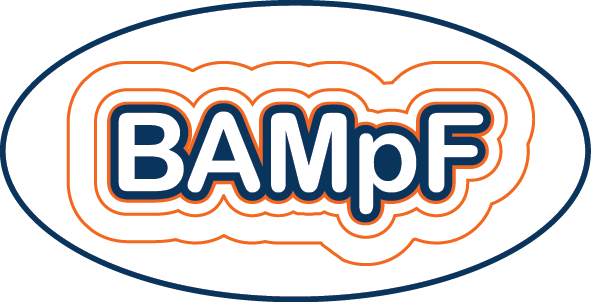
Starting from an assumed initial flaw, BAMpF® implements a multi-point fracture mechanics approach that allows crack shapes to evolve naturally as a function of the underlying, spatially varying stress fields and stress intensity factors. As illustrated in the figure below, the user specifies the number of points along the crack front to be used in the analysis. For each individual point, BAMpF® queries the stress intensity factor specific to the part geometry and loading through an interface with StressCheck® (a leading finite element software tool), provides the necessary inputs to AFGROW (a leading fatigue life assessment tool), and stores the expected fatigue crack growth for a given number of cycles. BAMpF® then combines the growth of each individual point into a new crack shape that serves as the starting point for the next increment of the analysis. This process is repeated until the fatigue crack reaches a critical size.
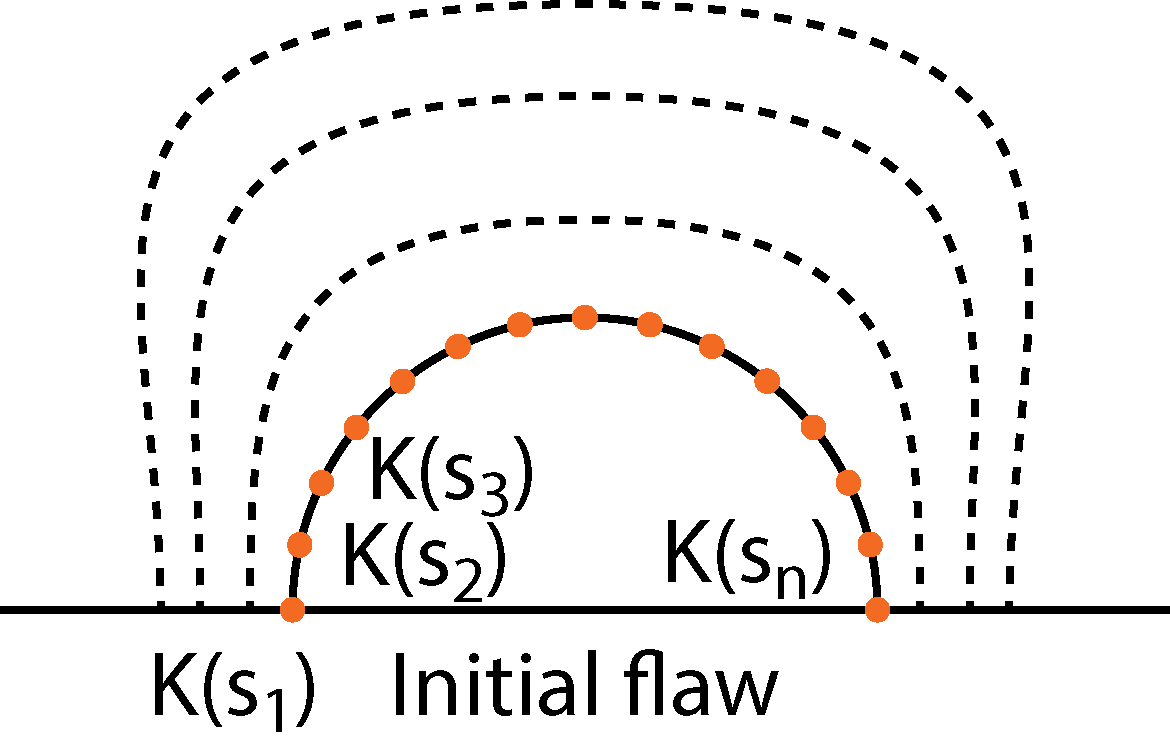
Illustration of multipoint fracture mechanics approach to defining individual control points around the crack front
Multipoint fracture mechanics improves the accuracy of fatigue crack growth calculations relative to traditional analysis methods by eliminating assumptions and constraints related to the shape of the crack (e.g. elliptical crack shapes are not required by MPFM). The use of MPFM is especially important when non-standard conditions like complex loading, complex geometry, and/or residual stresses are present as these factors tend to drive the evolution of the fatigue crack shape away from the circular/elliptical constraints imposed by the traditional analysis methods.
BAMpF® provides a straightforward approach for including residual stress in crack growth assessments. Residual stress input data for BAMpF® may come from measurement or process modeling (e.g., ERS-Toolbox®). The MPFM capabilities in BAMpF® enable accurate fatigue analysis of parts with laser shock peening (LSP), cold-expanded (CX) holes, of other bulk residual stress fields. For example, the figure below shows a comparison between the predicted (BAMpF®) and experimentally observed fatigue crack shape for a cold expanded hole test specimen.
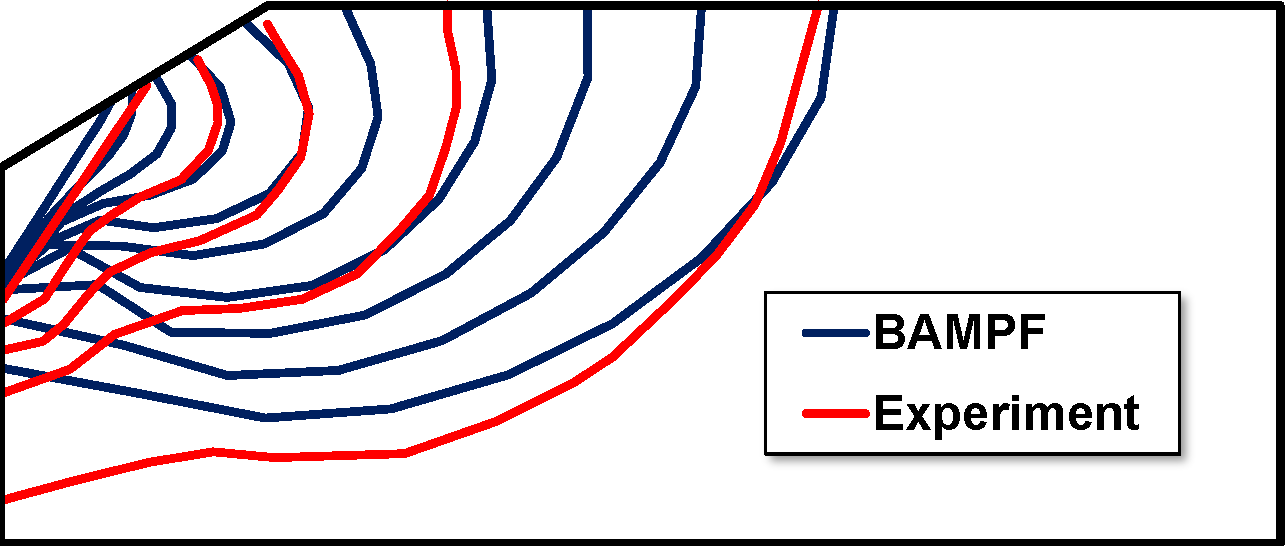
Fatigue crack growth analysis (BAMpF®) and experimental results for a cold expanded hole test specimen
Some of the key features and capabilities of BAMpF® include:
• Natural fatigue crack shape progression
• Fully 3D analysis
• Complex loading
• Multi-crack interactions and link-up
• Residual stress
BAMpF® has received software certification from the United States Airforce.
For more information about the study described above, our fatigue analysis and testing abilities, our residual stress engineering services, or to place an order for BAMpF® related goods and services, please contact us.
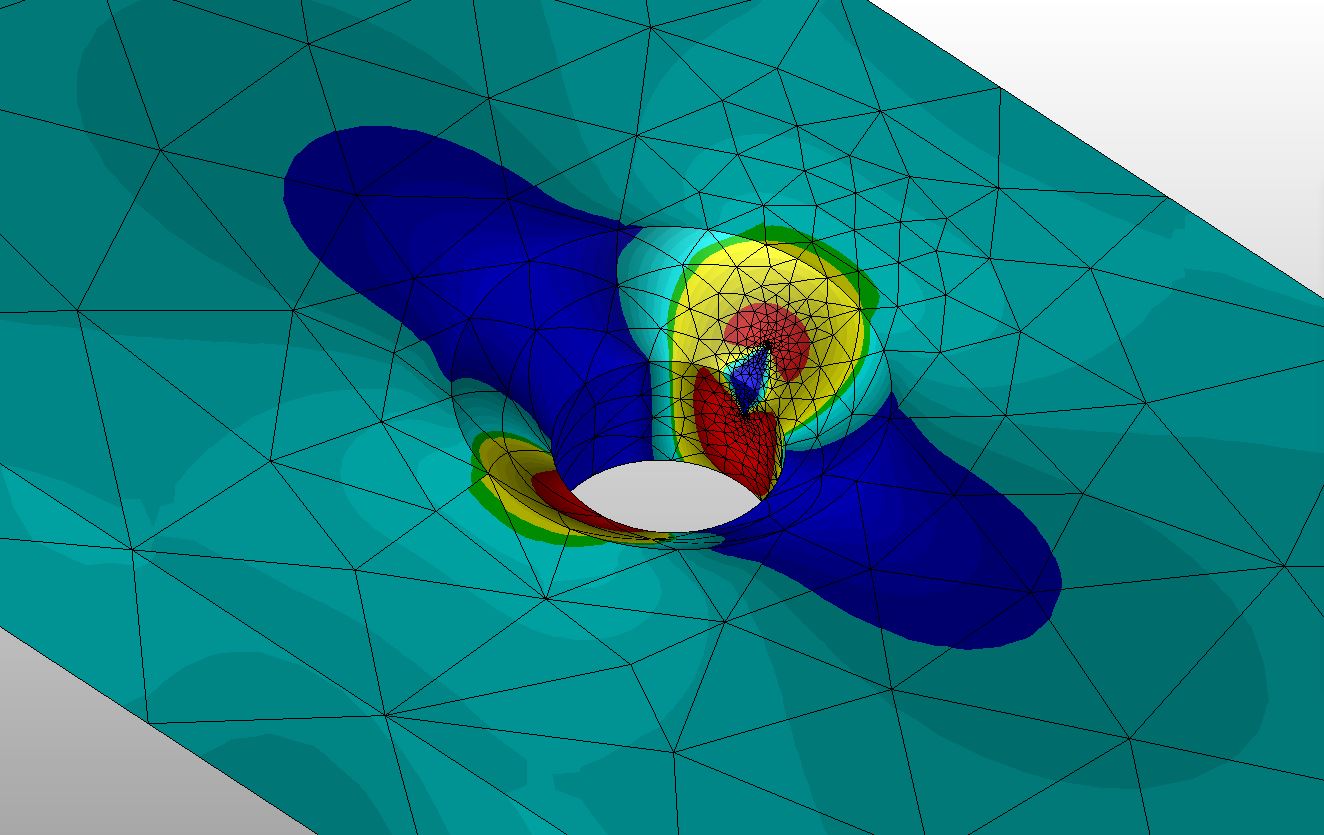
Image from a BAMpF® analysis showing the stress in a specimen with a small crack near a hole
Special thanks to our partners:
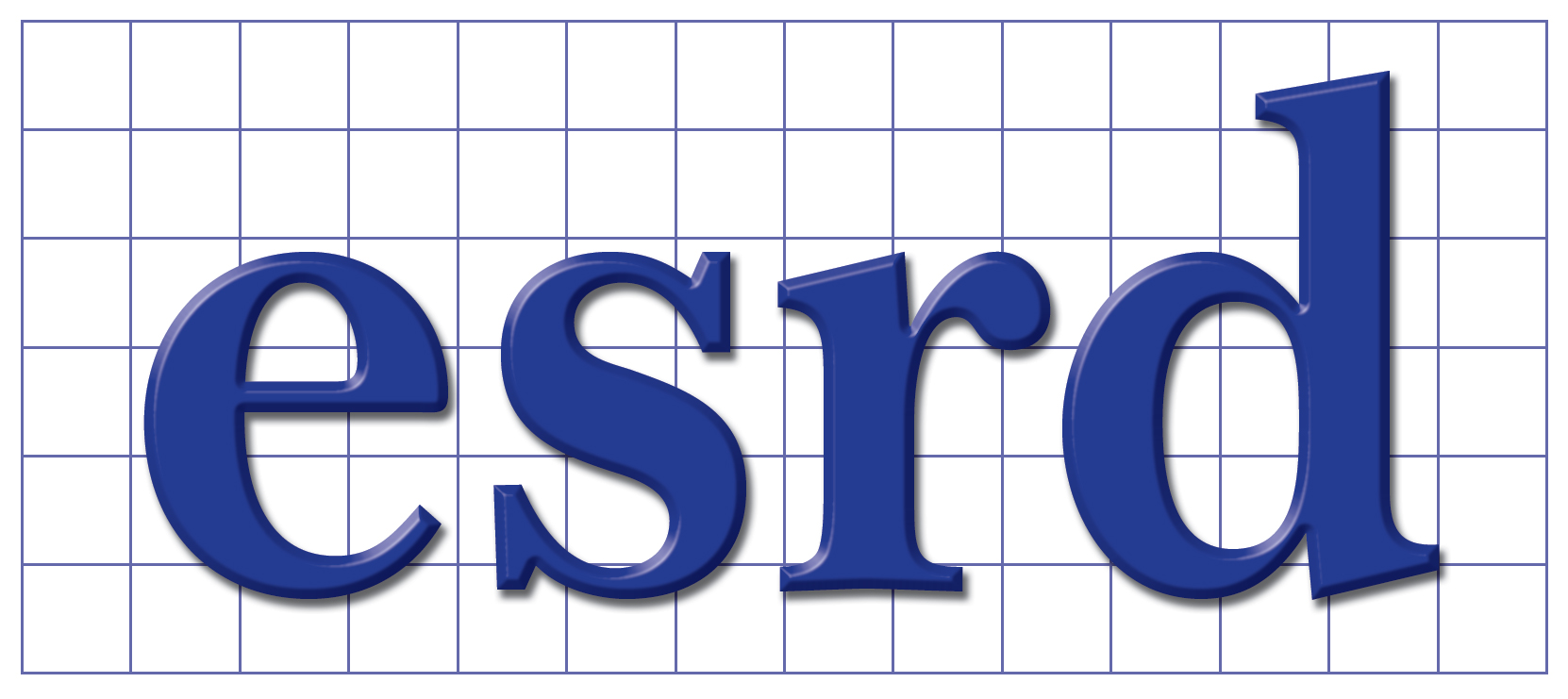
ESRD’s flagship software product, StressCheck® Professional, is an advanced FEA tool having numerous unique technical capabilities
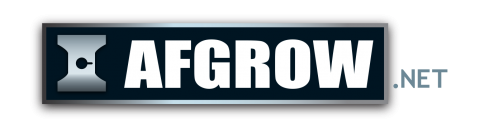
AFGROW is a Damage Tolerance Analysis (DTA) framework that allows users to analyze crack initiation, fatigue crack growth, and fracture to predict the life of metallic structures
Case Study: Cold hole expansion process modeling
Cold hole expansion (CX or cold expansion for short) of fastener holes is a technique that has been widely used in the aircraft industry to improve the fatigue performance of structural components. The cold hole expansion process introduces compressive residual stress near the vicinity of the hole that slows crack growth and can significantly improve fatigue performance. The process induces plastic deformation near the hole from pulling an oversized mandrel through the hole. The elastic recovery of the surrounding material results in compressive residual stress near the hole bore surface that is balanced by tensile residual stress farther from the hole. The benefits of cold expansion on fatigue performance have been illustrated in several research studies. A correlation of fatigue crack growth at cold expanded holes is illustrated in [1].
This case study focuses on nonlinear process modeling of cold expansion using finite element analysis. An aluminum coupon with dimensions 50.8 x 50.8 x 6.35 mm (2.0 x 2.0 x 0.25 inch) and a hole in the center of diameter 12.12 mm (0.477 inch) is considered. The hole undergoes a 3.16% applied expansion during the cold hole expansion process, i.e., at maximum expansion, the hole radius is enlarged by 3.16%. Figure 1 shows the coupon geometry.
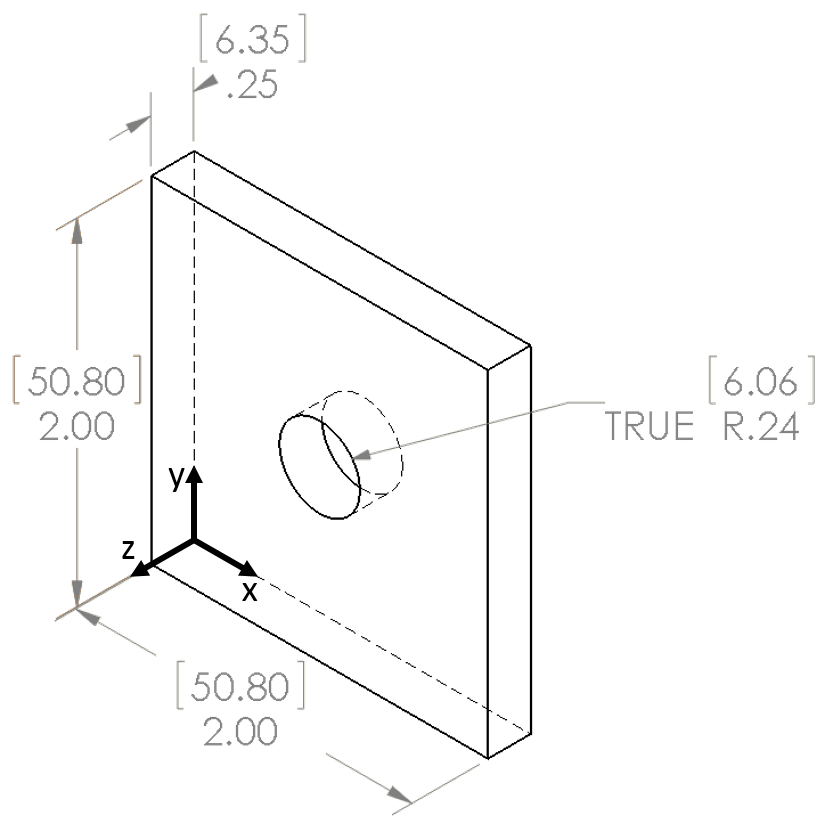
Coupon geometry used for cold hole expansion process modeling. Non-bracketed dimensions are in inches and bracketed dimensions are in mm.
The analysis considers the elastic-plastic behavior of the material, and uses a true stress-strain curve obtained from experimental tests using the specific material considered here. The material curve describes the material behavior under loading, and characterizes the hardening of the material as it is loaded past its initial yield strength.
Typically, fatigue cracks initiate at the edge of fastener holes. The hoop residual stress combines with applied loading to alter the crack driving force, and is important in a fatigue crack growth analysis considering cold expanded holes. The process model used here provides hoop residual stress as shown in Figure 2. A through-thickness map taken at the y = 25.4 mm (1.0 inch) plane is shown in Figure 2a, where high compressive residual stress is observed near the edges of the hole, while tensile residual stress arises farther from the hole edge to satisfy mechanical equilibrium. Figure 2b also shows the hoop residual stress, but at a xy midplane (z = 3.175 mm (0.125 inch)). The high compressive residual stress is localized near the hole edge, and is approximately axisymmetric. Taking a line plot of the hoop residual stress along a specified path provides more quantitative results, as illustrated in Figure 2c, where the path taken is at the y = 25.4 mm plane and at the mid-thickness of the plate (z = 3.175 mm (0.125 inch)). The curve in this plot is for the right side of the hole only (x > 30 mm).
The distribution shows peak compressive residual stress at the hole edge that decays and eventually becomes tensile. The peak compressive residual stress at the hole edge is -480 MPa (approximately -70 ksi). The size of the compressive residual stress zone, i.e., the distance at which the RS crosses 0 is about 4.4 mm (0.17 inch), which corresponds to about 0.7R (R = radius of the hole). Beyond the compressive residual stress zone, tensile residual stress develops with peak of about 115 MPa (approximately 17 ksi) at 7.2 mm (0.28 inch) away from the hole edge, which corresponds to 1.1R.
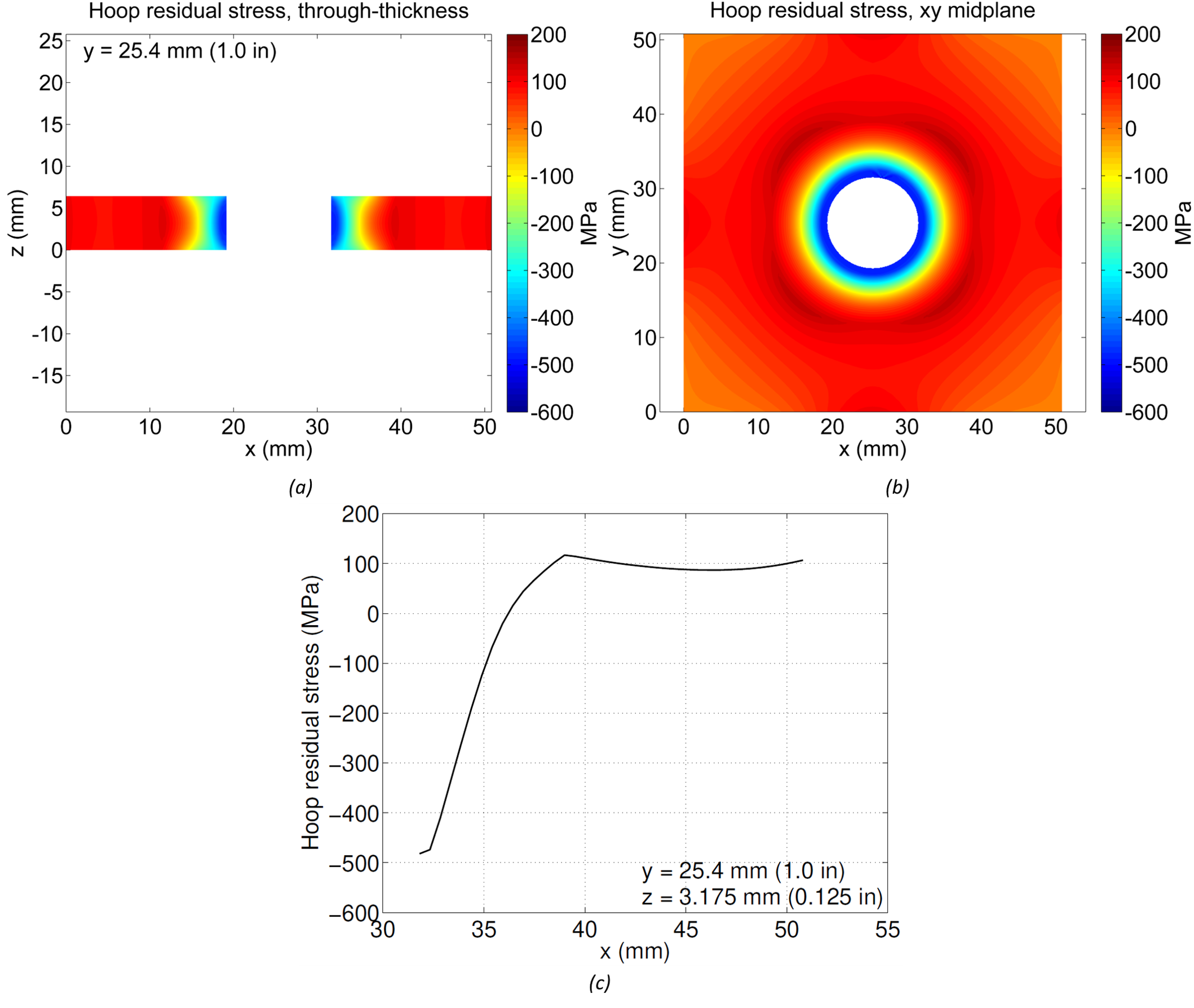
Hoop residual stress from process model with 3.16% applied expansion a) through thickness of coupon, b) on xy midplane at z = 3.175 mm (0.125 inch), c) line plot along x-direction at y = 25.4 mm, z = 3.175 mm
Having the process model established above, it is useful to evaluate the effect of the radial applied expansion level in the resulting hoop residual stress. Running the process model with a 4.16% applied expansion provides hoop residual stress as shown in Figure 3. Maps of the hoop residual stress are shown in Figure 3a and Figure 3b, and show slightly higher magnitudes of residual stress compared to the results in Figure 2a and Figure 2b. Figure 3c shows the line plot along the same path as for the previous model, and compares the results obtained with both levels of expansion. Overall, the higher level of expansion resulted in about 5% increase in peak compressive residual stress at the hole edge, and a 10% increase in the size of the compressive residual stress zone around the hole.

Hoop residual stress from process model with 4.16% applied expansion a) through thickness of coupon, b) on xy midplane at z = 3.175 mm (0.125 inch), c) line plot along x-direction at y = 25.4 mm, z = 3.175 mm
This case study focuses on process modeling using finite element analysis for prediction of residual stress from cold expansion of fastener holes. A process model is developed to simulate the expansion of the hole due to the mandrel pull-through operation, and the resulting hoop residual stress after elastic recovery of the material is presented. The model results show high compressive residual stress at the edge and vicinity of the hole, which decays with distance from the hole and eventually becomes tensile. Increasing the amount of applied expansion used in the model causes an increase in peak compressive residual stress at the hole edge, as well as an increase in size of the zone of compressive residual stress near the hole. Although only the hoop residual stress results are shown here, the process model provides full field solutions, and allows for evaluating residual stress from cold expansion through numerical simulation.
For more information about the study described above, our fatigue testing abilities, or any of our residual stress measurement techniques, please contact us.
[1] Stuart, D. H., Hill, M. R., and Newman Jr, J. C., 2011, “Correlation of one-dimensional fatigue crack growth at cold-expanded holes using linear fracture mechanics and superposition,” Eng. Fract. Mech., 78(7), pp. 1389–1406.
An Uncertainty Estimator for Slitting Method Residual Stress Measurements Including the Influence of Regularization
This paper describes the development of a new uncertainty estimator for slitting method residual stress measurements. The new uncertainty estimator accounts for uncertainty in the regularization-based smoothing included in the residual stress calculation procedure, which is called regularization uncertainty. The work describes a means to quantify regularization uncertainty and then, in the context of a numerical experiment, compares estimated uncertainty to known errors. The paper further compares a first order uncertainty estimate, established by a repeatability experiment, to the new uncertainty estimator and finds good correlation between the two estimates of precision. Furthermore, the work establishes a procedure for automated determination of the regularization parameter value that minimizes total uncertainty. In summary, the work shows that uncertainty in the regularization parameter is a significant contributor to the total uncertainty in slitting method measurements and that the new uncertainty estimator provides a reasonable estimate of single measurement uncertainty.